Expériences et résultats du soudage duplex de tubes en acier inoxydable
L'homme produit et utilise de l'acier inoxydable duplex depuis près de 80 ans. Les premiers alliages, tels que l'alliage malléable 329 et l'alliage coulé CD4MCu, contenaient beaucoup plus de ferrite que d'austénite.
Les gens ne font pas attention à l'importance de l'azote. De nombreux alliages contiennent très peu d'azote, de sorte que lorsque le traitement thermique n'est pas effectué après le soudage, la zone affectée thermiquement de ces alliages devient généralement fragile et a une mauvaise résistance à la corrosion. Le soudage au gaz du métal fondu présente également ce défaut.
Dans les années 1980, l'importance de l'azote pour tuyaux en acier inoxydable duplex était pleinement reconnu et les exigences minimales en matière de teneur en azote étaient généralement spécifiées. En ajoutant une teneur en azote appropriée au métal de base et en utilisant un métal d'apport de soudure avec une teneur en nickel accrue, la soudure peut avoir des quantités approximativement égales d'austénite et de ferrite à l'état soudé, ce qui améliore considérablement les propriétés mécaniques. Résistance à la corrosion améliorée.
Erreurs
Spécifications déraisonnables des métaux de base
Au cours des 25 dernières années, l'acier inoxydable duplex le plus courant est un alliage appelé 2205. La quasi-totalité de la littérature utilise la plage de composition de l'UNSS31803 pour décrire cet alliage. Cependant, l'UNS S31803 a une teneur minimale en azote de 0,08%.
La pratique a prouvé que ce niveau de teneur en azote est trop faible, si la zone affectée thermiquement et la zone de fusion doivent maintenir de bonnes performances dans des conditions post-soudage. Après avoir réalisé ce problème, ASTM a utilisé UNSS32205 pour définir 2205 depuis 2000.
Le tableau 1 montre la plage de composition de UNS S31803 et UNS S32205. Il convient de noter que, par rapport au S31803, en plus d'augmenter la teneur minimale en azote, la teneur minimale en chrome et en molybdène a également augmenté.
Table de composition de 2205 duplex en acier inoxydable | |||||||||
UNS | Gamme de composition chimique /% (maximum) | ||||||||
C | Mn | P | S | Si | Cr | Ni | Mo | N | |
S31803 | 0.030 | 2.000 | 0.030 | 0.020 | 1.000 | 21.0~23.0 | 4.5~6.5 | 2.5~3.5 | 0.08~0.20 |
S32205 | 0.030 | 2.000 | 0.030 | 0.020 | 1.000 | 22.0~23.0 | 4.5~6.5 | 3.0~3.5 | 0.14~0.20 |
Tableau 1
La figure 1 montre la microstructure de l'acier forgé conforme à la composition de l'UNS S31803 mais pas à la composition de l'UNS S32205, et la répartition des éléments d'alliage entre la phase ferrite et la phase austénite. Pour le S32205, la teneur en azote de 0,12% est trop faible.
Sur la figure 1 (a), la ferrite est d'un gris plus foncé, tandis que l'austénite est presque blanche. On peut voir sur la figure que la phase ferrite est riche en chrome et molybdène et la phase austénite est riche en nickel et en azote.
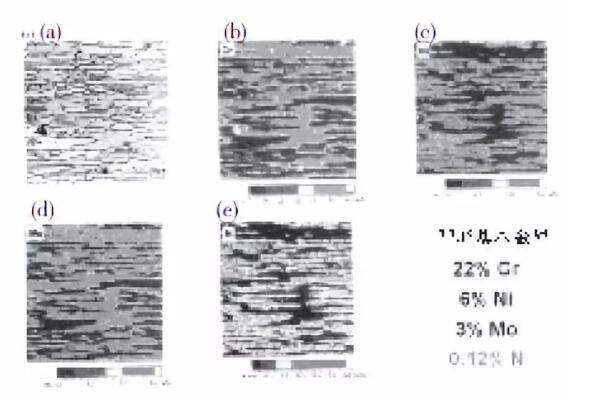
En particulier, la teneur en chrome dans la ferrite est d'environ 25% et seulement de 20% dans l'austénite, comme le montre la figure 1 (b). La teneur en molybdène dans la ferrite est d'environ 3,5%, dans l'austénite La teneur en molybdène n'est que de 2,5%, comme le montre la figure 1 (d). La teneur en nickel dans l'austénite est de 7,5%, et elle est d'environ 5% dans la ferrite. Voir figure 1 (c), la teneur en azote dans l'austénite est d'environ 0,3%, et est nulle dans la ferrite, comme le montre la figure 1 (e).
