El acero inoxidable súper austenítico es actualmente el material más adecuado para el proceso de desulfuración de gases de combustión en húmedo.
Este proceso también es el más utilizado con acero inoxidable súper austenítico en el mundo actual. De las muchas tecnologías de desulfuración, representa el 80% de la capacidad total instalada de desulfuración. Siempre está por encima de un rango constante.
La desulfuración de gases de combustión húmeda de piedra caliza-yeso es el proceso de desulfuración más comúnmente utilizado en la desulfuración de gases de combustión húmedos.
El ambiente corrosivo dentro del sistema de desulfuración de gases de combustión húmeda es duro y el equipo interno del sistema se corroe fácilmente. Hacer un buen trabajo de anticorrosión es una medida importante para garantizar el funcionamiento seguro y estable de la fábrica y controlar la planta de energía para evitar emisiones.
El acero inoxidable súper austenítico es rico en una gran cantidad de Cr, Ni, Mo y cantidades adecuadas de elementos de aleación como N y Cu, resistente al ácido sulfúrico diluido y a la corrosión por picaduras, la resistencia a la corrosión por grietas es equivalente a las aleaciones a base de níquel, tiene una excelente propiedades mecánicas y rendimiento de resistencia a la corrosión. Entre ellos, el Mo puede mejorar la resistencia a la corrosión general del acero inoxidable súper austenítico, especialmente la resistencia a la corrosión por picadura de iones de cloruro. El acero inoxidable súper austenítico 6% Mo tiene una mejor resistencia a la corrosión en soluciones ácidas que contienen iones de cloruro y es más adecuado para su aplicación en el sistema de desulfuración de gases de combustión.
Flujo de proceso del sistema de proceso de desulfuración de gases de combustión húmedos
El principal proceso tecnológico básico de la desulfuración húmeda de gas de combustión de piedra caliza-yeso es: después de que el gas de combustión de la caldera es desempolvado por un precipitador eléctrico y reforzado por un ventilador de refuerzo, y luego enfriado por un intercambiador de calor de gases de combustión, ingresa a la torre de absorción. La lechada de piedra caliza se rocía en la torre de absorción para que reaccione con el gas de combustión para eliminar SO2, SO3, HCl y HF en el gas de combustión. La lechada de piedra caliza se transfiere a la capa de pulverización a través de la bomba de circulación de la lechada y luego se atomiza a través de la boquilla, de modo que la lechada y el gas de combustión puedan entrar en contacto y reaccionar completamente. El gas de combustión desulfurado se calienta a través del intercambiador de calor de gases de combustión para aumentar su difusividad y finalmente se descarga en la chimenea, que se descarga a la atmósfera.
En la torre de absorción, la compleja reacción química entre la lechada de piedra caliza y el dióxido de azufre en el gas de combustión produce yeso. Esta parte de la lechada de yeso pasa a través de la bomba de descarga de la torre de absorción y entra al sistema de deshidratación de yeso. El sistema de deshidratación incluye principalmente un ciclón de yeso, un deshidratador de banda de vacío y un distribuidor de lodo. La corriente de gas de combustión después de la reacción se desempaña mediante un dispositivo de desempañado para eliminar las gotas de niebla de la suspensión en el gas de combustión. Al mismo tiempo, el agua de proceso de la planta de energía debe usarse para enjuagar el desempañador de vez en cuando. Hay dos propósitos principales para lavar el desempañador, uno es evitar que el desempañador se obstruya y el otro es usar el agua de lavado como agua suplementaria para estabilizar el nivel de líquido de la torre de absorción.
A la salida de la torre de absorción, el gas de combustión generalmente se enfría a aproximadamente 50 ° C y contiene una gran cantidad de vapor de agua saturado. Después de pasar por el intercambiador de calor de los gases de combustión, los gases de combustión se calientan por encima de 80 ℃, principalmente para mejorar la altura de elevación y la capacidad de difusión de los gases de combustión, eliminando así el fenómeno de la lluvia de yeso. Finalmente, el gas de combustión limpio que cumple con los estándares de emisión de gases de combustión de la central eléctrica se descarga a la atmósfera a través de la chimenea.
