Nickel-based Alloys are a class of alloys that have high strength and a certain degree of resistance to oxidation and corrosion at high temperatures of 650-1000℃.
Classification | Main Types |
---|---|
By Main Performance(Nickel-based) | Heat-resistant Alloy |
Corrosion-resistant Alloy | |
Wear-resistant Alloy | |
Precision Alloy | |
Shape Memory Alloy | |
By Matrix Material | Iron Based Superalloy |
Nickel Based Superalloy | |
Cobalt Based Superalloy |
Role of major elements of Nickel-Based Alloys
When it comes to nickel based alloys, you have to talk about the element nickel first.
Like iron and copper, nickel has been used in alloys since the dawn of civilization. But compared to steel, brass and bronze, nickel alloys were a latecomer to the chemical industry. Continuous advances in metallurgy and manufacturing technology have driven the development of nickel alloys and facilitated their widespread use in the chemical industry. Nickel alloys combine excellent corrosion resistance, strength, toughness, metallurgical stability, workability and weldability. Many nickel alloys also have excellent heat resistance, making them ideal for applications requiring high-temperature strength and chemical resistance at elevated temperatures.
The primary role of nickel in nickel-based alloys is that it alters the crystal structure of the material. An important value of nickel in nickel-based alloys is the formation of an austenitic crystal structure, which improves such things as malleability, weldability and toughness.
The roles of various elements other than nickel in nickel-based alloys are as follows.
Lowering the melting point of the alloy, expanding the temperature zone of the solid-liquid phase line, and forming low-melting eutectic crystals. Deoxidizing and reducing effect and slagging function. Hardening and strengthening of the coating. Improvement of operation process performance.
Improve the corrosion resistance to non-oxidizing acids.
Solid solution strengthening effect, passivation effect. Improve the corrosion resistance and high temperature oxidation resistance. Formation of chromium carbide, chromium boride hard phase to improve alloy hardness and wear resistance.
Solid solution causes large distortions in the lattice, significantly strengthening the alloy matrix. Improve the high temperature strength and red hardness of the matrix. Can cut off and reduce the reticulation organization in the coating. Improve the resistance to cavitation and erosion Nickel-based precision alloys.
Nickel Alloy Representative
The first nickel alloy of commercial importance was Alloy 400. It was developed and marketed in 1905 by the International Nickel Company (Inco Alloys) under the trademark MONEL.
The next important milestones were the nickel-molybdenum alloy B and the nickel-chromium-molybdenum-tungsten alloy C, which were introduced around 1930. Their inventor was the Haynes Stellite Company (Haynes International). Two of them are registered under the trademark HASTELLOY.
The next important stage in the development of nickel-based alloys came from Inco. The development of nickel-chromium-iron alloy 600 in 1931 and nickel-iron-chromium alloy in 1949 were named INCONEL and INCOLOY, respectively.
Inco and Haynes capitalized on the popularity and reputation of these initial trademarks to introduce a total of about 50 corrosion and heat resistant alloys.VDM was a later and better known developer and producer of nickel-based alloys under the trademarks Nicrofer, Nimofer and Nicorros.
