Welding coefficient in the order
Welding coefficient in the order.In the inquiry orders for stainless steel welded pipes, words such as “Ej=1.0” or “Ej=0.85” are often seen. What do they represent? I have summarized the information briefly.
Ej is commonly referred to as the “welding joint coefficient”, also commonly referred to as the weld joint coefficient. In fact, the welding joint coefficient is a concept in pressure vessel products. In typical pressure vessels, welding joints are generally classified into four categories based on their position: A, B, C, and D. To simplify, A represents the longitudinal weld seam on the shell and head, B represents the circumferential butt weld seam on the shell, C represents the circumferential butt weld seam connected to the flange, and D represents the weld seam between the connecting pipe and the shell. A typical schematic diagram is as follows:
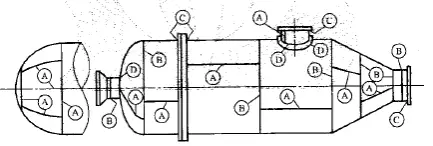
Classification standards for welded joints
The classification standards and instructions for welded joints are detailed in clause 4.5.1 of GB150.1-2011 Pressure Vessels, while clause 4.5.2 specifies the coefficient of welded joints. The first sentence clearly states that “the coefficient of welded joints should be determined based on the weld form and non-destructive testing length ratio of the butt joint.” From this sentence, we can see that “the weld form and non-destructive testing length ratio of the butt joint” determine the “welding joint coefficient”, which is a very important logical relationship. Let’s take a look at how ASME regulates the coefficient of welded joints. In the opening of UW-12 in Volume 8, Part 1 of ASME VIII. 1-2019 Rules for Construction of Pressure Vessels Division 1, it is also mentioned that “a joint efficiency depends only on the type of joint and on the context of examination of the joint and does not depend on the extent of examination of any other joint.” The logic is consistent with the provisions of GB150.1.
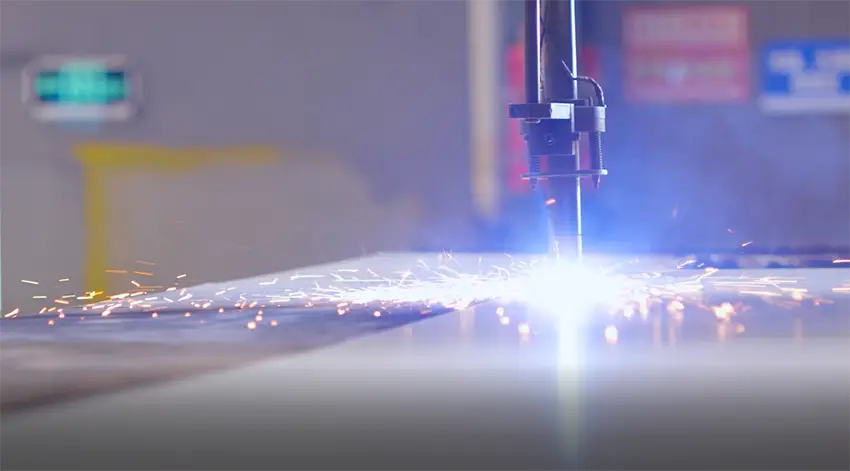
The role played by welded joints
The role of welded joints in structures is mainly determined by their position, and the stress state of welds at different positions varies. Therefore, position becomes the primary factor to consider the role of welded joints. Whether a welded joint can play its due role is determined by the quality of the welded joint, and the process of achieving welding quality will be influenced by congenital factors such as “difficulty in process implementation”. At the same time, it is also necessary to consider the acquired factors that “quality indicators contradict economic indicators”. Of course, all of this is based on safety as the bottom line. Therefore, in structural design, adopting different welding joint coefficients is a common result of integrating and balancing various factors, and it has significant practical significance.
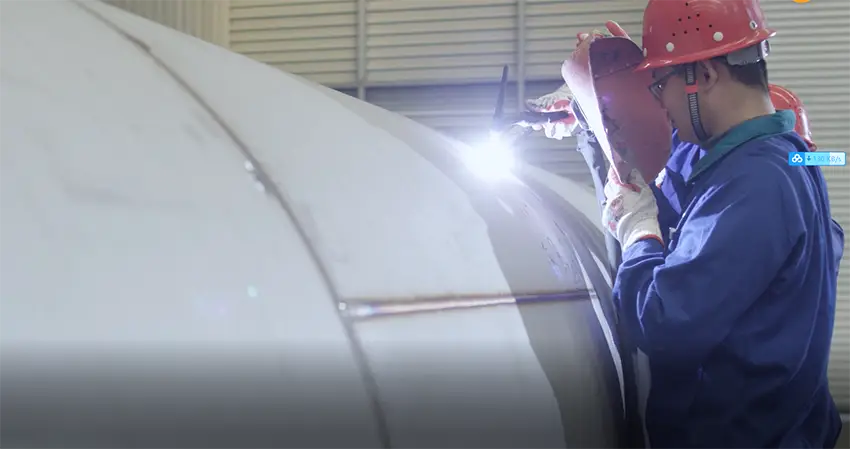
Furthermore, although different welding joint coefficients correspond to different testing ratios in form, they fundamentally correspond to different quality levels. Generally speaking, the qualification level of 100% non-destructive testing welds is level II, while the qualification level of 20% non-destructive testing welds is level III. Different qualification levels result in different allowable sizes and quantities of defects.