Aplicación de acero inoxidable súper austenítico en el sistema de proceso de desulfuración de gases de combustión húmedos
En algunas centrales eléctricas, el gas de combustión de carbón pasa a través de la torre de absorción y se descarga directamente en la chimenea sin un calentador de gas de combustión (WGGH). Este tipo de chimenea se convierte en una chimenea húmeda. Algunas centrales eléctricas no instalan un calentador de gases de combustión después de la torre de absorción, sino un colector de polvo eléctrico húmedo (WESP). El gas de combustión pasa a través del colector de polvo eléctrico húmedo y se descarga a través de la chimenea. Puede verse que el entorno corrosivo de la chimenea húmeda, el precipitador electrostático húmedo y el calentador de gases de combustión es equivalente.
Las chimeneas húmedas están revestidas con materiales metálicos anticorrosión que incluyen acero inoxidable súper austenítico, aleaciones a base de níquel, placas compuestas de acero de titanio, etc.
- Las aleaciones a base de níquel tienen una buena resistencia a la corrosión. La aleación Nicrofer 5923 h Mo-59, la aleación Nicrofer 3127h Mo-31, la aleación Cronifer 1925 h Mo-926, etc., son típicas.
- El titanio tiene buena resistencia, su rendimiento de soldadura es pobre y su resistencia es baja.
- El precio del acero inoxidable súper austenítico es mucho más bajo que el de las aleaciones a base de níquel. Tiene un excelente rendimiento de soldadura y se puede soldar directamente con acero al carbono. Tiene excelentes propiedades mecánicas y rendimiento de procesamiento, y es un material más adecuado.
254SMo es un tipo de acero 6Mo de uso común. Tiene una excelente resistencia a la corrosión por picaduras. Es ampliamente utilizado en equipos de procesamiento industrial ricos en iones halógenos como el agua de mar. Puede usarse para reemplazar materiales costosos como aleaciones a base de níquel o titanio. También hay algunas aplicaciones en sistemas de desulfuración de gases de combustión.
Este artículo toma 254SMo como ejemplo para estudiar la resistencia a la corrosión del acero inoxidable súper austenítico 6Mo en chimeneas húmedas y calentadores de gases de combustión.
Prueba de curva de polarización
preparación de la muestra
Los materiales de prueba son 316L, 317L y 254SMo, y sus componentes principales se muestran en la Tabla 1.

Los tubos de acero inoxidable de los tres materiales se cortaron mecánicamente para hacer muestras de 20 mm x 5 mm x 0,7 mm de tamaño. Las muestras se pulieron con papel de lija 01# alrededor de las muestras.
Después de la limpieza ultrasónica durante 15 minutos y la pasivación con ácido nítrico concentrado durante 30 minutos, la parte trasera se soldó con alambres de cobre y luego la acetona limpia la grasa adherida a la superficie del electrodo, y finalmente la superficie que no funciona se encapsula con resina epoxi, la superficie de trabajo es de 20 mm. × 5 mm.
Los electrodos empaquetados se lijan con diferentes asperezas, de grueso a fino, y luego se pulen con papel de lija 01# para su uso.
Método de prueba
La prueba utiliza un sistema de tres electrodos. El electrodo de trabajo es un electrodo plano de fabricación propia del material medido, el electrodo de referencia es un electrodo de calomelanos saturado (SCE) y el electrodo auxiliar es un electrodo de platino. La velocidad de exploración potencial es de 1 mV / sy la frecuencia de exploración es de 2 Hz. El medio de prueba es condensado de gas de combustión (pH = 1,84), y luego se agrega NaCl al condensado de gas de combustión para preparar 1000 mg / L y 40000 mg / L de dos soluciones de medio de prueba de concentración de Cl diferentes, y las otras concentraciones de iones permanecen sin cambios. .
La temperatura de prueba se selecciona para que sea de 50 ℃ y la precisión del control de temperatura es de 0,1 ℃. El potencial de picadura del material se probó mediante el método de exploración de potencial dinámico, y la prueba se inició desde -400 mV con respecto al electrodo de referencia hasta que la corriente del ánodo alcanzó 0,2 ~ 1,0 mA / cm2.
