A flange gasket is an important part that seals the space between two sections of pipe.So, these gaskets are vital in pipelines carrying water, liquids, or gases, for a safe, leak-proof connection. Unlike other surfaces, flange surfaces flare out and can easily cause fluid leaks if not sealed properly. Flange gaskets are specifically designed for these flanged surfaces to provide a tight seal and prevent leaks. In this article, we will discuss the types and importance of flange gaskets in detail.
What Is A Flange Gasket?
The flange gasket is the main sealing element in a flange connection, it connects tightly and prevents leakage. The flange gasket creates sufficient pressure between the bolt preload and the flange sealing surface to achieve a seal.
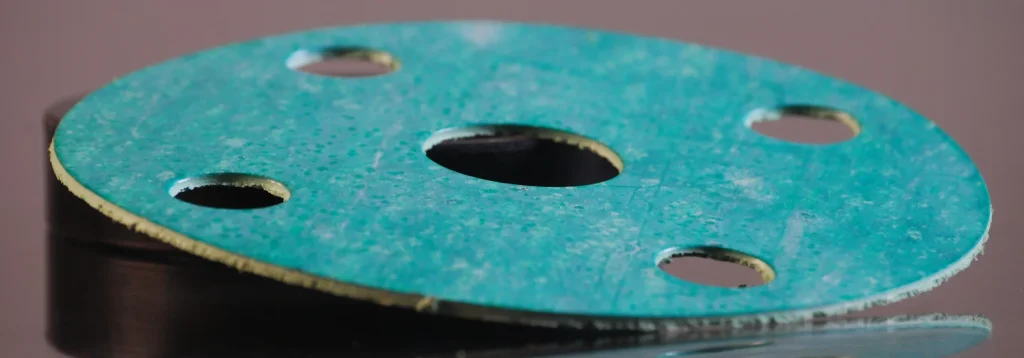
Types Of A Flange Gasket
Non-metallic Gaskets
Non-metallic gaskets have good elasticity and corrosion resistance, but relatively weak resistance to high temperature and pressure.
Rubber Gasket:
Material: Natural rubber, nitrile rubber, neoprene rubber, styrene-butadiene rubber, EPDM rubber, and so on.
Characteristics: Good flexibility, suitable for low temperature and medium pressure environment, part of the material has a certain degree of acid and alkali resistance and anti-aging properties.
Application Scenario: Seals for normal temperature, low pressure, water and non-corrosive media.
Asbestos Gasket:
Material: Made of a mixture of asbestos fiber and rubber.
Characteristics: High temperature resistance and excellent pressure resistance, but asbestos is harmful to human body and its use is restricted.
Alternative materials: Non-asbestos gaskets, usually made of synthetic fibers and rubber, with similar performance but without health hazards.
Application Scenario: Seals for medium and low pressure steam, water and gases.
Flexible Graphite Gasket:
Material: Cut or stamped from flexible graphite sheet.
Features: Excellent high temperature resistance, can maintain good sealing performance at high temperatures; high chemical stability, corrosion resistance; better resilience.
Application Scenario: Suitable for sealing of high temperature and strong corrosive medium.
Polytetrafluoroethylene (PTFE) Gasket:
Material: Polytetrafluoroethylene.
Characteristics: Excellent chemical stability, almost resistant to the erosion of all chemical media; very low coefficient of friction, good self-lubrication; but the compressive strength is low.
Application Scenario: Strong acids, alkalis and other corrosive media, as well as food, pharmaceutical and other industries with high cleanliness requirements.
Quel matériel faisons-nous ?
- Acier inoxydable
- Duplex&Super Duplex
- Alliage à base de nickel
- View More Materials
Semi-metallic Gaskets
Semi-metallic gaskets are made from a combination of metallic and non-metallic materials. It combines the strength of metal with the sealing properties of non-metal.
Metal Wound Gasket:
Structure and material: Metal bands (e.g. SS304, SS316, etc.) and non-metallic filler materials (e.g. graphite, PTFE, etc.). The outer layer is usually reinforced with a metal ring.
Characteristics:Excellent sealing performance, adaptable to large pressure and temperature fluctuations. Strong elastic compensation ability, according to different working conditions to choose different filling materials.
Application Scenario: Sealing of petroleum, chemical and other high-temperature, high-pressure pipes and equipment.
Metal Clad Gasket:
Structure and material: Non-metallic materials (such as graphite, ceramic fiber, etc.) as the inner core, outsourcing a layer of metal flakes (such as stainless steel, aluminum, etc.).
Characteristics: Both the softness of non-metallic gaskets and the strength and durability of metal materials; good compression resilience; can withstand high pressure.
Application Scenario: Suitable for medium and high pressure pipeline and equipment sealing.
