Эксперименты и результаты дуплексной сварки труб из нержавеющей стали
Человек производит и использует дуплексную нержавеющую сталь почти 80 лет. Ранние сплавы, такие как ковкий сплав 329 и литой сплав CD4MCu, содержали гораздо больше феррита, чем аустенита.
Люди не обращают внимания на важность азота. Многие сплавы содержат очень мало азота, поэтому, когда термическая обработка не выполняется после сварки, зона термического влияния этих сплавов обычно становится хрупкой и имеет плохую коррозионную стойкость. Металл шва газовой сварки также имеет этот дефект.
В 1980-х годах важность азота для дуплексные трубы из нержавеющей стали был полностью признан, и обычно указывались минимальные требования к содержанию азота. За счет добавления соответствующего содержания азота к основному металлу и использования присадочного металла сварного шва с повышенным содержанием никеля сварная деталь может иметь примерно равное количество аустенита и феррита в сварном состоянии, что значительно улучшает механические свойства Повышенная коррозионная стойкость.
Ошибки
Необоснованные характеристики основного металла
В течение последних 25 лет наиболее распространенной дуплексной нержавеющей сталью является сплав под названием 2205. Почти во всей литературе для описания этого сплава используется диапазон состава UNSS31803. Однако в UNS S31803 минимальное содержание азота составляет 0,08%.
Практика показала, что этот уровень содержания азота слишком низок, если зона термического влияния и зона плавления должны поддерживать хорошие характеристики в условиях после сварки. Осознав эту проблему, ASTM использовал UNSS32205 для определения 2205 с 2000 года.
В таблице 1 показан диапазон составов UNS S31803 и UNS S32205. Стоит отметить, что по сравнению с S31803, помимо увеличения минимального содержания азота, также увеличилось минимальное содержание хрома и молибдена.
Составной стол из дуплексной нержавеющей стали 2205 | |||||||||
UNS | Диапазон химического состава / 1ТР1Т (максимум) | ||||||||
C | Mn | п | S | Si | Cr | Ni | Пн | N | |
S31803 | 0.030 | 2.000 | 0.030 | 0.020 | 1.000 | 21.0~23.0 | 4.5~6.5 | 2.5~3.5 | 0.08~0.20 |
S32205 | 0.030 | 2.000 | 0.030 | 0.020 | 1.000 | 22.0~23.0 | 4.5~6.5 | 3.0~3.5 | 0.14~0.20 |
Таблица 1
На рисунке 1 показана микроструктура кованой стали, которая соответствует составу UNS S31803, но не составу UNS S32205, а также распределение элементов сплава между фазой феррита и фазой аустенита. Для S32205 содержание азота 0,12% слишком низкое.
На рисунке 1 (а) феррит имеет более темно-серый цвет, а аустенит почти белый. Из рисунка видно, что ферритная фаза богата хромом и молибденом, а аустенитная фаза богата никелем и азотом.
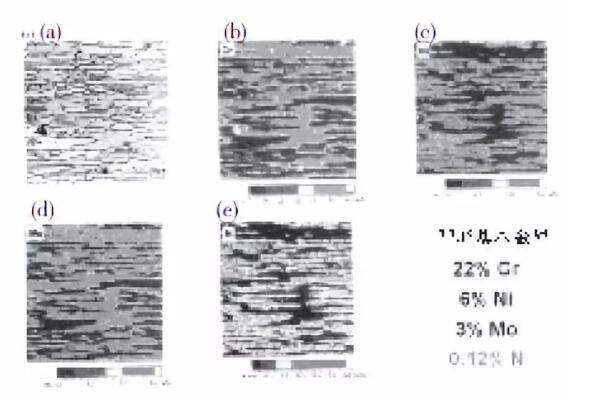
В частности, содержание хрома в феррите составляет около 25% и только 20% в аустените, как показано на рисунке 1 (b). Содержание молибдена в феррите составляет около 3,5%, в аустените. Содержание молибдена составляет всего 2,5%, как показано на рисунке 1 (d). Содержание никеля в аустените составляет 7,5%, а в феррите - около 5%. См. Рис. 1 (c), содержание азота в аустените составляет около 0,3%, а в феррите равно нулю, как показано на рис. 1 (e).
