Experimentos e resultados da soldagem duplex de tubos de aço inoxidável
O homem produziu e utilizou aço inoxidável duplex por quase 80 anos. As primeiras ligas, como a liga maleável 329 e a liga fundida CD4MCu, continham muito mais ferrita do que austenita.
As pessoas não prestam atenção à importância do nitrogênio. Muitas ligas contêm muito pouco nitrogênio, de modo que, quando o tratamento térmico não é realizado após a soldagem, a zona afetada pelo calor dessas ligas geralmente se torna frágil e tem baixa resistência à corrosão. O metal de solda de soldagem a gás também apresenta esse defeito.
Na década de 1980, a importância do nitrogênio para tubos de aço inoxidável duplex foi totalmente reconhecido, e os requisitos de conteúdo mínimo de nitrogênio foram geralmente especificados. Ao adicionar um teor de nitrogênio adequado ao metal de base e usar um metal de adição de solda com um teor de níquel aumentado, a soldagem pode ter quantidades aproximadamente iguais de austenita e ferrita no estado soldado, o que melhora significativamente as propriedades mecânicas Resistência à corrosão melhorada.
Erros
Especificações de metal base irracionais
Durante os últimos 25 anos, o aço inoxidável duplex mais comum é uma liga chamada 2205. Quase toda a literatura utiliza a faixa de composição do UNSS31803 para descrever esta liga. Entretanto, o UNSS S31803 tem um teor mínimo de nitrogênio de 0,08%.
A prática provou que este nível de conteúdo de nitrogênio é muito baixo, se a zona afetada pelo calor e a zona de fusão devem manter um bom desempenho sob condições pós-soldagem. Depois de perceber esse problema, a ASTM usou UNSS32205 para definir 2205 desde 2000.
A Tabela 1 mostra a faixa de composição de UNS S31803 e UNS S32205. Vale ressaltar que, em comparação com S31803, além de aumentar o teor mínimo de nitrogênio, o teor mínimo de cromo e molibdênio também aumentou.
Mesa de composição de aço inoxidável 2205 duplex | |||||||||
UNS | Faixa de composição química / % (máximo) | ||||||||
C | Mn | P | S | Si | Cr | Ni | Mo | N | |
S31803 | 0.030 | 2.000 | 0.030 | 0.020 | 1.000 | 21.0~23.0 | 4.5~6.5 | 2.5~3.5 | 0.08~0.20 |
S32205 | 0.030 | 2.000 | 0.030 | 0.020 | 1.000 | 22.0~23.0 | 4.5~6.5 | 3.0~3.5 | 0.14~0.20 |
tabela 1
A Figura 1 mostra a microestrutura do aço forjado que está em conformidade com a composição do UNS S31803, mas não com a composição do UNS S32205, e a distribuição dos elementos de liga entre a fase de ferrita e a fase de austenita. Para S32205, o conteúdo de nitrogênio de 0,12% é muito baixo.
Na Figura 1 (a), a ferrita é cinza mais escuro, enquanto a austenita é quase branca. Pode-se observar na figura que a fase ferrita é rica em cromo e molibdênio e a fase austenita é rica em níquel e nitrogênio.
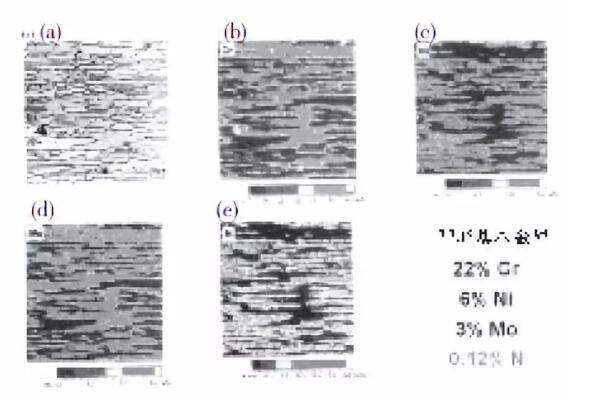
Em particular, o conteúdo de cromo na ferrita é de cerca de 25% e apenas 20% na austenita, conforme mostrado na Figura 1 (b). O teor de molibdênio na ferrita é de cerca de 3,5%, na austenita O teor de molibdênio é de apenas 2,5%, conforme mostrado na Figura 1 (d). O conteúdo de níquel na austenita é 7,5% e é cerca de 5% na ferrita. Veja a Figura 1 (c), o conteúdo de nitrogênio na austenita é cerca de 0,3%, e é zero na ferrita, conforme mostrado na Figura 1 (e).