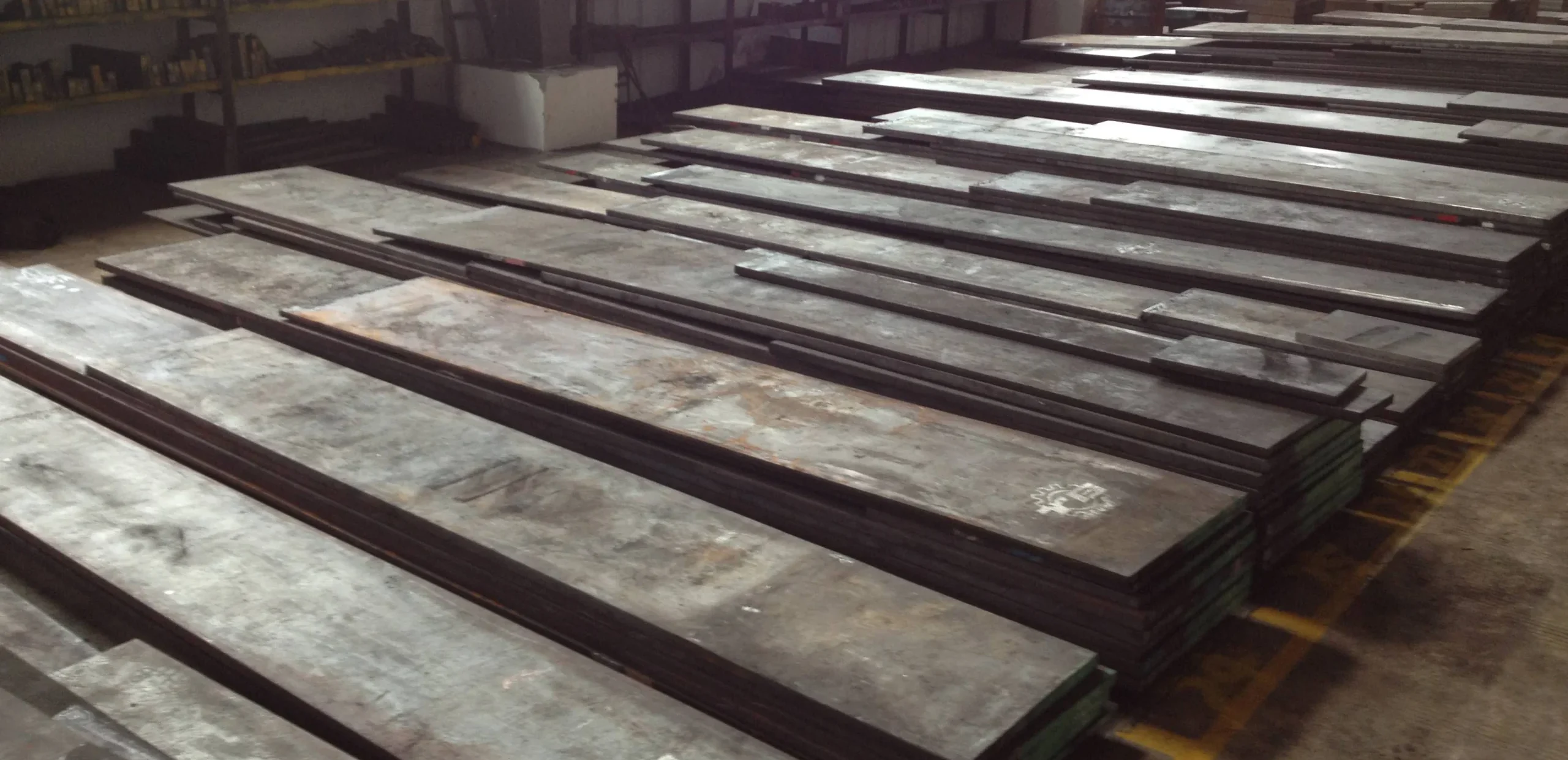
History
Nickel-based alloys were developed in the late 1930’s. Nimonic 75 (Ni-20Cr-0.4Ti) was first produced in the UK in 1941, and Nimonic 80 (Ni-20Cr-2.5Ti-1.3Al) was developed to improve creep strength and add aluminum. Nickel-based alloys were also developed in the USA in the mid-1940s, in the USSR in the late 1940s, and in China in the mid-1950s.
Its development included improvements in alloy composition and innovations in production processes.
In the early 1950s, the development of vacuum melting technology created the conditions for refining nickel-based alloys containing high levels of aluminum and titanium.
At the end of the 1950s, the higher operating temperatures of turbine blades requiring alloys with higher high-temperature strength. However, the high strength of the alloy makes it difficult, if not impossible, to deform. So using the investment casting process to develop a series of casting alloys with good high-temperature strength.
The mid-1960s, the development of a series of casting alloys with good high-temperature strength.