La répartition des phases est fondamentalement équilibrée. L'acier étant un produit laminé à chaud, la structure est en forme de bande.
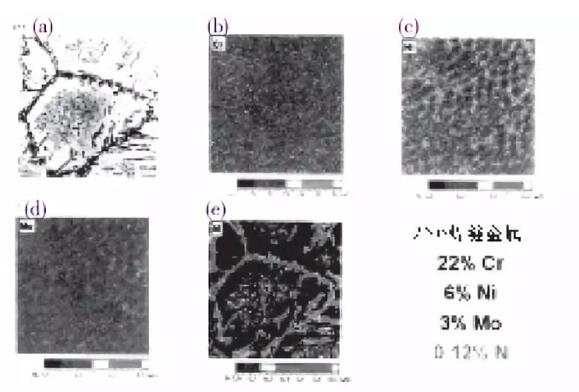
Par rapport à la figure 1, la figure 2 montre la microstructure et la distribution des éléments d'alliage de la zone de fusion de la soudure GTA auto-fondante de UNSS31803, qui est la même que le matériau de la figure. 1.
Il est difficile de voir le modèle de distribution des éléments d'alliage sur les Fig. 2 (b), 2 (c) ou 2 (d) similaire à la distribution de phase de la figure 2 (a). Cependant, la distribution d'azote indique que la concentration d'azote dans les paillettes d'austénite autour des joints de grains de ferrite est plus élevée que celle dans les grains de ferrite. Cela peut être dû au temps suffisant pour que l'azote dans ces régions diffuse dans l'austénite sur les joints de grains de ferrite, ce qui fait que la région à côté de la plaque d'austénite ne contient pratiquement pas d'azote, comme le montre la figure 2 (e).
À l'intérieur des grains de ferrite, l'azote est bloqué, il n'y a aucune chance de pénétrer dans l'austénite et il précipite sous forme de nitrure de chrome, ce qui est clairement visible, comme le montre la figure 2 (a). Pour la zone de fusion, la combinaison de gros grains de ferrite et de précipités de nitrure de chrome est très préjudiciable à la ténacité et à la résistance à la corrosion de la zone de fusion.
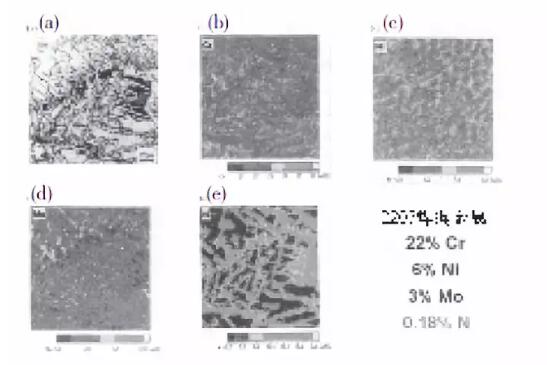
En effet, comme mentionné précédemment, 100% de la solidification dans la zone de fusion est de la ferrite. Ensuite, lorsque la transformation en austénite commence, la diffusion est nécessaire.
Étant donné que le chrome, le nickel et le molybdène sont des éléments de remplacement, ils diffusent relativement lentement à l'état solide, de sorte qu'ils ne peuvent pas atteindre une répartition équilibrée entre la ferrite et l'austénite dans des conditions normales de refroidissement du soudage. L'azote est un élément interstitiel et sa vitesse de diffusion est environ 100 fois plus rapide que celle de l'élément de remplacement. En conséquence, il a plus de capacité à entrer dans l'austénite, bien que la composition ne soit pas complètement entrée comme le montre la Fig. 2.
Dans les matériaux contenant de l'azote 0,12%, la partie la plus chaude de la ZAT se comporte de la même manière que le métal fondu. En particulier, il est composé de ferrite 100% puis se transforme en partie en austénite à l'état solide. Par conséquent, il est plus enclin à former de gros grains de ferrite et des flocons d'austénite formés le long des joints de grains de ferrite d'origine.
La figure 3 montre la microstructure et la distribution des éléments d'alliage dans la zone de fusion GTA lorsque la teneur en azote de l'alliage 2205 est supérieure à la teneur en azote indiquée sur la figure 2 et respecte les limites de composition des normes UNS S31803 et S32205.