A distribuição das fases é basicamente equilibrada. Como o aço é um produto laminado a quente, a estrutura é em forma de faixa.
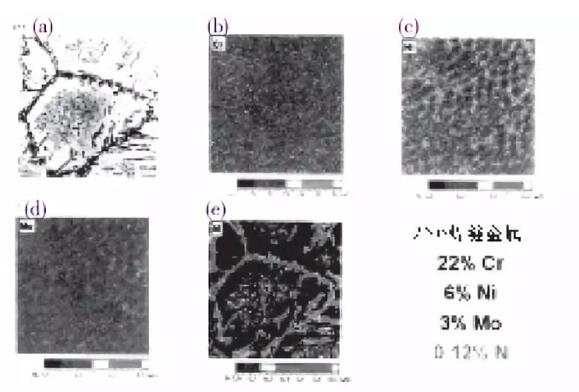
Em comparação com a Figura 1, a Figura 2 mostra a microestrutura e a distribuição do elemento de liga da zona de fusão da solda GTA autofluxante de UNSS31803, que é a mesma que o material na FIG. 1
É difícil ver o padrão de distribuição dos elementos de liga nas Figs. 2 (b), 2 (c) ou 2 (d) semelhante à distribuição de fase da Fig. 2 (a). No entanto, a distribuição de nitrogênio indica que a concentração de nitrogênio nos flocos de austenita em torno dos limites do grão de ferrita é maior do que nos grãos de ferrita. Isso pode ser devido ao tempo suficiente para o nitrogênio nessas regiões se difundir na austenita nos contornos de grão da ferrita, resultando na região próxima à placa de austenita contendo praticamente nenhum nitrogênio, conforme mostrado na Figura 2 (e).
Dentro dos grãos de ferrita, o nitrogênio é bloqueado, não há chance de entrar na austenita, e ele precipita como nitreto de cromo, que é claramente visível, conforme mostrado na Figura 2 (a). Para a zona de fusão, a combinação de grandes grãos de ferrite e precipitados de nitreto de cromo é muito prejudicial para a tenacidade e resistência à corrosão da zona de fusão.
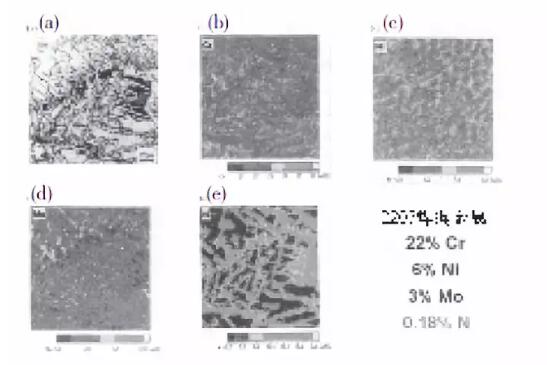
Na verdade, como mencionado anteriormente, 100% da solidificação na zona de fusão é ferrita. Então, quando a transformação em austenita começa, a difusão é necessária.
Como o cromo, o níquel e o molibdênio são elementos de substituição, eles se difundem de forma relativamente lenta no estado sólido, de modo que não podem atingir uma distribuição equilibrada entre ferrita e austenita em condições normais de resfriamento de soldagem. O nitrogênio é um elemento intersticial e sua taxa de difusão é cerca de 100 vezes mais rápida do que a do elemento substituto. Como resultado, ele tem mais capacidade de entrar na austenita, embora a composição não seja completamente inserida como mostrado na FIG. 2
Em materiais contendo nitrogênio 0,12%, a parte mais quente da HAZ se comporta de forma semelhante ao metal de solda. Em particular, é composto por ferrita 100% e, em seguida, se transforma parcialmente em austenita no estado sólido. Portanto, é mais inclinado a formar grandes grãos de ferrita e flocos de austenita formados ao longo dos limites originais dos grãos de ferrita.
A Figura 3 mostra a microestrutura e a distribuição do elemento de liga na zona de fusão GTA quando o teor de nitrogênio da liga 2205 é maior do que o teor de nitrogênio mostrado na Figura 2 e atende aos limites de composição de UNS S31803 e S32205.