In the mid-1960s, single-crystal high-temperature alloys and powder metallurgy high-temperature alloys with good performance were developed. To meet the needs of ships and industrial gas turbines, since the 1960s has also developed a number of heat resistance, corrosion resistance, good organizational stability of high chromium-nickel-based alloys.
From the early 1940s to the end of the 1970s about 40 years, nickel-based alloy working temperature from 700 ℃ to 1100 ℃, an average annual increase of about 10 ℃.
Nickel Alloys Product
Composition And Properties
Nickel-based high temperature alloys are the most widely used. The main reasons are: first, can dissolve more alloying elements, and can maintain good organizational stability. Secondly, the co-lattice-ordered A3B-type intermetallic compound γ[Ni3(Al, Ti)] phase forms as the reinforcing phase and strengthens the alloy. Finally, higher high-temperature strengths than those of iron-based high-temperature alloys and cobalt-based high-temperature alloys can also result. Third, compared with iron-based high-temperature alloys, chromium-containing nickel-based alloys have better resistance to oxidation and gas corrosion.
It contains more than a dozen elements, of which chromium mainly plays the role of antioxidant and corrosion resistance. There are solid solution strengthening elements, precipitation strengthening elements and grain boundary strengthening elements according to their strengthening effects.
According to the strengthening method, there are solid solution strengthening alloys and precipitation strengthening alloys.
Production Process
Smelting in order to obtain more purified steel, reduce the gas content and harmful element content, at the same time, due to some alloys in the oxidizable elements such as Al, Ti, etc., the existence of non-vacuum smelting is difficult to control; but also in order to obtain better thermoplasticity, nickel-based heat-resistant alloys, usually using a vacuum induction furnace smelting. Even with vacuum induction smelting plus vacuum self-consumption furnace or electroslag furnace remelting mode for production.
Deformation of forging, rolling process, for poor thermoplasticity of the alloy and even the use of extrusion of open billet after rolling or soft steel (or stainless steel) jacket direct extrusion process. The purpose of deformation is to break the casting organization, optimize the microstructure.
Casting is usually done by melting the master alloy in a vacuum induction furnace to ensure composition and control gas and impurity content. And the parts are made by vacuum remelting-precision casting.
In the case of Udmet 500 alloy, for example, there are four stages in the heat treatment system. Solution treatment, 1175°C, 2 hours, air cooling. Intermediate treatment, 1080°C, 4 hours, air cooling. Primary aging treatment, 843°C, 24 hours, air cooling. Secondary aging treatment, 760°C, 16 hours, air cooling.In order to obtain the required state of organization and good overall performance.
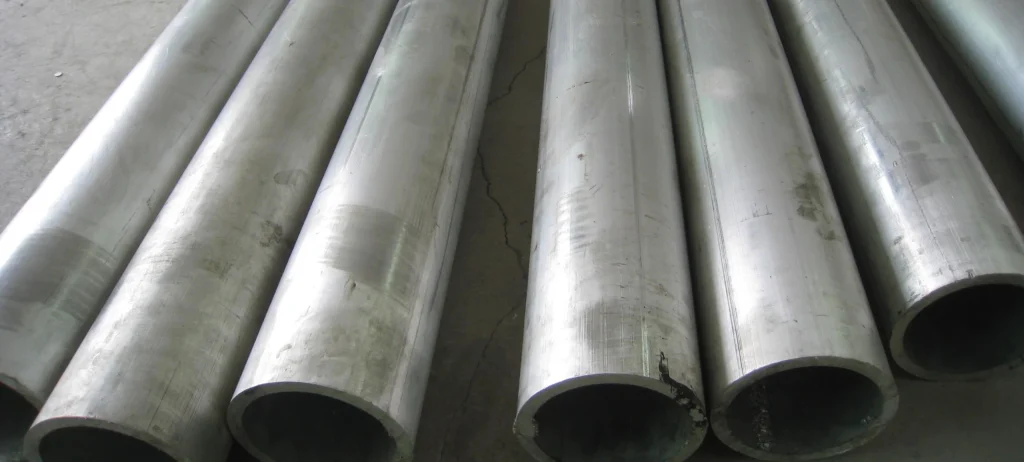
Nickel-based Corrosion Resistant Alloys
The main alloying elements are copper, chromium and molybdenum. It has good comprehensive performance and can resist various acid corrosion and stress corrosion. The earliest applications were nickel-copper alloys, also known as monel alloys. There are also nickel-chromium alloys, nickel-molybdenum alloys, nickel-chromium-molybdenum alloys At the same time, pure nickel is also a typical representative of nickel-based corrosion-resistant alloys. Nickel-based corrosion-resistant alloys are indispensable for the manufacture of petroleum, chemical, electric power and other corrosion-resistant environmental parts.
