Супер аустенитная нержавеющая сталь в настоящее время является наиболее подходящим материалом для мокрого процесса десульфуризации дымовых газов.
Этот процесс также является наиболее часто используемым сегодня в мире для обработки супераустенитной нержавеющей стали. Из многих технологий обессеривания на нее приходится 80% от общей установленной мощности обессеривания. Это всегда выше постоянного диапазона.
Мокрая десульфуризация дымовых газов из известняка и гипса - это наиболее часто используемый процесс десульфуризации при влажной десульфуризации дымовых газов.
Коррозионная среда внутри системы влажной сероочистки дымовых газов жесткая, а внутреннее оборудование системы легко подвергается коррозии. Проведение качественных антикоррозионных работ - важная мера для обеспечения безопасной и стабильной работы завода и контроля электростанции для предотвращения выбросов.
Супераустенитная нержавеющая сталь богата большим количеством Cr, Ni, Mo и соответствующим количеством легирующих элементов, таких как N и Cu, устойчива к разбавленной серной кислоте и точечной коррозии, стойкость к щелевой коррозии эквивалентна сплавам на основе никеля, имеет отличные характеристики. механические свойства и стойкость к коррозии. Среди них Мо может улучшить общую коррозионную стойкость супераустенитной нержавеющей стали, особенно стойкость к точечной коррозии хлорид-ионами. Супераустенитная нержавеющая сталь 6% Mo имеет лучшую коррозионную стойкость в кислых растворах, содержащих ионы хлора, и больше подходит для использования в системе обессеривания дымовых газов.
Технологическая схема технологической системы мокрой сероочистки дымовых газов
Основным технологическим процессом мокрого обессеривания дымовых газов из известняка и гипса является следующий: после того, как дымовые газы котла очищаются электрофильтром и нагнетаются дожимным вентилятором, а затем охлаждаются теплообменником дымовых газов, они попадают в абсорбционную башню. Известняковая суспензия распыляется в абсорбционной башне для реакции с дымовым газом для удаления SO2, SO3, HCl и HF из дымового газа. Известняковая суспензия переносится в слой распыления через циркуляционный насос для суспензии, а затем распыляется через сопло, так что суспензия и дымовой газ могут полностью контактировать и полностью реагировать. Обессериваемый дымовой газ нагревается через теплообменник дымового газа для увеличения коэффициента диффузии и, наконец, выбрасывается в дымоход, который выбрасывается в атмосферу.
В абсорбционной башне в результате сложной химической реакции между известняковой суспензией и диоксидом серы в дымовых газах образуется гипс. Эта часть гипсовой суспензии проходит через нагнетательный насос абсорбционной башни и поступает в систему обезвоживания гипса. Система дегидратации в основном включает гипсовый циклон, ленточный вакуумный осушитель и распределитель шлама. Поток дымовых газов после реакции затуманивается туманоуловителем для удаления капель жидкого тумана в дымовых газах. В то же время, техническая вода электростанции должна время от времени использоваться для промывки туманоуловителя. Промывка туманоуловителя преследует две основные цели: одна - предотвратить засорение туманоуловителя, а другая - использовать промывочную воду в качестве дополнительной воды для стабилизации уровня жидкости в абсорбционной башне.
На выходе из абсорбционной башни дымовой газ обычно охлаждается примерно до 50 ° C и содержит большое количество насыщенного водяного пара. После прохождения через теплообменник дымовых газов дымовой газ нагревается до температуры выше 80 ℃, в основном для улучшения высоты подъема и диффузионной способности дымового газа, тем самым устраняя явление гипсового дождя. Наконец, чистый дымовой газ, который соответствует стандартам выбросов дымовых газов электростанции, сбрасывается в атмосферу через дымоход.