O teor de nitrogênio do metal de solda na Fig. 3 é maior (o teor de nitrogênio é 0,18%, em comparação com o teor de nitrogênio da Fig. 2 sendo 0,12%), o que muda significativamente a microestrutura após a soldagem. Em particular, pode ser visto claramente na Fig. 3 (a) que mais austenita é formada do que austenita formada na Fig. 2 (a), e a austenita é dispersa através de todos os grãos de ferrita em vez de ser principalmente limitada ao ferro. Limite de grão do corpo do elemento. Em comparação com a FIG. 2 (a), a precipitação de nitreto de cromo não é vista na FIG. 3 (a). Em vez disso, todo o nitrogênio entra na austenita, conforme mostrado na Figura 3 (e). Além disso, nas Figuras 3 (b) e (d), uma pequena distribuição de cromo e molibdênio pode ser vista claramente nesta região. Grãos primários de ferrite.
Devido ao maior teor de nitrogênio desta amostra, a formação de austenita pode começar em temperaturas mais altas do que ligas de 0,12% N e, como a difusão e a transformação começam em temperaturas mais altas, o molibdênio e o cromo podem se difundir mais rapidamente, a difusão demorará mais. Também pode ser visto na Fig. 3 (a) que os flocos de austenita formados em todos os grãos de ferrita originais estilhaçaram os grãos de ferrita grosseiros originais. Como os grãos de ferrita originais são quebrados em pequenos grãos pelas tiras de austenita internas, a tenacidade é melhorada. E como nenhum nitreto de cromo é precipitado, a resistência à corrosão é melhorada. O mesmo é verdade na parte de alta temperatura da zona afetada pelo calor. Desta forma, pode-se concluir que UNSS32205 com maior teor de nitrogênio na Figura 3 é significativamente melhor do que UNS S31803 com menor teor de nitrogênio na Figura 2.
A composição limite da liga 2550 | ||||||||||
UNS | Faixa de composição química / % (máximo) | |||||||||
C | Mn | P | S | Si | Cr | Ni | Mo | N | Cu | |
S32550 | 0.040 | 1.500 | 0.035 | 0.030 | 1.000 | 24.0~27.0 | 4.5~6.5 | 2.9~3.9 | 0.10~0.25 | 1.50~2.50 |
S32520 | 0.030 | 1.500 | 0.030 | 0.020 | 0.800 | 24.0~26.0 | 5.5~8.0 | 3.0~4.0 | 0.20~0.35 | 0.50~2.00 |
mesa 2
É claro que UNS S31803 não é adequado como um metal base para uso no estado pós-soldagem, e UNS S32205 deve ser usado. Entre os aços inoxidáveis duplex, UNS S31803 não é o único metal base inadequado para estruturas de soldagem. O mesmo é verdadeiro para a liga 255, que é um componente do UNS S32550. A Tabela 2 compara a composição de UNSS32550 e UNSS32520 usada para revestimento. A composição é geralmente a mesma. No entanto, o conteúdo mínimo de nitrogênio do UNS S32520 é maior do que o do UNS S32550. Obviamente, UNS S32520 é mais adequado para aplicações pós-soldagem. Além disso, UNSS32550 também pode ser usado, mas o teor de nitrogênio da composição do aço deve ser controlado até o limite superior.
Entrada de calor de soldagem irracional
A visão tradicional da entrada de calor de soldagem é que ao soldar aço inoxidável duplex com teor de cromo 22%, a entrada de calor deve ser limitada a 0,5 ~ 2,5kJ / mm, e ao soldar aço inoxidável super duplex com teor de cromo 25%, a entrada de calor deve ser limitado a 0,5 ~ 1,5kJ / mm.
Quando uma entrada de calor mais baixa é usada, mesmo para aços duplex com alto teor de nitrogênio, a austenita é resfriada a uma taxa muito rápida. A formação também é insuficiente. Quando uma entrada de calor mais alta (> 1,5kJ) é usada, sob condições de resfriamento lento, há uma tendência de compostos intermetálicos precipitarem na ferrita. Comparado com o aço inoxidável duplex 22% Cr, a tendência do aço inoxidável super duplex 25% Cr é mais óbvia.