Category
Ni-Cu alloy has better corrosion resistance than nickel in reducing media and better corrosion resistance than copper in oxidizing media. It is the best material to resist high temperature fluorine gas, hydrogen fluoride and hydrofluoric acid under the condition of no oxygen and oxidizer.
Ni-Cr alloy Also known as nickel-based heat-resistant alloy, it is mainly used in oxidizing medium conditions. Resistant to high-temperature oxidation and corrosion of gases containing sulfur and vanadium, their corrosion resistance increases with chromium content. These alloys also have good resistance to hydroxide (such as NaOH, KOH) corrosion and stress corrosion resistance.
Nickel-molybdenum alloys are mainly used under corrosive conditions in reducing media. It is one of the alloys with the best corrosion resistance to hydrochloric acid. However, in the presence of oxygen and oxidizing agents, its corrosion resistance is greatly reduce.
Ni-Cr-Mo (W) alloy both the above Ni-Cr alloy, Ni-Mo alloy performance. Mainly used in oxidizing – reducing mixed media conditions. This type of alloy in the high temperature hydrogen fluoride gas, in the oxygen and oxidizing agent containing hydrochloric acid, hydrofluoric acid solution, as well as at room temperature in the wet chlorine gas corrosion resistance is good.
Ni-Cr-Mo-Cu alloys are resistant to both nitric and sulfuric acid corrosion and have good corrosion resistance in some redox mixed acids.
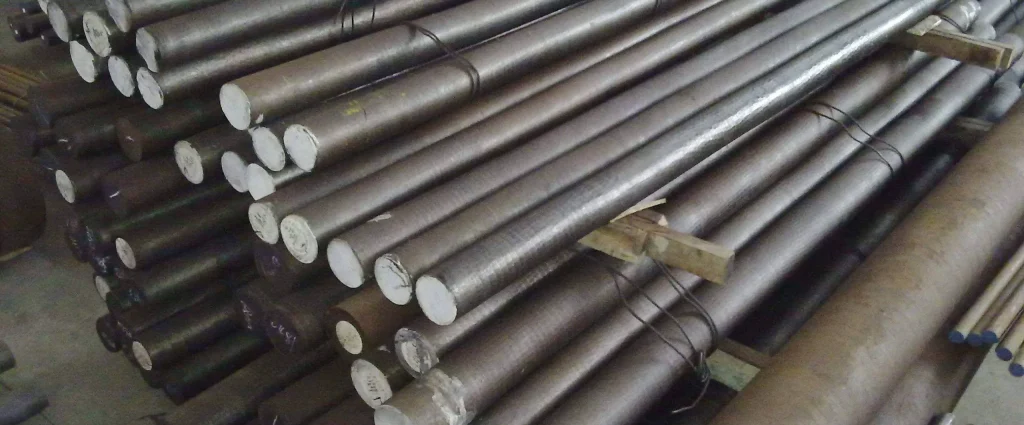
Nickel-based Wear-resistant Alloys
The main alloying elements are chromium, molybdenum, tungsten, and also contains a small amount of niobium, tantalum and indium. In addition to wear-resistant performance, its oxidation resistance, corrosion resistance, welding performance is also good. It can make wear-resistant parts. It is also a cladding material, which acts as an overlay on other substrate surfaces through the cladding and spraying process.
There are mainly self-melting alloy powders and non-self-melting alloy powders.