La teneur en azote du métal déposé sur la figure 3 est plus élevée (la teneur en azote est de 0,18%, alors que la teneur en azote de la figure 2 est de 0,12%), ce qui modifie considérablement la microstructure après soudage. En particulier, on peut clairement voir sur la figure 3 (a) qu'il se forme plus d'austénite que l'austénite formée sur la figure 2 (a), et l'austénite est dispersée à travers l'ensemble des grains de ferrite au lieu d'être principalement limitée au fer. Joint de grain du corps de l'élément. Par rapport à la fig. 2 (a), la précipitation du nitrure de chrome n'est pas visible sur la Fig. 3 (a). Au lieu de cela, tout l'azote pénètre dans l'austénite, comme le montre la figure 3 (e). De plus, sur les figures 3 (b) et (d), une petite distribution de chrome et de molybdène est clairement visible dans cette région. Grains de ferrite primaire.
En raison de la teneur en azote plus élevée de cet échantillon, la formation d'austénite peut commencer à des températures plus élevées que les alliages 0,12% N, et comme la diffusion et la transformation commencent à des températures plus élevées, le molybdène et le chrome peuvent diffuser plus rapidement, la diffusion prendra plus de temps. On peut également voir sur la figure 3 (a) que les paillettes d'austénite formées sur la totalité des grains de ferrite d'origine ont brisé les gros grains de ferrite d'origine. Comme les grains de ferrite d'origine sont brisés en petits grains par les bandes d'austénite internes, la ténacité est améliorée. Et parce qu'aucun nitrure de chrome n'est précipité, la résistance à la corrosion est améliorée. Il en est de même dans la partie à haute température de la zone affectée thermiquement. De cette façon, on peut conclure que UNSS32205 avec une teneur en azote plus élevée dans la figure 3 est nettement meilleur que UNS S31803 avec une teneur en azote plus faible dans la figure 2.
La composition limite de l'alliage 2550 | ||||||||||
UNS | Gamme de composition chimique /% (maximum) | |||||||||
C | Mn | P | S | Si | Cr | Ni | Mo | N | Cu | |
S32550 | 0.040 | 1.500 | 0.035 | 0.030 | 1.000 | 24.0~27.0 | 4.5~6.5 | 2.9~3.9 | 0.10~0.25 | 1.50~2.50 |
S32520 | 0.030 | 1.500 | 0.030 | 0.020 | 0.800 | 24.0~26.0 | 5.5~8.0 | 3.0~4.0 | 0.20~0.35 | 0.50~2.00 |
Tableau 2
Il est clair que UNS S31803 ne convient pas comme métal de base pour une utilisation après soudage, et UNS S32205 doit être utilisé. Parmi les aciers inoxydables duplex, UNS S31803 n'est pas le seul métal de base qui ne convient pas au soudage des structures. Il en va de même pour l'alliage 255, qui est un composant de l'UNS S32550. Le tableau 2 compare la composition des UNSS32550 et UNSS32520 utilisés pour le surfaçage. La composition est généralement la même. Cependant, la teneur minimale en azote de l'UNS S32520 est supérieure à celle de l'UNS S32550. De toute évidence, UNS S32520 est plus adapté aux applications post-soudage. De plus, UNSS32550 peut également être utilisé, mais la teneur en azote de la composition de l'acier doit être contrôlée à la limite supérieure.
Apport de chaleur de soudage déraisonnable
La vision traditionnelle de l'apport de chaleur de soudage est que lors du soudage d'acier inoxydable duplex avec une teneur en chrome 22%, l'apport de chaleur doit être limité à 0,5 2,5kJ / mm, et lors du soudage d'acier inoxydable super duplex avec une teneur en chrome 25%, l'apport de chaleur doit être limité à 0,5 ~ 1,5 kJ / mm.
Lorsqu'un apport de chaleur inférieur est utilisé, même pour les aciers duplex à haute teneur en azote, l'austénite est refroidie à une vitesse très rapide. La formation est également insuffisante. Lorsqu'un apport de chaleur plus élevé (> 1,5 kJ) est utilisé, dans des conditions de refroidissement lent, les composés intermétalliques ont tendance à précipiter dans la ferrite. Par rapport à l'acier inoxydable duplex 22% Cr, la tendance de l'acier inoxydable super duplex 25% Cr est plus évidente.