Распределение фаз в основном сбалансировано. Поскольку сталь представляет собой горячекатаный продукт, структура имеет ленточную форму.
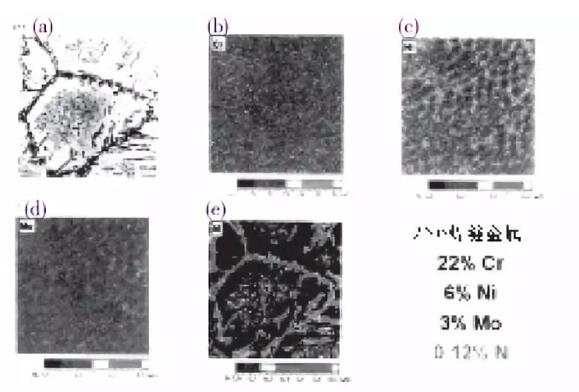
По сравнению с Фиг.1, Фиг.2 показывает микроструктуру и распределение легирующих элементов в зоне плавления самофлюсующегося GTA-сварного шва UNSS31803, который является таким же, как материал на Фиг. 1.
Трудно увидеть картину распределения элементов сплава на рис. 2 (б), 2 (в) или 2 (г) аналогично распределению фаз на рис. 2 (а). Однако распределение азота указывает на то, что концентрация азота в хлопьях аустенита вокруг границ зерен феррита выше, чем в зернах феррита. Это может быть связано с тем, что азоту в этих областях достаточно времени, чтобы диффундировать в аустенит на границах зерен феррита, в результате чего область рядом с аустенитной пластиной практически не содержит азота, как показано на рисунке 2 (е).
Внутри зерен феррита азот заблокирован, нет возможности попасть в аустенит, и он выпадает в осадок в виде нитрида хрома, что хорошо видно, как показано на рисунке 2 (а). Для зоны плавления сочетание крупных зерен феррита и выделений нитрида хрома очень пагубно сказывается на ударной вязкости и коррозионной стойкости зоны плавления.
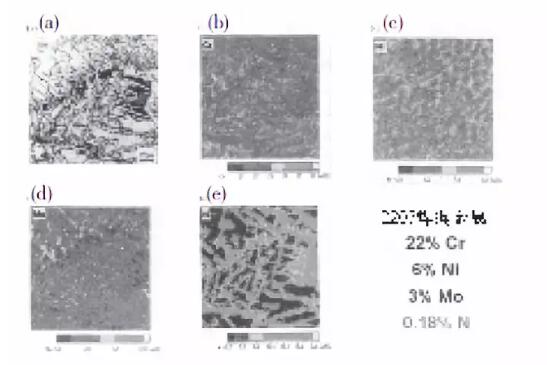
Фактически, как упоминалось ранее, 100% затвердевания в зоне плавления является ферритом. Затем, когда начинается превращение в аустенит, требуется диффузия.
Поскольку хром, никель и молибден являются заменяющими элементами, они относительно медленно диффундируют в твердом состоянии, поэтому они не могут достичь сбалансированного распределения между ферритом и аустенитом при нормальных условиях охлаждения при сварке. Азот - это промежуточный элемент, и его скорость диффузии примерно в 100 раз выше, чем у замещающего элемента. В результате он имеет большую способность вводить аустенит, хотя композиция вводится не полностью, как показано на фиг. 2.
В материалах, содержащих 0,12% азота, самая горячая часть ЗТВ ведет себя аналогично металлу сварного шва. В частности, он состоит из феррита 100% и затем частично превращается в аустенит в твердом состоянии. Следовательно, он более склонен к образованию крупных зерен феррита и чешуек аустенита, образованных вдоль границ исходных зерен феррита.
На рисунке 3 показана микроструктура и распределение легирующих элементов в зоне плавления GTA, когда содержание азота в сплаве 2205 выше, чем содержание азота, показанное на рисунке 2, и соответствует ограничениям по составу UNS S31803 и S32205.
