Définition des alliages à base de nickel
Les alliages dont la teneur en Ni dépasse 30wt% sont appelés alliages à base de nickel. Les produits courants ont une teneur en Ni supérieure à 50wt%. En raison de leur résistance mécanique à haute température et de leur résistance à la corrosion supérieures, ils sont combinés avec des alliages à base de fer et à base de cobalt en tant que superalliages (Superalliage).
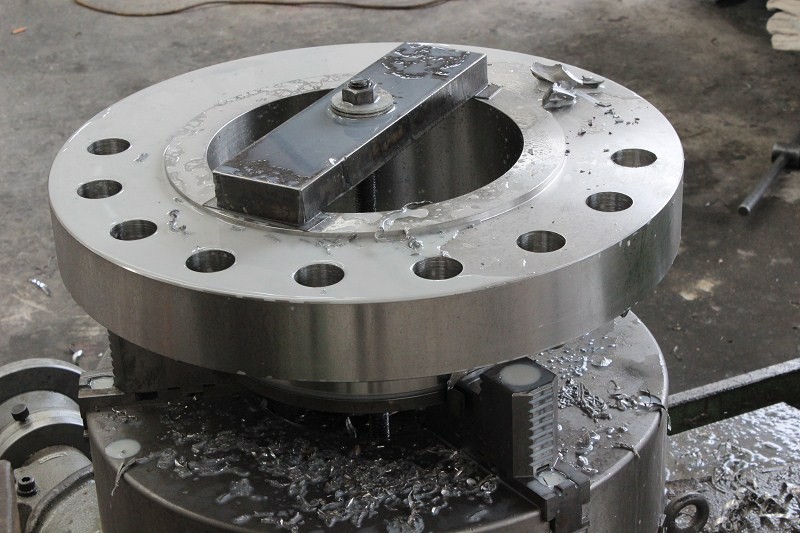
Ce type d'alliage est généralement utilisé dans un environnement à haute température supérieure à 540℃, et différents alliages sont sélectionnés en fonction de l'application. Il est principalement utilisé dans des environnements spéciaux résistants à la corrosion, des environnements de corrosion à haute température et des équipements nécessitant une résistance mécanique à haute température.
Il est souvent utilisé dans l'aérospatiale, l'énergie, l'industrie pétrochimique ou les domaines spéciaux de l'électronique/optoélectronique.
Champs d'application | Caractéristiques des exigences | Utilisation du produit |
Aérospatial | Maintenir une bonne résistance mécanique à des températures extrêmement élevées | Moteurs d'avion, turbines à gaz, soupapes de moteur |
Énergie | Bonne résistance à la vulcanisation à haute température et à l'oxydation à haute température | Pièces de fournaises, isolation, industrie du traitement thermique, industrie pétrolière et gazière |
Pétrochimique | Résistant à la corrosion des solutions aqueuses (acide, alcalin, ion chlorure) | Usine de dessalement, pipeline pétrochimique |
Électronique | Environnement général avec une faible résistance à la corrosion ou une résistance à haute température | Pièces de coque de batterie, cadre de plomb, couvercle de filet d'écran d'ordinateur |
Origine et développement
L'alliage à base de nickel a été développé à la fin des années 1930. L'alliage à base de nickel Nimonic 75 (Ni-20Cr-0,4Ti) a été produit pour la première fois au Royaume-Uni en 1941. Afin d'augmenter la résistance au fluage, de l'Al a été ajouté pour développer le Nimonic 80 (Ni-20Cr-2,5 Ti-1.3Al ); tandis que les États-Unis au milieu des années 1940, la Russie à la fin des années 1940, la Chine au milieu des années 1950 ont également développé des alliages à base de nickel.
Le développement des alliages à base de nickel comprend deux aspects, à savoir l'amélioration de la composition des alliages et l'innovation de la technologie de production.
Par exemple, au début des années 1950, le développement de la technologie de fusion sous vide a créé des conditions pour l'affinage d'alliages à base de nickel contenant des teneurs élevées en Al et Ti, et a entraîné une augmentation substantielle de la résistance de l'alliage et de la température de service. À la fin des années 1950, en raison de l'augmentation de la température de fonctionnement des aubes de turbine, les alliages devaient avoir une résistance à haute température plus élevée. Cependant, lorsque la résistance de l'alliage était élevée, il était difficile, voire impossible, de se déformer. Par conséquent, la technologie de moulage de précision a été utilisée pour développer une série de résistances à haute température. Des alliages de fonderie. Au milieu des années 1960, des superalliages directionnels cristallins et monocristallins et des superalliages de métallurgie des poudres plus performants ont été développés.
Afin de répondre aux besoins des navires et des turbines à gaz industrielles, un certain nombre d'alliages à base de nickel à haute teneur en Cr avec une bonne résistance à la corrosion thermique et une structure stable ont été développés depuis les années 1960. En 40 ans environ, du début des années 40 à la fin des années 70, la température de travail des alliages à base de nickel est passée de 700 à 1 100 °C, soit une augmentation annuelle moyenne d'environ 10 °C. Aujourd'hui, la température de service des alliages à base de nickel peut dépasser 1 100℃. De l'alliage Nimonic75 susmentionné avec une composition simple à l'alliage MA6000 récemment développé, la résistance à la traction à 1 100 ℃ peut atteindre 2 220 MPa et la limite d'élasticité est de 192 MPa; Sa durabilité dans des conditions de 1 100 ℃/137 MPa est d'environ 1 000 heures et il peut être utilisé pour les pales de moteurs d'avion.