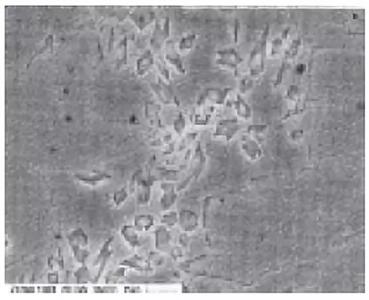
La figure 4 montre la microstructure du métal fondu près de l'épaisseur moyenne de l'échantillon. Il existe un grand nombre de précipités angulaires dans la ferrite seule. Cependant, il n'a pas été déterminé exactement quel était le précipité. Notre conclusion est que les précipités ont été générés par chauffage répété pendant douze passages de l'éprouvette.
Le fonctionnement normal lors du soudage d'aciers inoxydables duplex, en particulier de tuyaux en acier inoxydable super duplex, est que l'apport de chaleur au niveau du cordon de racine est supérieur au congé d'origine. L'utilisation de cordon de racine d'une épaisseur d'environ 6 mm est assez bonne.
Traitement thermique après soudage déraisonnable
Si les pièces moulées ou les têtes soudées nécessitent un traitement thermique post-soudage, alors l'utilisation de métaux d'apport riches en nickel couramment utilisés, associée à l'utilisation de températures de recuit déraisonnables qui répondent aux spécifications de base des métaux, amènera les fabricants de traitement d'acier inoxydable duplex à commettre une autre erreur (pour l'acier inoxydable duplex, la teneur en nickel est généralement de 9%, d'autres sont similaires aux métaux d'apport).
L'exigence générale est de recuit à une température minimale de 1040 ° C puis de tremper à l'eau à partir de la température de recuit. Parce que les gens ne savent pas que la phase est presque toujours formée dans l'acier inoxydable duplex pendant le chauffage à la température de recuit, et plus la teneur en nickel augmentera la température de la phase de solution solide de la phase . Dans ce cas, le métal d'apport riche en nickel est dangereux.
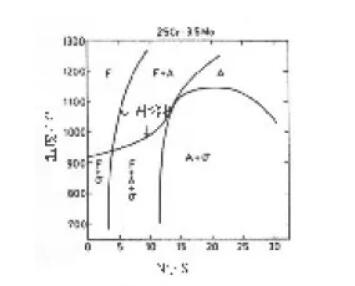
La figure 5 réalisée par Grobner montre l'effet du nickel sur la température de la phase en solution solide de la phase de l'alliage 25% Cr-3.5% Mo.
Bien que l'alliage utilisé pour dessiner ce diagramme ne contienne pas d'éléments d'alliage tels que le manganèse, le silicium et l'azote, il est pratique pour les gens de comprendre l'effet du nickel dans la nature. Il montre clairement que la température de la phase de solution solide de la phase augmente avec l'augmentation de la teneur en nickel. En particulier, la température de ligne de phase de solution solide en phase du métal fondu contenant 9% Ni sera d'au moins 50 °C supérieure à la température de ligne de phase de solution solide de phase du métal de base adapté contenant 5% Ni.
Conclusion
La pratique a prouvé que l'acier inoxydable duplex, y compris l'acier inoxydable super duplex, a de bonnes performances de soudage et est un matériau d'ingénierie très important.
Cependant, en raison de la négligence et de l'ignorance, certaines erreurs peuvent être commises. Afin que la zone affectée thermiquement et le métal de soudure aient de bonnes performances, il convient d'utiliser un métal de base avec une teneur élevée en azote d'au moins 0,14% d'azote. Sinon, une grande quantité de ferrite et de nitrure de chrome sera précipitée dans la zone affectée thermiquement, ce qui endommagera la résistance à la corrosion et les propriétés mécaniques.
Afin d'éviter la précipitation d'acier inoxydable super duplex dans la zone de chauffage répétée, l'utilisation d'une grande quantité d'apport de chaleur faible et de petits cordons doit être évitée. Et lors du soudage de tuyaux en acier inoxydable duplex et super duplex, pour éviter les précipitations sur la surface interne du tuyau, le cordon de racine doit utiliser un apport de chaleur plus élevé (supérieur à 1kJ/mm), qui est supérieur à l'apport de chaleur du quelques premières soudures continues.
Le recuit post-soudage de l'acier inoxydable duplex soudé doit tenir compte du fait que la température de la phase du métal fondu qui dissout le métal fondu riche en nickel est plus élevée que celle du métal de base.