Experimentos y resultados de la soldadura de tubos de acero inoxidable dúplex
Man ha producido y utilizado acero inoxidable dúplex durante casi 80 años. Las primeras aleaciones, como la aleación maleable 329 y la aleación fundida CD4MCu, contenían mucha más ferrita que austenita.
La gente no presta atención a la importancia del nitrógeno. Muchas aleaciones contienen muy poco nitrógeno, por lo que cuando no se realiza el tratamiento térmico después de la soldadura, la zona afectada por el calor de estas aleaciones generalmente se vuelve quebradiza y tiene poca resistencia a la corrosión. El metal de soldadura de soldadura con gas también tiene este defecto.
En la década de 1980, la importancia del nitrógeno para tubos de acero inoxidable dúplex se reconoció plenamente y, por lo general, se especificaron los requisitos mínimos de contenido de nitrógeno. Añadiendo un contenido de nitrógeno apropiado al metal base y usando un metal de aportación de soldadura con un mayor contenido de níquel, la soldadura puede tener cantidades aproximadamente iguales de austenita y ferrita en el estado soldado, lo que mejora significativamente las propiedades mecánicas. Mejor resistencia a la corrosión.
Errores
Especificaciones de metal base irrazonables
En los últimos 25 años, el acero inoxidable dúplex más común es una aleación llamada 2205. Casi toda la literatura utiliza el rango de composición de UNSS31803 para describir esta aleación. Sin embargo, el UNS S31803 tiene un contenido mínimo de nitrógeno de 0,08%.
La práctica ha demostrado que este nivel de contenido de nitrógeno es demasiado bajo, si la zona afectada por el calor y la zona de fusión deben mantener un buen rendimiento en condiciones posteriores a la soldadura. Después de darse cuenta de este problema, ASTM ha utilizado UNSS32205 para definir 2205 desde 2000.
La Tabla 1 muestra el rango de composición de UNS S31803 y UNS S32205. Cabe señalar que, en comparación con S31803, además de aumentar el contenido mínimo de nitrógeno, también aumentó el contenido mínimo de cromo y molibdeno.
Mesa de composición de acero inoxidable dúplex 2205 | |||||||||
UNS | Rango de composición química / % (máximo) | ||||||||
C | Minnesota | P | S | Si | Cr | Ni | Mes | norte | |
S31803 | 0.030 | 2.000 | 0.030 | 0.020 | 1.000 | 21.0~23.0 | 4.5~6.5 | 2.5~3.5 | 0.08~0.20 |
S32205 | 0.030 | 2.000 | 0.030 | 0.020 | 1.000 | 22.0~23.0 | 4.5~6.5 | 3.0~3.5 | 0.14~0.20 |
tabla 1
La Figura 1 muestra la microestructura del acero forjado que se ajusta a la composición de UNS S31803 pero no a la composición de UNS S32205, y la distribución de los elementos de aleación entre la fase de ferrita y la fase de austenita. Para S32205, el contenido de nitrógeno de 0.12% es demasiado bajo.
En la Figura 1 (a), la ferrita es de un gris más oscuro, mientras que la austenita es casi blanca. Se puede ver en la figura que la fase de ferrita es rica en cromo y molibdeno y la fase de austenita es rica en níquel y nitrógeno.
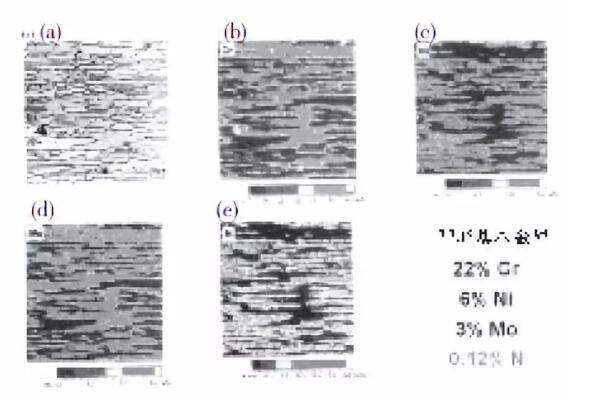
En particular, el contenido de cromo en la ferrita es de aproximadamente 25% y solo 20% en la austenita, como se muestra en la Figura 1 (b). El contenido de molibdeno en la ferrita es aproximadamente 3.5%, en la austenita El contenido de molibdeno es solo 2.5%, como se muestra en la Figura 1 (d). El contenido de níquel en la austenita es 7.5%, y es aproximadamente 5% en la ferrita. Consulte la Figura 1 (c), el contenido de nitrógeno en la austenita es de aproximadamente 0.3%, y es cero en la ferrita, como se muestra en la Figura 1 (e).