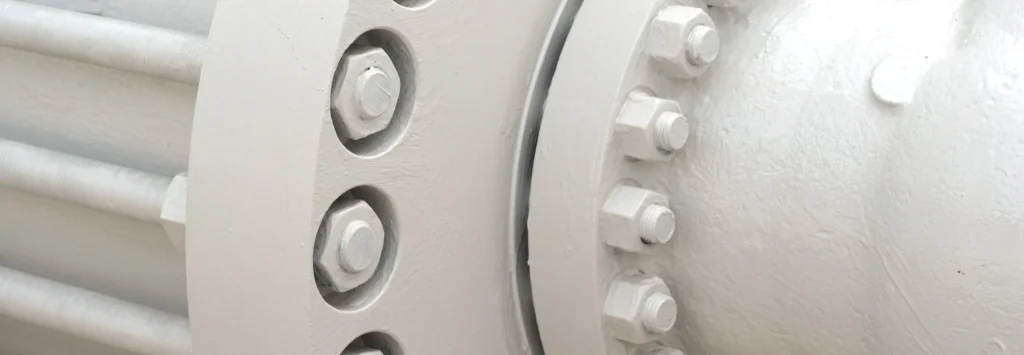
Metallic Gaskets
The use of metal or alloy materials by mechanical processing, with high strength, high temperature resistance, corrosion resistance.
Flat Metal Gaskets:
Structure and material: Flat ring gasket made of soft steel, stainless steel, aluminum and other metal materials.
Characteristics: High material strength, high temperature and high pressure resistance; but the sealing surface requirements are high, and depend on the flange surface flatness.
Application Scenario: High temperature and high pressure harsh working conditions.
Metal Ring Gasket:
Structure and material: Ring gasket made of metal materials (such as 304, 316 stainless steel, soft iron, mild steel, nickel-based alloys, etc.), with a specific cross-sectional shape (such as oval, octagonal, etc.).
Characteristics: Excellent sealing performance, dedicated to high-pressure flange connection.
Application Scenario: RTJ flange groove seals for high pressure environments.
Metal Waveform Gasket:
Structure and material: With corrugated metal surface, usually made of stainless steel or high temperature resistant metal materials.
Characteristics: The corrugated design increases the contact surface area and can adapt to the unevenness of the flange surface; provides good elasticity and sealing performance.
Application Scenario: High temperature and high pressure working conditions.
Metal Toothed gasket:
Structure and material: Surface with toothed metal design, usually made of stainless steel, carbon steel or alloy materials.
Characteristics: The toothed surface can effectively provide good sealing on the flange surface, and can also provide good sealing effect for uneven flange surface.
Application Scenario: Suitable for applications requiring high sealing performance.
Metal Lens Gasket:
Structure and Material: Shaped like a lens, thick in the center and thin on both sides, made of stainless steel or high temperature resistant metal materials.
Characteristics: Lens shape provides uniform sealing pressure distribution and good sealing performance for high pressure and high temperature environments.
Application Scenario: Suitable for sealing in high pressure and high temperature environments.
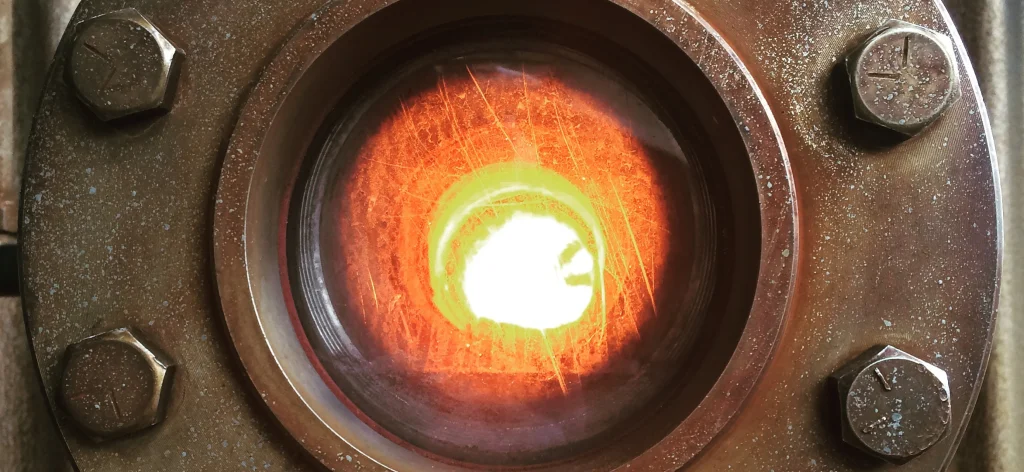
Application Scenarios and Importance
Flange gaskets are vital in a variety of industrial applications, particularly in the petrochemical, power and metallurgical industries. Proper selection and use of gaskets to reduce the risk of leakage can ensure safety and efficiency. At the same time, the performance of gaskets is influenced by their material, construction and installation. Choosing the right gasket is therefore essential to ensure the reliability of flanged connections.
Selection and Installation
When selecting flange gaskets, factors such as medium, pressure, temperature and type of flange sealing surface need to be considered. Because different media, pressures and temperatures have different requirements for the material and performance of flange gaskets. When installing the flange gasket, make sure that the gasket and flange sealing surface connection is well sealed. If you need, you can contact us to make the most suitable choice for you.