Применение супер аустенитной нержавеющей стали в технологической системе мокрой сероочистки дымовых газов
На некоторых электростанциях дымовой газ, работающий на угле, проходит через абсорбционную башню и сбрасывается непосредственно в дымоход без нагревателя дымового газа (WGGH). Этот тип дымохода становится дымоходом мокрого типа. На некоторых электростанциях после абсорбционной башни устанавливается не нагреватель дымовых газов, а мокрый электрический пылеуловитель (WESP). Дымовой газ проходит через мокрый электрический пылеуловитель и выводится через дымоход. Видно, что коррозионная среда мокрого дымохода, мокрого электрофильтра и нагревателя дымовых газов эквивалентна.
Мокрые дымоходы облицованы антикоррозийными металлическими материалами, в том числе супераустенитной нержавеющей сталью, сплавами на основе никеля, композитными пластинами из титановой стали и т. Д .:
- Сплавы на основе никеля обладают хорошей коррозионной стойкостью. Типичными являются сплав Nicrofer 5923 h Mo-59, сплав Nicrofer 3127h Mo-31, сплав Cronifer 1925 h Mo-926 и т. Д.
- Титан обладает хорошей стойкостью, плохими сварочными характеристиками и низкой прочностью.
- Цена на супер-аустенитную нержавеющую сталь намного ниже, чем на сплавы на основе никеля. Он обладает отличными сварочными характеристиками и может напрямую свариваться с углеродистой сталью. Он обладает превосходными механическими свойствами и производительностью обработки и является более подходящим материалом.
254SMo это разновидность, обычно используемая в стали 6Mo. Обладает отличной стойкостью к точечной коррозии. Он широко используется в промышленном технологическом оборудовании, богатом ионами галогена, например в морской воде. Его можно использовать для замены дорогих материалов, таких как сплавы на основе никеля или титан. Есть также несколько применений в системах обессеривания дымовых газов.
В этой статье на примере 254SMo изучается коррозионная стойкость супераустенитной нержавеющей стали 6Mo в дымоходах и нагревателях дымовых газов.
Тест кривой поляризации
Базовые приготовления
Испытательными материалами являются 316L, 317L и 254SMo, и их основные компоненты показаны в таблице 1.

Трубки из нержавеющей стали из трех материалов были механически вырезаны, чтобы получить образцы размером 20 мм × 5 мм × 0,7 мм. Образцы были отполированы до наждачной бумаги 01# вокруг образцов.
После ультразвуковой очистки в течение 15 минут и пассивации концентрированной азотной кислотой в течение 30 минут, задняя сторона была приварена медной проволокой, а затем ацетон очищает смазку, прикрепленную к поверхности электрода, и, наконец, нерабочая поверхность залита эпоксидной смолой, рабочая поверхность составляет 20 мм. × 5 мм.
Упакованные электроды шлифуются с различной степенью шероховатости от грубой до мелкой, а затем полируются до наждачной бумаги 01# для использования.
Метод испытания
В тесте используется трехэлектродная система. Рабочий электрод - самодельный планарный электрод из измеряемого материала, электрод сравнения - насыщенный каломельный электрод (SCE), вспомогательный электрод - платиновый электрод. Потенциальная скорость сканирования составляет 1 мВ / с, а частота сканирования - 2 Гц. Испытательная среда представляет собой конденсат дымового газа (pH = 1,84), а затем к конденсату дымового газа добавляется NaCl для приготовления двух различных растворов испытательной среды с концентрацией Cl с концентрацией 1000 и 40000 мг / л, при этом концентрации других ионов остаются неизменными. .
Температура испытания выбрана равной 50 ℃, а точность контроля температуры - 0,1 ℃. Потенциал питтинга материала проверяли методом динамического сканирования потенциала, и испытание начинали с -400 мВ относительно электрода сравнения до тех пор, пока анодный ток не достигал 0,2 ~ 1,0 мА / см2.
Каждый материал тестируется трижды в одних и тех же рабочих условиях, чтобы убедиться, что результаты испытаний верны и надежны.
