Los grados austeníticos son aquellas aleaciones comúnmente utilizadas en aplicaciones de acero inoxidable. El acero inoxidable austenítico no es magnético. La aleación austenítica más común es el acero de hierro-cromo-níquel, ampliamente conocido como la serie 300.
Debido al alto contenido de cromo y níquel, los tubos de acero inoxidable austenítico son los más resistentes a la corrosión en el grupo de los aceros inoxidables, proporcionando propiedades mecánicas excepcionalmente buenas. No pueden endurecerse mediante tratamiento térmico, pero pueden endurecerse significativamente mediante trabajo en frío.
Grado recto
Los grados rectos de tubos de acero inoxidable austenítico contienen hasta 0.08% de carbono. Existe la idea errónea de que el acero de grado puro contiene al menos 0.035% de carbono, pero la especificación no lo requiere. Siempre que el material cumpla con los requisitos físicos de grado puro, no existe un requisito mínimo de carbono.
"Grado "L
El grado "L" se utiliza para proporcionar una resistencia adicional a la corrosión después de la soldadura. La letra "L" después del tubería de acero inoxidable tipo indica bajo carbono (por ejemplo, 304L). Mantenga el carbono a 0,035% o menos para evitar la precipitación de carburos. El carbono en el acero se precipitará cuando se caliente a una temperatura crítica de 800°F a 1600°F, se combinará con el cromo y se acumulará en los límites del grano. Esto elimina el cromo de la solución del acero y favorece la corrosión cerca de los límites del grano. Al controlar la cantidad de carbono, esto se minimiza. Para la soldabilidad, utilice el grado "L". Quizá se pregunte por qué no todos los aceros inoxidables son de grado L.
Hay dos razones:
El grado "L" es más caro;
El carbono tiene una alta resistencia física a altas temperaturas;
Cuanto mayor sea el contenido de carbono, mayor será el límite elástico.
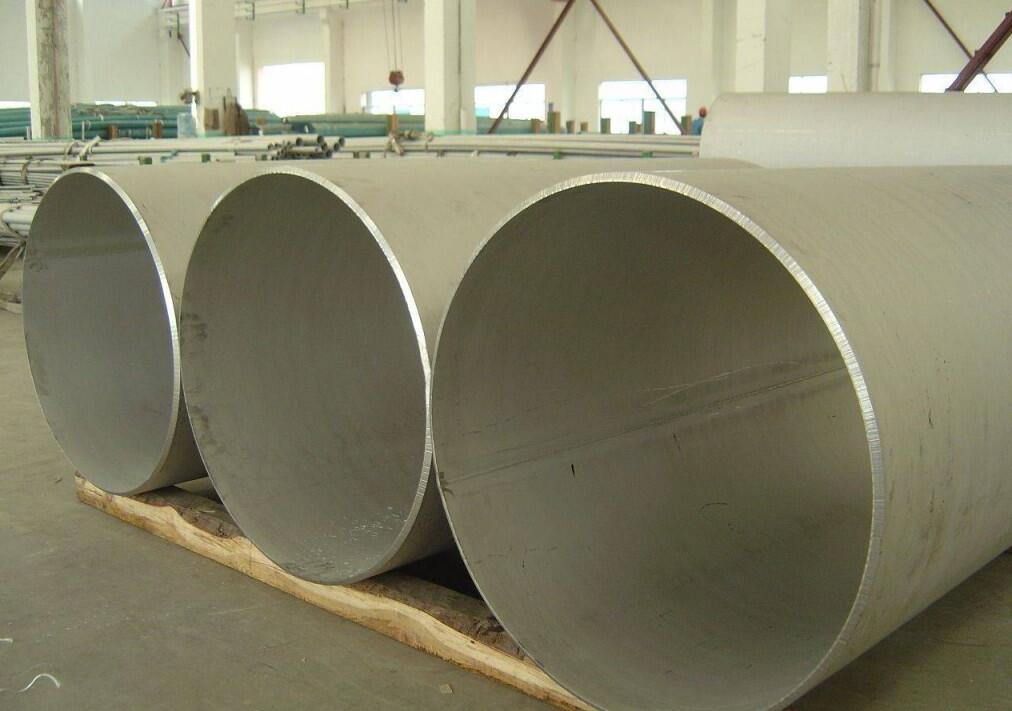
Los trenes de laminación suelen comprar materias primas de grado "L", pero especifican las propiedades físicas de los grados rectos para mantener la resistencia de los mismos. La torta también se calienta. De este modo, el material ha obtenido la doble certificación 304/304L; 316/316L y otros grados "H
los "Grado "H El contenido de carbono es de al menos 0,04% y el contenido máximo de carbono es de 0,10%, que se indica con la letra "H" después de la aleación. La gente requiere principalmente el grado "H", porque el material se utilizará a temperaturas extremas, ya que el mayor contenido de carbono ayuda al material a mantener la resistencia a temperaturas extremas.
Es posible que escuche el término "recocido por disolución". Esto significa que sólo los carburos que pueden haber precipitado (o desplazado) el límite del grano se vuelven a disolver (dispersar) en la matriz metálica mediante el proceso de recocido. Si no es posible el recocido después de la soldadura, se utiliza el grado "L", por ejemplo en el campo de la soldadura de tuberías y accesorios.
Tipo 304 | El más común de los grados austeníticos, que contiene aproximadamente cromo 18% y níquel 8%. Se utiliza para equipos de procesamiento químico, para las industrias de alimentos, lácteos y bebidas, para intercambiadores de calor y para los productos químicos más suaves. |
Tipo 316 | Contiene cromo de 16% a 18% y níquel de 11% a 14%. También tiene molibdeno agregado al níquel y cromo del 304. El molibdeno se usa para controlar el ataque tipo pozo. El tipo 316 se utiliza en el procesamiento químico, la industria de la pulpa y el papel, para el procesamiento y dispensación de alimentos y bebidas y en los entornos más corrosivos. El molibdeno debe tener un mínimo de 2%. |
Tipo 317 | Contiene un porcentaje de molibdeno superior al 316 para entornos altamente corrosivos. Debe tener un mínimo de 3% “moly”. A menudo se utiliza en pilas que contienen depuradores. |
Escribe 317L | Restringe el contenido máximo de carbono a 0.030% máx. y silicio a 0,75% máx. para mayor resistencia a la corrosión. |
Tipo 317LM | Requiere un contenido de molibdeno de 4.00% min. |
Tipo 317LMN | Requiere un contenido de molibdeno de 4.00% min. y nitrógeno de .15% min. |
Escribe 321 Escribe 347 | Estos tipos se han desarrollado para resistir a la corrosión por exposición intermitente repetida a temperaturas superiores a 800 grados F. El tipo 321 se fabrica mediante la adición de titanio y el tipo 347 se fabrica mediante la adición de tantalio / columbio. Estos grados se utilizan principalmente en la industria aeronáutica. |