Cada material se prueba tres veces en las mismas condiciones de trabajo para garantizar que los resultados de la prueba sean verdaderos y confiables.
Resultados de la prueba
La Figura 1 muestra las curvas de polarización de acero inoxidable 316L y acero inoxidable 317L en condensado de gas de combustión de 1000 mg / LCl y acero inoxidable súper austenítico 254SMo en condensado de gas de combustión de 40000 mg / LCl.
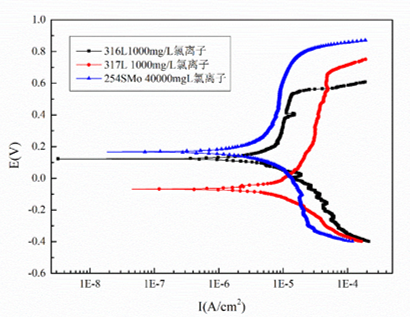
Se puede ver que el potencial de picaduras de 316L es menor que el de 317L cuando la concentración de Cl es 1000 mg / L en el condensado de gas de combustión.
El potencial de picadura del acero inoxidable generalmente disminuye con el aumento de la concentración de Cl en el medio de solución. Sin embargo, cuando la concentración de Cl en el condensado de los gases de combustión alcanza 40.000, el potencial de picaduras de 254SMo sigue siendo muy alto y se encuentra en un estado sobrepasivado. Puede verse que el 254SMo tiene una mejor resistencia a la corrosión por picaduras en el condensado de los gases de combustión con una mayor concentración de Cl.
El contenido de elementos de aleación como Cr y Mo en 254SMo es relativamente alto. Entre ellos, el Cr es el elemento principal para formar la película de pasivación. El aumento del contenido de Cr puede hacer que la película de pasivación sea más estable; y el mayor contenido de Mo puede hacer que la superficie del acero tenga. Se forma una película protectora de MoOCl2 en el medio donde está presente Cl-, evitando así que el Cl- penetre en la película de pasivación.
La magnitud de la corriente roma dimensional en la curva de polarización puede caracterizar el índice de corrosión uniforme del acero inoxidable. Según la ley de Faraday, existe una estricta relación cuantitativa entre el índice de corriente de corrosión y el índice de peso. Cuanto mayor sea la corriente de corrosión, más rápida será la velocidad de corrosión del metal, lo que representa la resistencia del material. Cuanto peor sea el rendimiento de la corrosión uniforme. Explique el rendimiento de la resistencia a la corrosión uniforme 254SMo>316L>317L.
Pruebas in situ
Las tasas de corrosión de los tres materiales de acero inoxidable se muestran en la Figura 2. Como se puede ver en la figura, la tasa de corrosión de 317L es ligeramente más alta que la de 316L, respectivamente 0.081μm / ay 0.069μm / a, que es la Igual que los resultados de la prueba de la curva de polarización Es consistente.
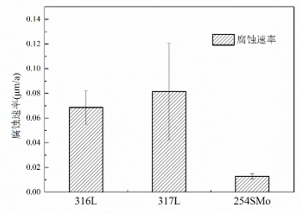
La tasa de corrosión de 254SMo es mucho menor que las dos anteriores, que es de 0.013μm por año. Debido a la existencia de errores de pesaje, la corrosión del 254SMo es casi insignificante. Puede verse que el 254SMo tiene una mejor resistencia a la corrosión uniforme en las condiciones de funcionamiento reales.
Resumen
- 1) El acero inoxidable súper austenítico tiene buena resistencia a la corrosión por picaduras de Cl en solución ácida, y su precio es más bajo que el de la aleación a base de níquel, que es más adecuada para su aplicación en sistemas de gases de combustión de desulfuración húmeda;
- 2) La prueba de la curva de gradiente y la prueba en el sitio muestran que el 254SMo tiene una excelente resistencia a la corrosión en el condensado de los gases de combustión y puede cumplir con las condiciones de trabajo de equipos tales como chimeneas húmedas y calentadores de gases de combustión;
- 3) El acero inoxidable súper austenítico 904L y AL-6XN se pueden usar bien en torres de absorción de desulfuración, y es una buena dirección de selección de material para que las torres de absorción reemplacen materiales no metálicos con materiales de aleación.