UNS N04400, also called monel 400,MCu-28-1.5-1.8 or Ni68Cu28Fe.
It is a nickel-based alloy material with good corrosion resistance in seawater, chemical solvents and various acidic media.
Especially in hydrofluoric acid corrosion resistance, ranked first in the general nickel-based alloys.
The main components of Monel 400 are NICKEL e COPPER.
Welding Precautions for N04400
Monel 400 has good welding performance, can be TIG and MIG method, can use Monel body or EniCu-7 wire, electrode. Or manual electric arc welding and submerged arc welding, can be welded with carbon steel and low alloy steel. We remind you of the following two points.
Easy to produce thermal cracks, especially in the arc pit crack sensitivity is greater. Mainly in the arc pit S, P segregation, S, P and Ni form a low melting point co-crystal. In the weld crystallization process, the segregation in the crystal boundary, under the action of tensile stress to produce cracks. So S, P content must be strictly controlled.
Liquid metal has poor fluidity and can dissolve gases such as oxygen, nitrogen and hydrogen, making it prone to porosity.
N04400 Welding Description
In order to test its welding performance and process, we cite a customer example to do welding test guide.
Test Plate Specifications
Two 10*300*100 test plate, welding bevel angle 37.5°, blunt edge 4mm, using a planer processing. The origin of the test plate is VDM, Germany.
Test Welding Process
The test welding process consists of first beveling, then assembling the test plate and spot welding it, with the addition of the lead-in and take-out plate 304.
Next, pre-weld cleaning is performed to prepare for welding.
Welding is automated, using the PAW process for priming, followed by three passes of TIG filler wire and cover welding.
After the welding was completed, RT inspection was carried out and mechanical tests were performed.
Due to the limited size of the test plate, the mechanical test was only able to complete the tensile test and the forward and reverse bending test of the weld.
Welding Situation
The operator should operate in a standardized manner and control the welding parameters properly. At this time, the welded plate has good welding quality and meets the performance requirements of N04400 alloy.
Use small heat input to reduce the probability of cracking. Low welding specifications (current, voltage, welding speed) to reduce the risk of deformation and welding defects. Control the interlayer temperature less than 100℃ to reduce the influence of heat cycle in the welding process.
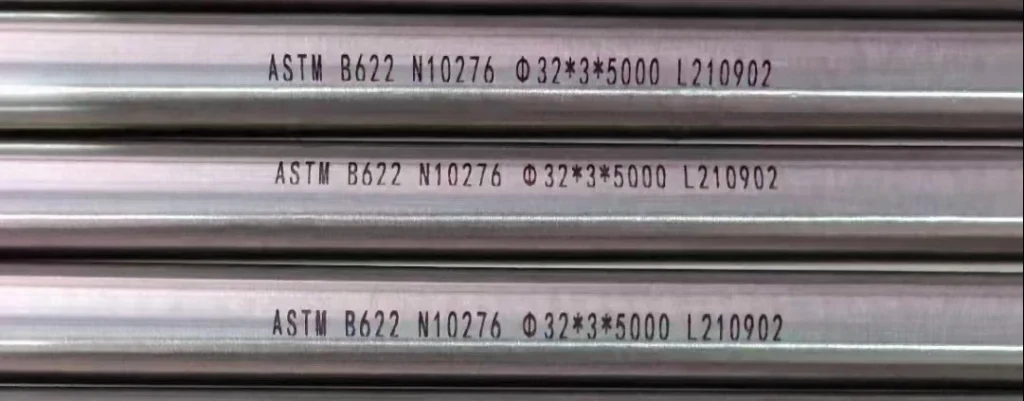
N04400 Welding Process
Designation | Diameter (mm) | C | Mn | Si | S | P | Al | Fe | Ti | Cu | Ni+Co | Ni |
---|---|---|---|---|---|---|---|---|---|---|---|---|
Welding Wire | 1.6 | 0.072 | 3.53 | 0.97 | 0.001 | 0.005 | 0.12 | 0.12 | 2.35 | Remainder | 65.11 | / |
Welding Rod | 3.2 | 0.10 | 3.38 | 0.84 | 0.003 | 0.005 | 0.22 | 0.45/td> | 0.74 | 29.52 | / | 64.74 |
Ⅱ, Welding rod 350℃×1h drying; wire pay attention to surface cleaning.Normally no preheating in necessary. Preheat to below 100°C if required.
Ⅲ, Arc welding polarity for DC reverse connection, TIG for DC positive connection, tungsten diameter positive connection, tungsten diameter φ3mm, nozzle diameter φ10mm, argon purity 99.99%.
Ⅳ, Mechanical grinding and scrub the bevel and its edge with acetone.
V, Bevel Form & Welding Sequence
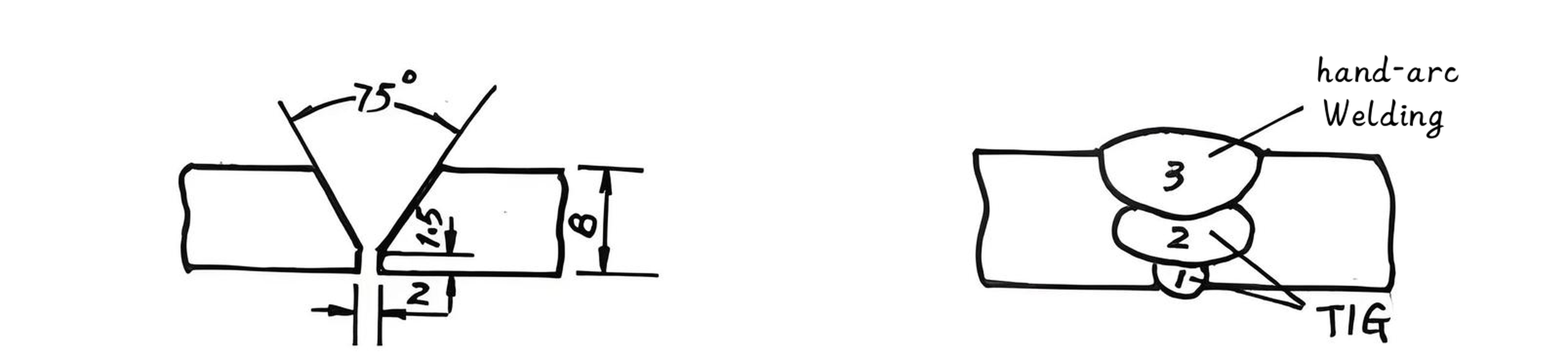
Welding Method | Welding Levels | Welding current (A) | Arc Voltage (V) | Welding Speed (cm/min) | 12 | Argon Flow Rate (L/min) | Interlayer Temperature ( °C) |
---|---|---|---|---|---|---|---|
TIG | Underlayer | 70 ~ 120 | 14 ~ 18 | 10 | 10080 | 8 ~ 12 | / |
TIG | Second | 95 ~ 120 | 14 ~ 18 | 6 | 15400 | 8 ~ 12 | Less Than 100 |
Hand-arc Welding | Cover Layer | 110 ~ 120 | 22 ~ 24 | 7 | 20740 | / | Less Than 100 |
VIII, The filler wire should be kept at a suitable angle for fast feeding.
Ⅸ, Control the depth of fusion during the application and keep the fusion ratio below 50%. Also use a low current.
Ⅹ, Narrow and flat weld paths are best. Elevated face welding parts should minimize the volume of the molten pool, in order to facilitate weld shaping. When closing the arc, pay attention to fill the arc pit.
Ⅺ, Use short-arc welding to avoid excessive intake of harmful gases during the welding process.