Содержание азота в металле сварного шва на рис. 3 выше (содержание азота составляет 0,18% по сравнению с содержанием азота на рис. 2, равным 0,12%), что значительно изменяет микроструктуру после сварки. В частности, на рис. 3 (а) ясно видно, что образуется больше аустенита, чем аустенита, образованного на рис. 2 (а), и аустенит рассеивается по всем зернам феррита, а не ограничивается в основном железом. Граница зерен тела элемента. По сравнению с фиг. 2 (а), осаждение нитрида хрома на фиг. 3 (а). Вместо этого весь азот попадает в аустенит, как показано на Рисунке 3 (е). Более того, на рис. 3 (b) и (d) в этой области отчетливо видно небольшое распределение хрома и молибдена. Первичные зерна феррита.
Из-за более высокого содержания азота в этом образце образование аустенита может начаться при более высоких температурах, чем у сплавов 0,12% N, а поскольку диффузия и превращение начинаются при более высоких температурах, молибден и хром могут диффундировать быстрее, диффузия будет длиться дольше. На рис. 3 (а) также можно увидеть, что чешуйки аустенита, образовавшиеся на всех исходных зернах феррита, раздробили исходные крупные зерна феррита. Поскольку исходные зерна феррита разбиваются на мелкие зерна внутренними аустенитными полосками, прочность повышается. А поскольку нитрид хрома не осаждается, коррозионная стойкость улучшается. То же самое и в высокотемпературной части зоны термического влияния. Таким образом, можно сделать вывод, что UNSS32205 с более высоким содержанием азота на Рисунке 3 значительно лучше, чем UNS S31803 с более низким содержанием азота на Рисунке 2.
Предельный состав сплава 2550 | ||||||||||
UNS | Диапазон химического состава / 1ТР1Т (максимум) | |||||||||
C | Mn | п | S | Si | Cr | Ni | Пн | N | Cu | |
S32550 | 0.040 | 1.500 | 0.035 | 0.030 | 1.000 | 24.0~27.0 | 4.5~6.5 | 2.9~3.9 | 0.10~0.25 | 1.50~2.50 |
S32520 | 0.030 | 1.500 | 0.030 | 0.020 | 0.800 | 24.0~26.0 | 5.5~8.0 | 3.0~4.0 | 0.20~0.35 | 0.50~2.00 |
Таблица 2
Понятно, что UNS S31803 не подходит в качестве основного металла для использования после сварки, и следует использовать UNS S32205. Среди дуплексных нержавеющих сталей UNS S31803 - не единственный основной металл, непригодный для сварки конструкций. То же самое и со сплавом 255, входящим в состав UNS S32550. В таблице 2 сравнивается состав UNSS32550 и UNSS32520, используемых для наплавки. Состав в целом такой же. Однако минимальное содержание азота в UNS S32520 выше, чем в UNS S32550. Очевидно, что UNS S32520 больше подходит для применения после сварки. Кроме того, можно использовать UNSS32550, но содержание азота в составе стали необходимо контролировать до верхнего предела.
Неоправданный подвод тепла при сварке
Традиционный взгляд на подвод тепла при сварке заключается в том, что при сварке дуплексной нержавеющей стали с содержанием хрома 22% тепловложение должно быть ограничено до 0,5 ~ 2,5 кДж / мм, а при сварке супердуплексной нержавеющей стали с содержанием хрома 25% тепловложение должно быть ограничено 0,5 ~ 1,5 кДж / мм.
Когда используется меньшее тепловложение, даже для дуплексных сталей с высоким содержанием азота, аустенит охлаждается с очень высокой скоростью. Формирования тоже недостаточно. При использовании более высокого подводимого тепла (> 1,5 кДж) в условиях медленного охлаждения интерметаллические соединения склонны осаждаться в феррите. По сравнению с дуплексной нержавеющей сталью 22% Cr тенденция к использованию супердуплексной нержавеющей стали 25% Cr более очевидна.
