L'acier inoxydable super austénitique est actuellement le matériau le plus approprié pour le processus de désulfuration des gaz de combustion humides
Ce procédé est également le plus couramment utilisé avec l'acier inoxydable super austénitique dans le monde aujourd'hui. Parmi les nombreuses technologies de désulfuration, elle représente 80% de la capacité totale installée de désulfuration. Il est toujours au-dessus d'une plage constante.
La désulfuration humide des gaz de combustion au calcaire-gypse est le procédé de désulfuration le plus couramment utilisé dans la désulfuration humide des gaz de combustion.
L'environnement corrosif à l'intérieur du système de désulfuration des gaz de combustion humides est difficile et l'équipement interne du système est facilement corrodé. Faire un bon travail anticorrosion est une mesure importante pour assurer le fonctionnement sûr et stable de l'usine et contrôler la centrale électrique pour éviter les émissions.
L'acier inoxydable super austénitique est riche en une grande quantité de Cr, Ni, Mo et des quantités appropriées d'éléments d'alliage tels que N et Cu, résistant à l'acide sulfurique dilué et à la corrosion par piqûres, la résistance à la corrosion caverneuse est équivalente aux alliages à base de nickel, a une excellente propriétés mécaniques et performances de résistance à la corrosion. Parmi eux, le Mo peut améliorer la résistance globale à la corrosion de l'acier inoxydable super austénitique, en particulier la résistance à la corrosion par piqûres d'ions chlorure. L'acier inoxydable super austénitique 6% Mo présente une meilleure résistance à la corrosion dans les solutions acides contenant des ions chlorure et convient mieux à une application dans le système de désulfuration des gaz de combustion.
Flux de processus du système de processus de désulfuration des gaz de combustion humides
Le principal processus technologique de base de la désulfuration humide des fumées calcaire-gypse est le suivant : après que les fumées de la chaudière ont été dépoussiérées par un précipitateur électrique et boostées par un ventilateur d'appoint, puis refroidies par un échangeur de chaleur des fumées, elles pénètrent dans la tour d'absorption. La boue de calcaire est pulvérisée dans la tour d'absorption pour réagir avec les gaz de combustion afin d'éliminer le SO2, le SO3, le HCl et le HF dans les gaz de combustion. La boue de calcaire est transférée à la couche de pulvérisation via la pompe de circulation de boue, puis atomisée à travers la buse, de sorte que la boue et les gaz de combustion puissent être complètement en contact et complètement réagis. Les fumées désulfurées se réchauffent à travers l'échangeur de chaleur des fumées pour augmenter leur diffusivité, et sont finalement évacuées dans la cheminée, qui est rejetée dans l'atmosphère.
Dans la tour d'absorption, la réaction chimique complexe entre la boue calcaire et le dioxyde de soufre dans les gaz de combustion produit du gypse. Cette partie de la boue de gypse traverse la pompe de décharge de la tour d'absorption et pénètre dans le système de déshydratation du gypse. Le système de déshydratation comprend principalement un cyclone de gypse, un déshydrateur à bande sous vide et un distributeur de lisier. Le flux de gaz de combustion après la réaction est désembué par un dispositif de désembuage pour éliminer les gouttelettes de brouillard de boue dans les gaz de combustion. Dans le même temps, l'eau de traitement de la centrale électrique doit être utilisée pour rincer de temps en temps le dévésiculeur. Le rinçage du dévésiculeur a deux objectifs principaux, l'un est d'empêcher le désembuage de se boucher, et l'autre est d'utiliser l'eau de rinçage comme eau supplémentaire pour stabiliser le niveau de liquide de la tour d'absorption.
A la sortie de la tour d'absorption, les fumées sont généralement refroidies à environ 50°C et contiennent une grande quantité de vapeur d'eau saturée. Après avoir traversé l'échangeur de chaleur des fumées, les fumées sont chauffées à plus de 80 ℃, principalement pour améliorer la hauteur de levage et la capacité de diffusion des fumées, éliminant ainsi le phénomène de pluie de gypse. Enfin, des fumées propres et conformes aux normes d'émission de fumées de la centrale électrique sont rejetées dans l'atmosphère par la cheminée.