La distribución de fases está básicamente equilibrada. Dado que el acero es un producto laminado en caliente, la estructura tiene forma de banda.
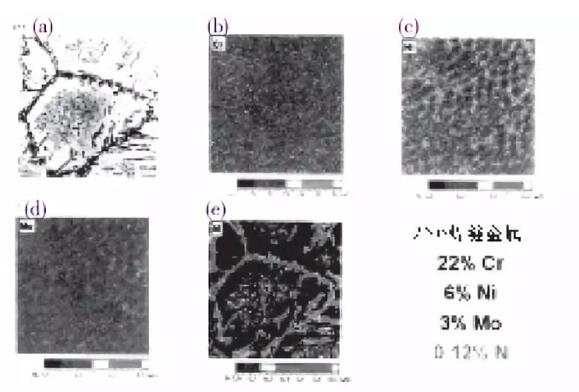
En comparación con la Figura 1, la Figura 2 muestra la microestructura y la distribución del elemento de aleación de la zona de fusión de la soldadura GTA autofundente de UNSS31803, que es el mismo que el material de la FIG. 1.
Es difícil ver el patrón de distribución de los elementos de aleación en las Figs. 2 (b), 2 (c) o 2 (d) similar a la distribución de fase de la Fig. 2 (a). Sin embargo, la distribución de nitrógeno indica que la concentración de nitrógeno en las escamas de austenita alrededor de los límites de los granos de ferrita es mayor que en los granos de ferrita. Esto puede deberse al tiempo suficiente para que el nitrógeno en estas regiones se difunda en la austenita en los límites del grano de ferrita, lo que da como resultado que la región próxima a la placa de austenita no contenga prácticamente nitrógeno, como se muestra en la Figura 2 (e).
Dentro de los granos de ferrita, el nitrógeno está bloqueado, no hay posibilidad de ingresar a la austenita y se precipita como nitruro de cromo, que es claramente visible, como se muestra en la Figura 2 (a). Para la zona de fusión, la combinación de grandes granos de ferrita y precipitados de nitruro de cromo es muy perjudicial para la tenacidad y resistencia a la corrosión de la zona de fusión.
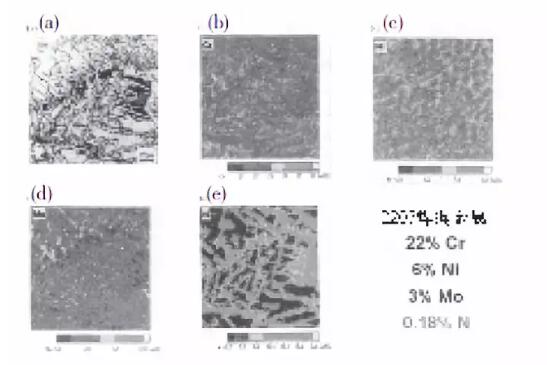
De hecho, como se mencionó anteriormente, 100% de la solidificación en la zona de fusión es ferrita. Luego, cuando comienza la transformación a austenita, se requiere difusión.
Dado que el cromo, el níquel y el molibdeno son elementos de reemplazo, se difunden relativamente lentamente en estado sólido, por lo que no pueden lograr una distribución equilibrada entre ferrita y austenita en condiciones normales de enfriamiento de soldadura. El nitrógeno es un elemento intersticial y su tasa de difusión es aproximadamente 100 veces más rápida que la del elemento de reemplazo. Como resultado, tiene más capacidad para ingresar austenita, aunque la composición no ingresa completamente como se muestra en la FIG. 2.
En materiales que contienen nitrógeno 0.12%, la parte más caliente de la ZAT se comporta de manera similar al metal de soldadura. En particular, está compuesto de ferrita 100% y luego se transforma parcialmente en austenita en estado sólido. Por lo tanto, es más propenso a formar grandes granos de ferrita y escamas de austenita formadas a lo largo de los límites originales de los granos de ferrita.
La Figura 3 muestra la microestructura y la distribución de los elementos de aleación en la zona de fusión de GTA cuando el contenido de nitrógeno de la aleación 2205 es mayor que el contenido de nitrógeno que se muestra en la Figura 2 y cumple con los límites de composición de UNS S31803 y S32205.