Caractéristiques des alliages à base de nickel
Les alliages à base de nickel sont les matériaux les plus utilisés et les plus résistants dans les superalliages. Le nom du superalliage est dérivé des caractéristiques du matériau.
- (1) Excellentes performances : il peut maintenir une résistance élevée à haute température et présente une excellente résistance au fluage, une résistance à la fatigue et d'autres propriétés mécaniques, ainsi qu'une résistance à l'oxydation et à la corrosion, ainsi qu'une bonne plasticité et une bonne soudabilité.
- (2) L'ajout d'alliage est super compliqué : les alliages à base de Ni ajoutent souvent plus de dix éléments d'alliage pour améliorer la résistance à la corrosion de différents environnements ; et le renforcement de la solution solide ou le renforcement par précipitation.
- (3) L'environnement de travail est extrêmement difficile : les alliages à base de nickel sont largement utilisés dans diverses conditions de fonctionnement difficiles, telles que les pièces à haute température et haute pression des chambres à gaz des moteurs de vol aérospatiaux, les pièces structurelles pour l'énergie nucléaire, le pétrole, les industries marines et canalisations résistantes à la corrosion.
L'effet de divers éléments sur
Le nickel métallique conserve l'austénite et une structure cubique à faces centrées jusqu'à ce qu'il atteigne son point de fusion. Cela offre un degré de liberté pour la transition ductile-fragile, et réduit également considérablement les problèmes de fabrication causés par la coexistence d'autres métaux. Dans la séquence électrochimique, le nickel est inerte que le fer et plus actif que le cuivre. Par conséquent, dans un environnement réducteur, le nickel est plus résistant à la corrosion que le fer, mais pas le cuivre. À base de nickel et de chrome, l'alliage a une résistance à l'oxydation, ce qui permet de produire de nombreux types d'alliages avec une très large gamme d'applications, de sorte qu'ils puissent avoir la meilleure résistance aux environnements réducteurs et oxydants.
Compared with stainless steel and other iron-based alloys, nickel-based alloys can hold more alloying elements in a solid solution state, and can maintain good metallurgical stability. These factors allow the addition of a variety of alloying elements, so that a large number of nickel-based alloys can be used in various environnements corrosifs.
Les éléments communs aux alliages à base de nickel comprennent principalement :
Nickel:
Provide metallurgical stability, improve thermal stability and weldability, improve corrosion resistance to reducing acids and caustic soda, and improve fissuration par corrosion sous contrainte resistance, especially in chloride and caustic soda environments.
Chrome:
Améliorer les propriétés anti-oxydation et anti-oxydation à haute température, anti-soufre, et améliorer les propriétés anti-piqûres et corrosion caverneuse.
Molybdène:
Améliorez la résistance à la corrosion aux acides réducteurs, améliorez la résistance à la corrosion par piqûres et crevasses dans l'environnement de solution aqueuse contenant du chlorure et améliorez la résistance à haute température.
Le fer:
Améliorez la résistance à l'environnement de cémentation à haute température, réduisez le coût des alliages et contrôlez la dilatation thermique.
Le cuivre:
Améliorer la résistance à la corrosion des acides réducteurs (en particulier ceux de l'acide sulfurique et de l'acide fluorhydrique utilisés dans les endroits où l'air ne circule pas) et des sels. L'ajout de cuivre à l'alliage nickel-chrome-molybdène-fer contribue à améliorer la résistance à l'acide fluorhydrique, la résistance à la corrosion de l'acide phosphorique et de l'acide sulfurique.
Aluminium:
Améliore la résistance à l'oxydation à haute température et le durcissement par vieillissement.
Titane:
Combined with carbon, it reduces corrosion intergranulaire caused by chromium carbide precipitation during heat treatment and improves aging strengthening.
Niobium:
Combiné au carbone, il réduit la corrosion intergranulaire causée par la précipitation de carbure de chrome pendant le traitement thermique, améliore la résistance à la corrosion par piqûres et crevasses et améliore la résistance à haute température.
Tungstène :
Améliorer la résistance à la réduction de la corrosion acide et locale, améliorer la résistance et la soudabilité.
Azote:
Améliore la stabilité métallurgique, améliore la résistance à la corrosion par piqûres et crevasses et augmente la résistance.
Cobalt:
Fournit une résistance améliorée à haute température, une résistance améliorée à la carbonatation et à la vulcanisation.
Bon nombre de ces éléments d'alliage peuvent se combiner avec le nickel dans une large gamme de compositions pour former une solution solide monophasique, garantissant que l'alliage a une bonne résistance à la corrosion dans de nombreuses conditions corrosives. L'alliage présente également de bonnes propriétés mécaniques à l'état entièrement recuit, sans se soucier des modifications métallurgiques néfastes causées par la fabrication ou le traitement thermique. De nombreux alliages à haute teneur en nickel peuvent augmenter leur résistance par durcissement en solution solide, précipitation de carbure, durcissement par précipitation (vieillissement) et renforcement de la dispersion.
Posté par raccords de tuyauterie en acier inoxydable kaysuns