Application de l'acier inoxydable super austénitique dans le système de processus de désulfuration des gaz de combustion humides
Dans certaines centrales électriques, les fumées du charbon passent à travers la tour d'absorption et sont évacuées directement dans la cheminée sans réchauffeur de fumées (WGGH). Ce type de cheminée devient une cheminée humide. Certaines centrales n'installent pas de réchauffeur de fumées après la tour d'absorption mais un dépoussiéreur électrique humide (WESP). Le gaz de combustion traverse le dépoussiéreur électrique humide et est évacué par la cheminée. On peut voir que l'environnement corrosif de la cheminée humide, du dépoussiéreur électrostatique humide et du réchauffeur de gaz de combustion est équivalent.
Les cheminées humides sont revêtues de matériaux métalliques anti-corrosion dont l'acier inoxydable super austénitique, les alliages à base de nickel, les plaques composites en acier au titane, etc. :
- Les alliages à base de nickel ont une bonne résistance à la corrosion. L'alliage Nicrofer 5923 h Mo-59, l'alliage Nicrofer 3127h Mo-31, l'alliage Cronifer 1925 h Mo-926, etc. sont typiques.
- Le titane a une bonne résistance, ses performances de soudage sont médiocres et sa résistance est faible.
- Le prix de l'acier inoxydable super austénitique est bien inférieur à celui des alliages à base de nickel. Il a d'excellentes performances de soudage et peut être directement soudé avec de l'acier au carbone. Il a d'excellentes propriétés mécaniques et performances de traitement, et est un matériau plus approprié
254SMo est une sorte d'acier couramment utilisé dans 6Mo. Il a une excellente résistance à la corrosion par piqûres. Il est largement utilisé dans les équipements de traitement industriels riches en ions halogènes tels que l'eau de mer. Il peut être utilisé pour remplacer des matériaux coûteux tels que les alliages à base de nickel ou le titane. Il existe également quelques applications dans les systèmes de désulfuration des gaz de combustion.
Cet article prend le 254SMo comme exemple pour étudier la résistance à la corrosion de l'acier inoxydable super austénitique 6Mo dans la cheminée humide et le réchauffeur de gaz de combustion.
Test de la courbe de polarisation
La préparation des échantillons
Les matériaux d'essai sont le 316L, le 317L et le 254SMo, et leurs principaux composants sont indiqués dans le tableau 1.

Les tubes en acier inoxydable des trois matériaux ont été découpés mécaniquement pour faire des échantillons de 20 mm x 5 mm x 0,7 mm. Les échantillons ont été polis sur du papier de verre 01# autour des échantillons.
Après nettoyage aux ultrasons pendant 15 min et passivation à l'acide nitrique concentré pendant 30 min, la face arrière a été soudée avec des fils de cuivre, puis l'acétone nettoie la graisse fixée à la surface de l'électrode, et enfin la surface non fonctionnelle est encapsulée avec de la résine époxy, la surface de travail est de 20 mm ×5mm.
Les électrodes emballées sont poncées avec différentes rugosités de grossière à fine, puis polies au papier de verre 01# pour utilisation.
Méthode d'essai
Le test utilise un système à trois électrodes. L'électrode de travail est une électrode plane fabriquée par nos soins du matériau mesuré, l'électrode de référence est une électrode au calomel saturé (SCE) et l'électrode auxiliaire est une électrode de platine. La vitesse de balayage potentielle est de 1 mV/s et la fréquence de balayage est de 2 Hz. Le milieu de test est un condensat de gaz de combustion (pH = 1,84), puis du NaCl est ajouté au condensat de gaz de combustion pour préparer 1000 mg/L et 40000 mg/L deux solutions différentes de milieu de test de concentration en Cl, et les autres concentrations d'ions restent inchangées .
La température de test est sélectionnée pour être de 50 et la précision du contrôle de la température est de 0,1 . Le potentiel de piqûre du matériau a été testé par la méthode de balayage de potentiel dynamique, et le test a commencé à partir de -400 mV par rapport à l'électrode de référence jusqu'à ce que le courant d'anode atteigne 0,2 ~ 1,0 mA/cm2.