El contenido de nitrógeno del metal de soldadura en la Fig. 3 es mayor (el contenido de nitrógeno es 0.18%, en comparación con el contenido de nitrógeno de la Fig. 2 es 0.12%), lo que cambia significativamente la microestructura después de la soldadura. En particular, puede verse claramente en la Fig. 3 (a) que se forma más austenita que la austenita formada en la Fig. 2 (a), y la austenita se dispersa a través de todos los granos de ferrita en lugar de limitarse principalmente al hierro. Límite de grano del cuerpo del elemento. Comparado con la FIG. 2 (a), la precipitación de nitruro de cromo no se ve en la FIG. 3 (a). En cambio, todo el nitrógeno entra en la austenita, como se muestra en la Figura 3 (e). Además, en la Figura 3 (b) y (d), se puede ver claramente una pequeña distribución de cromo y molibdeno en esta región. Granos de ferrita primarios.
Debido al mayor contenido de nitrógeno de esta muestra, la formación de austenita puede comenzar a temperaturas más altas que las aleaciones 0.12% N, y como la difusión y transformación comienzan a temperaturas más altas, el molibdeno y el cromo pueden difundirse más rápido, la difusión tomará más tiempo. También se puede ver en la Fig. 3 (a) que las escamas de austenita formadas en todos los granos de ferrita originales rompieron los granos de ferrita gruesos originales. Como los granos de ferrita originales se rompen en pequeños granos por las tiras internas de austenita, se mejora la tenacidad. Y debido a que no se precipita nitruro de cromo, se mejora la resistencia a la corrosión. Lo mismo ocurre en la parte de alta temperatura de la zona afectada por el calor. De esta manera, se puede concluir que UNSS32205 con mayor contenido de nitrógeno en la Figura 3 es significativamente mejor que UNS S31803 con menor contenido de nitrógeno en la Figura 2.
La composición límite de la aleación 2550 | ||||||||||
UNS | Rango de composición química / % (máximo) | |||||||||
C | Minnesota | P | S | Si | Cr | Ni | Mes | norte | Cu | |
S32550 | 0.040 | 1.500 | 0.035 | 0.030 | 1.000 | 24.0~27.0 | 4.5~6.5 | 2.9~3.9 | 0.10~0.25 | 1.50~2.50 |
S32520 | 0.030 | 1.500 | 0.030 | 0.020 | 0.800 | 24.0~26.0 | 5.5~8.0 | 3.0~4.0 | 0.20~0.35 | 0.50~2.00 |
Tabla 2
Está claro que UNS S31803 no es adecuado como metal base para su uso en el estado posterior a la soldadura, y se debe usar UNS S32205. Entre los aceros inoxidables dúplex, UNS S31803 no es el único metal base inadecuado para soldar estructuras. Lo mismo ocurre con la aleación 255, que es un componente de UNS S32550. La Tabla 2 compara la composición de UNSS32550 y UNSS32520 utilizados para el revestimiento. La composición es generalmente la misma. Sin embargo, el contenido mínimo de nitrógeno de UNS S32520 es más alto que el de UNS S32550. Obviamente, UNS S32520 es más adecuado para aplicaciones posteriores a la soldadura. Además, también se puede utilizar UNSS32550, pero el contenido de nitrógeno de la composición del acero debe controlarse hasta el límite superior.
Aporte de calor de soldadura irrazonable
La visión tradicional de la entrada de calor de soldadura es que cuando se suelda acero inoxidable dúplex con contenido de cromo 22%, la entrada de calor debe limitarse a 0.5 ~ 2.5kJ / mm, y cuando se suelda acero inoxidable súper dúplex con contenido de cromo 25%, la entrada de calor debe ser limitado a 0,5 ~ 1,5 kJ / mm.
Cuando se utiliza un aporte de calor más bajo, incluso para aceros dúplex con alto contenido de nitrógeno, la austenita se enfría a una velocidad muy rápida. La formación también es insuficiente. Cuando se utiliza una entrada de calor más alta (> 1,5 kJ), en condiciones de enfriamiento lento, hay una tendencia a que los compuestos intermetálicos se precipiten en la ferrita. En comparación con el acero inoxidable dúplex 22% Cr, la tendencia del acero inoxidable súper dúplex 25% Cr es más obvia.