Результаты теста
На рис. 1 показаны поляризационные кривые для нержавеющей стали 316L и нержавеющей стали 317L в конденсате дымового газа 1000 мг / LCl и сверхаустенитной нержавеющей стали 254SMo в конденсате дымового газа 40000 мг / LCl.
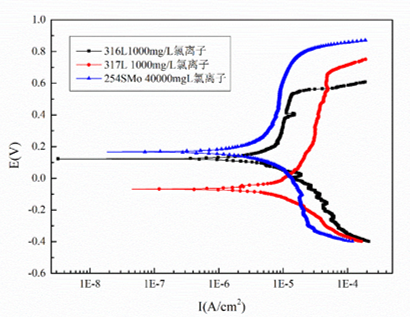
Можно видеть, что точечный потенциал 316L ниже, чем у 317L, когда концентрация Cl в конденсате дымовых газов составляет 1000 мг / л.
Потенциал точечной коррозии нержавеющей стали обычно снижается с увеличением концентрации Cl в растворе. Однако, когда концентрация Cl в конденсате дымового газа достигает 40000, потенциал питтинга 254SMo все еще очень высок и находится в чрезмерно пассивированном состоянии. Видно, что 254SMo имеет лучшую стойкость к точечной коррозии в конденсате дымовых газов с более высокой концентрацией Cl.
Содержание элементов сплава, таких как Cr и Mo, в 254SMo относительно высокое. Среди них Cr является основным элементом, образующим пассивирующую пленку. Увеличение содержания Cr может сделать пассивирующую пленку более стабильной; и более высокое содержание Mo может привести к тому, что стальная поверхность будет иметь защитную пленку MoOCl2, которая образуется в среде, где присутствует Cl-, тем самым эффективно предотвращая проникновение Cl- в пассивирующую пленку.
Величина размерного тупого тока на поляризационной кривой может характеризовать равномерную скорость коррозии нержавеющей стали. Согласно закону Фарадея, существует строгая количественная зависимость между показателем тока коррозии и индексом массы. Чем больше коррозионный ток, тем быстрее скорость коррозии металла, что отражает сопротивление материала. Тем хуже показатели равномерной коррозионной стойкости. Объясните показатели равномерной коррозионной стойкости 254SMo>316L>317L.
Тестирование на месте
Скорость коррозии трех материалов из нержавеющей стали показана на рисунке 2. Как видно из рисунка, скорость коррозии 317L немного выше, чем у 316L, соответственно 0,081 мкм / год и 0,069 мкм / год, что является То же, что и результаты теста кривой поляризации.
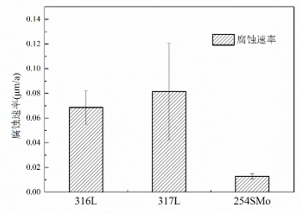
Скорость коррозии 254SMo намного меньше, чем у двух предыдущих, и составляет 0,013 мкм в год. Из-за наличия ошибок взвешивания коррозия 254SMo практически незначительна. Видно, что 254SMo имеет лучшую стойкость к равномерной коррозии в реальных условиях эксплуатации.
Резюме
- 1) Супераустенитная нержавеющая сталь имеет хорошую стойкость к точечной коррозии Cl в кислотном растворе, и ее цена ниже, чем у сплава на основе никеля, который больше подходит для применения в системе дымовых газов мокрой сероочистки;
- 2) Испытание градиентной кривой и испытание на месте показывают, что 254SMo имеет превосходную коррозионную стойкость в конденсате дымовых газов и может соответствовать условиям работы такого оборудования, как дымовая труба и нагреватель дымовых газов;
- 3) Супер-аустенитная нержавеющая сталь 904L и AL-6XN может хорошо использоваться в абсорбционных колоннах обессеривания, и это хорошее направление выбора материала для абсорбционных колонн для замены неметаллических материалов материалами из сплавов.