Chaque matériau est testé trois fois dans les mêmes conditions de travail pour s'assurer que les résultats des tests sont vrais et fiables.
Résultats de test
La figure 1 montre les courbes de polarisation de l'acier inoxydable 316L et de l'acier inoxydable 317L dans des condensats de fumées 1000 mg/LCl et de l'acier inoxydable super austénitique 254SMo dans des condensats de fumées 40000 mg/LCl.

On peut voir que le potentiel de piqûre du 316L est inférieur à celui du 317L lorsque la concentration en Cl est de 1000 mg/L dans le condensat des gaz de combustion.
Le potentiel de piqûres de l'acier inoxydable diminue généralement avec l'augmentation de la concentration de Cl dans le milieu de solution. Cependant, lorsque la concentration de Cl dans le condensat des gaz de combustion atteint 40 000, le potentiel de piqûre du 254SMo est encore très élevé et se trouve dans un état surpassivé. On peut voir que le 254SMo a une meilleure résistance à la corrosion par piqûres dans les condensats de gaz de combustion avec une concentration en Cl plus élevée.
La teneur en éléments d'alliage tels que Cr et Mo dans le 254SMo est relativement élevée. Parmi eux, Cr est l'élément principal pour former le film de passivation. L'augmentation de la teneur en Cr peut rendre le film de passivation plus stable ; et la teneur plus élevée en Mo peut donner à la surface de l'acier un aspect. Un film protecteur de MoOCl2 est formé dans le milieu où Cl- est présent, empêchant ainsi efficacement Cl- de pénétrer dans le film de passivation.
L'ampleur du courant d'émoussage dimensionnel dans la courbe de polarisation peut caractériser le taux de corrosion uniforme de l'acier inoxydable. Selon la loi de Faraday, il existe une relation quantitative stricte entre l'indice de courant de corrosion et l'indice de poids. Plus le courant de corrosion est important, plus la vitesse de corrosion du métal est rapide, ce qui représente la résistance du matériau. Plus la performance de la résistance uniforme à la corrosion est mauvaise. Expliquez la performance de la résistance uniforme à la corrosion 254SMo>316L>317L.
Tests sur site
Les taux de corrosion des trois matériaux en acier inoxydable sont indiqués sur la figure 2. Comme on peut le voir sur la figure, le taux de corrosion du 317L est légèrement supérieur à celui du 316L, respectivement 0,081μm/a et 0,069μm/a, qui est le Identique aux résultats du test de la courbe de polarisation Est cohérent.
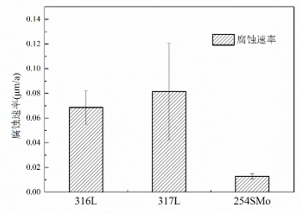
Le taux de corrosion de 254SMo est beaucoup plus faible que les deux précédents, qui est de 0,013μm par an. En raison de l'existence d'erreurs de pesée, la corrosion du 254SMo est presque négligeable. On peut voir que le 254SMo a une meilleure résistance à la corrosion uniforme dans les conditions réelles de fonctionnement.
Sommaire
- 1) L'acier inoxydable super austénitique a une bonne résistance à la corrosion par piqûres de Cl en solution acide et son prix est inférieur à celui de l'alliage à base de nickel, qui convient mieux à une application dans le système de désulfuration humide des gaz de combustion ;
- 2) Le test de courbe de gradient et le test sur site montrent que le 254SMo a une excellente résistance à la corrosion dans les condensats de gaz de combustion et peut répondre aux conditions de travail d'équipements tels que la cheminée humide et le réchauffeur de gaz de combustion ;
- 3) L'acier inoxydable super austénitique 904L et AL-6XN peut être bien utilisé dans les tours d'absorption de désulfuration, et c'est une bonne direction de sélection de matériaux pour les tours d'absorption pour remplacer les matériaux non métalliques par des matériaux en alliage.