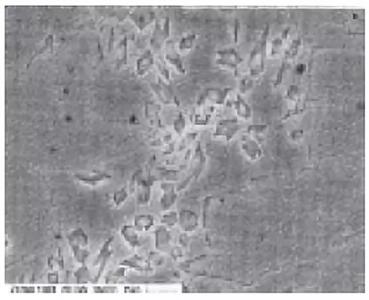
La Figura 4 muestra la microestructura del metal de soldadura cerca del espesor medio de la muestra. Hay una gran cantidad de precipitados angulares solo en la ferrita. Sin embargo, no se determinó exactamente cuál era el precipitado. Nuestra conclusión es que los precipitados se generaron por calentamiento repetido durante doce pasadas de la muestra de prueba.
La operación normal al soldar aceros inoxidables dúplex, especialmente tubos de acero inoxidable súper dúplex, es que la entrada de calor en el cordón de la raíz es mayor que el filete original. El uso de cordón de raíz con un grosor de aproximadamente 6 mm es bastante bueno.
Tratamiento térmico posterior a la soldadura irrazonable
Si las piezas de fundición soldadas o los cabezales soldados requieren un tratamiento térmico posterior a la soldadura, entonces el uso de metales de relleno ricos en níquel de uso común, junto con el uso de temperaturas de recocido irrazonables que cumplen con las especificaciones básicas del metal, hará que los fabricantes de procesamiento de acero inoxidable dúplex cometan otro error. (para acero inoxidable dúplex, el contenido de níquel suele ser 9%, otros son similares a los metales de relleno).
El requisito general es recocer a una temperatura mínima de 1040 ° C y luego enfriar con agua a partir de la temperatura de recocido. Porque la gente no sabe que la fase σ casi siempre se forma en el acero inoxidable dúplex durante el calentamiento a la temperatura de recocido, y cuanto mayor sea el contenido de níquel, aumentará la temperatura de la fase de solución sólida de la fase σ. En este caso, el metal de soldadura rico en níquel es peligroso.
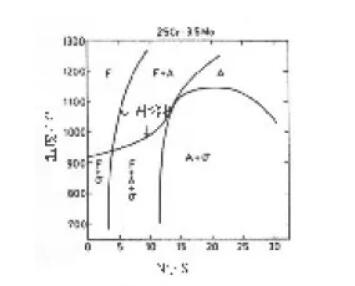
La Figura 5 hecha por Grobner muestra el efecto del níquel sobre la temperatura de la fase de solución sólida de la fase σ de la aleación de Mo 25% Cr-3.5%.
Aunque la aleación utilizada para dibujar este diagrama no contiene elementos de aleación como manganeso, silicio y nitrógeno, es conveniente que las personas comprendan el efecto del níquel en la naturaleza. Muestra claramente que la temperatura de la fase de solución sólida de la fase σ aumenta al aumentar el contenido de níquel. En particular, la temperatura de la línea de fase de la solución sólida de la fase σ del metal de soldadura que contiene 9% Ni será al menos 50 ° C más alta que la temperatura de la línea de la fase de la solución sólida de la fase σ del metal base combinado que contiene 5% Ni.
Conclusión
La práctica ha demostrado que el acero inoxidable dúplex, incluido el acero inoxidable súper dúplex, tiene un buen rendimiento de soldadura y es un material de ingeniería muy importante.
Sin embargo, debido al descuido y la ignorancia, se pueden cometer algunos errores. Para que la zona afectada por el calor y el metal de soldadura tengan un buen rendimiento, es apropiado utilizar un metal base con un alto contenido de nitrógeno de al menos 0,14% de nitrógeno. De lo contrario, se precipitará una gran cantidad de ferrita y nitruro de cromo en la zona afectada por el calor, lo que dañará la resistencia a la corrosión y las propiedades mecánicas.
Para evitar la precipitación de acero inoxidable superdúplex en el área de calentamiento repetido, se debe evitar el uso de una gran cantidad de entrada de calor baja y perlas pequeñas. Y al soldar tuberías de acero inoxidable dúplex y acero inoxidable súper dúplex, para evitar la precipitación en la superficie interna de la tubería, el cordón de la raíz debe usar una entrada de calor más alta (mayor que 1kJ / mm), que es mayor que la entrada de calor del primeras soldaduras continuas.
El recocido posterior a la soldadura del acero inoxidable dúplex soldado debe tener en cuenta el hecho de que la temperatura de la fase σ del metal de soldadura que disuelve el metal de soldadura rico en níquel es más alta que la del metal base.