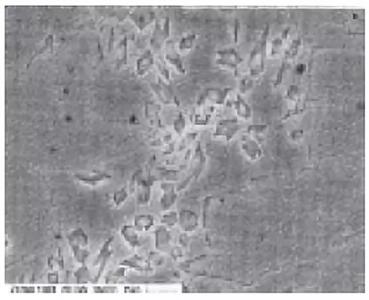
A Figura 4 mostra a microestrutura do metal de solda próximo à espessura média da amostra. Há um grande número de precipitados angulares apenas na ferrita. No entanto, não foi determinado exatamente o que era o precipitado. Nossa conclusão é que os precipitados foram gerados por aquecimento repetido durante doze passagens do corpo de prova.
A operação normal ao soldar aços inoxidáveis duplex, especialmente tubos de aço inoxidável super duplex, é que a entrada de calor no cordão de raiz seja maior do que o filete original. O uso de conta de raiz com espessura de cerca de 6 mm é bastante bom.
Tratamento térmico pós-soldagem irracional
Se fundições soldadas ou cabeças soldadas requerem tratamento térmico pós-soldagem, então o uso de metais de adição ricos em níquel comumente usados, juntamente com o uso de temperaturas de recozimento excessivas que atendem às especificações básicas de metal, fará com que os fabricantes de processamento de aço inoxidável duplex cometam Outro erro (para aço inoxidável duplex, o conteúdo de níquel é geralmente 9%, outros são semelhantes aos metais de adição).
O requisito geral é recozer a uma temperatura mínima de 1040 ° C e, em seguida, extinguir com água a partir da temperatura de recozimento. Porque as pessoas não sabem que a fase σ é quase sempre formada no aço inoxidável duplex durante o aquecimento até a temperatura de recozimento, e quanto maior o teor de níquel, aumentará a temperatura da fase de solução sólida da fase σ. Nesse caso, o metal de solda rico em níquel é perigoso.
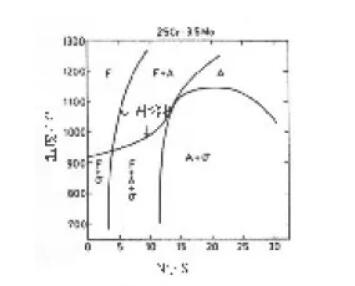
A Figura 5 feita por Grobner mostra o efeito do níquel na temperatura da fase de solução sólida da fase σ da liga 25% Cr-3.5% Mo.
Embora a liga usada para desenhar este diagrama não contenha elementos de liga como manganês, silício e nitrogênio, é conveniente que as pessoas entendam o efeito do níquel na natureza. Isso mostra claramente que a temperatura da fase de solução sólida da fase σ aumenta com o aumento do conteúdo de níquel. Em particular, a temperatura da linha de fase de solução sólida da fase σ do metal de solda contendo 9% Ni será pelo menos 50 ° C mais alta do que a temperatura da linha de fase de solução sólida da fase σ do metal de base correspondente contendo Ni 5%.
Conclusão
A prática provou que o aço inoxidável duplex, incluindo o aço inoxidável super duplex, tem bom desempenho de soldagem e é um material de engenharia muito importante.
No entanto, devido ao descuido e ignorância, alguns erros podem ser cometidos. Para fazer com que a zona afetada pelo calor e o metal de solda tenham um bom desempenho, é apropriado usar um metal de base com um alto teor de nitrogênio de pelo menos 0,14% de nitrogênio. Caso contrário, uma grande quantidade de ferrita e nitreto de cromo será precipitada na zona afetada pelo calor, o que danificará a resistência à corrosão e as propriedades mecânicas.
A fim de evitar a precipitação de aço inoxidável super duplex na área de aquecimento repetido, o uso de uma grande quantidade de entrada de calor baixa e pequeno cordão deve ser evitado. E ao soldar tubos de aço inoxidável duplex e aço inoxidável super duplex, para evitar precipitação na superfície interna do tubo, o cordão da raiz deve usar uma entrada de calor mais alta (maior que 1kJ / mm), que é maior que a entrada de calor do primeiras soldas contínuas.
O recozimento pós-soldagem do aço inoxidável duplex soldado precisa levar em consideração o fato de que a temperatura da fase σ do metal de solda que dissolve o metal de solda rico em níquel é mais alta do que a do metal de base.