Non-self-fusing nickel-based powder refers to nickel-based alloy powder without B, Si or with lower B, Si content. This type of powder, widely used in plasma arc spray coating, flame spray coating and plasma surface strengthening. They mainly include: Ni-Cr alloy powder, Ni-Cr-Mo alloy powder, Ni-Cr-Fe alloy powder, Ni-Cu alloy powder, Ni-P and Ni-Cr-P alloy powder, Ni-Cr-Mo-Fe alloy powder, Ni-Cr-Mo-Si alloy powder with high abrasion-resistance, Ni-Cr-Fe-Al alloy powder, Ni-Cr-Fe-Al-B-Si alloy powder, Ni-Cr-Si alloy powder, Ni-Cr-W-based wear and corrosion-resistant alloy powder, and so on.
The addition of appropriate amounts of B and Si to nickel alloy powders results in the formation of self-fusing alloy powders. The so-called self-fusing alloy powder, also known as low eutectic alloys and hardfacing alloys, is in nickel, cobalt and iron-based alloys by adding low melting point eutectic alloying elements (mainly boron, silicon) to form a series of powder materials. Commonly used are Ni-B-Si alloy powder, Ni-Cr-B-Si alloy powder, Ni-Cr-B-Si-Mo, Ni-Cr-B-Si-Mo-Cu, Ni-Cr-W-C based self-melting alloy powder, high copper self-melting alloy powder and more.
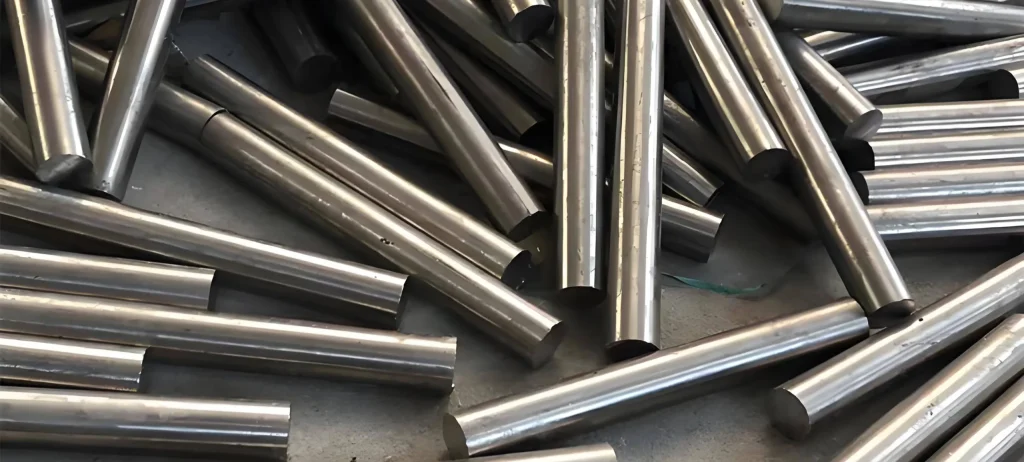
Nickel-based Precision Alloys
These include soft magnetic alloys, precision resistance alloys and electrothermal alloys. The most commonly used soft magnetic alloys are Bomol alloys containing about 80% nickel, which have high maximum permeability and starting permeability and low coercivity, and are important core materials for the electronics industry. The main alloying elements of precision resistance alloys are chromium, aluminum and copper. This alloy has high resistivity, low resistance temperature coefficient and good corrosion resistance. It applies to the manufacture of resistors. Electrothermal alloy is a nickel alloy containing 20% chromium, has good oxidation resistance and corrosion resistance, can make long-term use under the temperature of 1000 ~ 1100 ℃.
Nickel-based Shape Memory Alloys
It contains 50% titanium. Its recovery temperature is 70°C with good shape memory effect. A small change in the proportion of nickel and titanium components can make the recovery temperature in the range of 30 to 100 ℃. Mostly used in the manufacture of spacecraft used in the automatic opening of structural components, the aerospace industry, self-excited fasteners, biomedical use of artificial heart motors and so on.