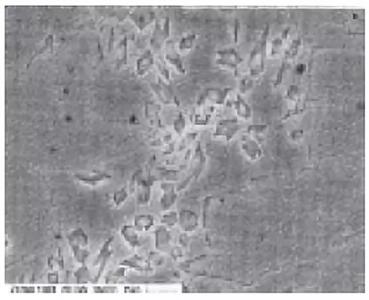
На рис. 4 показана микроструктура металла шва вблизи средней толщины образца. Только в феррите имеется большое количество угловых выделений. Однако точно не было установлено, что это за осадок. Наш вывод состоит в том, что осадки образовывались при повторном нагревании во время двенадцати проходов испытуемого образца.
Нормальная работа при сварке дуплексных нержавеющих сталей, особенно труб из супердуплексных нержавеющих сталей, заключается в том, что тепловложение у корневого валика больше, чем у исходного галтеля. Использование корневого валика толщиной около 6 мм вполне подходит.
Необоснованная термообработка после сварки
Если сварные отливки или сварные головки требуют термообработки после сварки, то использование обычно используемых присадочных металлов с высоким содержанием никеля в сочетании с использованием необоснованных температур отжига, соответствующих основным спецификациям металла, приведет к тому, что производители дуплексной обработки нержавеющей стали совершат еще одну ошибку. (для дуплексной нержавеющей стали содержание никеля обычно составляет 9%, остальные аналогичны присадочным металлам).
Общее требование - отжиг при минимальной температуре 1040 ° C, а затем закалка в воде от температуры отжига. Потому что люди не знают, что σ-фаза почти всегда образуется в дуплексной нержавеющей стали во время нагрева до температуры отжига, и чем выше содержание никеля, тем выше температура фазы твердого раствора σ-фазы. В этом случае металл шва, богатый никелем, опасен.
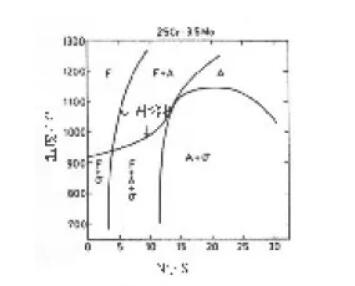
На рисунке 5, сделанном Гробнером, показано влияние никеля на температуру фазы твердого раствора σ-фазы сплава 25% Cr-3.5% Mo.
Хотя сплав, использованный для построения этой диаграммы, не содержит легирующих элементов, таких как марганец, кремний и азот, людям удобно понимать влияние никеля в природе. Это ясно показывает, что температура фазы твердого раствора σ-фазы увеличивается с увеличением содержания никеля. В частности, температура линии фазы твердого раствора σ-фазы металла сварного шва, содержащего 9% Ni, будет по крайней мере на 50 ° C выше, чем температура линии фазы твердого раствора σ-фазы соответствующего основного металла, содержащего 5% Ni.
Заключение
Практика доказала, что дуплексная нержавеющая сталь, в том числе супердуплексная нержавеющая сталь, обладает хорошими сварочными характеристиками и является очень важным конструкционным материалом.
Однако из-за невнимательности и незнания могут быть допущены некоторые ошибки. Чтобы зона термического влияния и металл сварного шва имели хорошие характеристики, целесообразно использовать основной металл с высоким содержанием азота, по крайней мере, 0,14% азота. В противном случае в зоне термического влияния будет осаждаться большое количество феррита и нитрида хрома, что повредит коррозионную стойкость и механические свойства.
Чтобы избежать осаждения супердуплексной нержавеющей стали в зоне многократного нагрева, следует избегать использования большого количества малой погонной энергии и небольшого валика. А при сварке труб из дуплексной нержавеющей стали и супердуплексной нержавеющей стали, чтобы предотвратить осадки на внутренней поверхности трубы, корневой валик должен использовать более высокое тепловложение (более 1 кДж / мм), что превышает тепловложение первые несколько непрерывных швов.
При послесварочном отжиге сварной дуплексной нержавеющей стали необходимо учитывать тот факт, что температура σ-фазы металла сварного шва, которая растворяет богатый никелем металл шва, выше, чем температура основного металла.