Definition of Nickel based alloys
Alloys with Ni content exceeding 30wt% are called nickel based alloys. Common products have Ni content exceeding 50wt%. Due to their superior high-temperature mechanical strength and corrosion resistance, they are combined with iron-based and cobalt-based alloys as superalloys ( Superalloy).
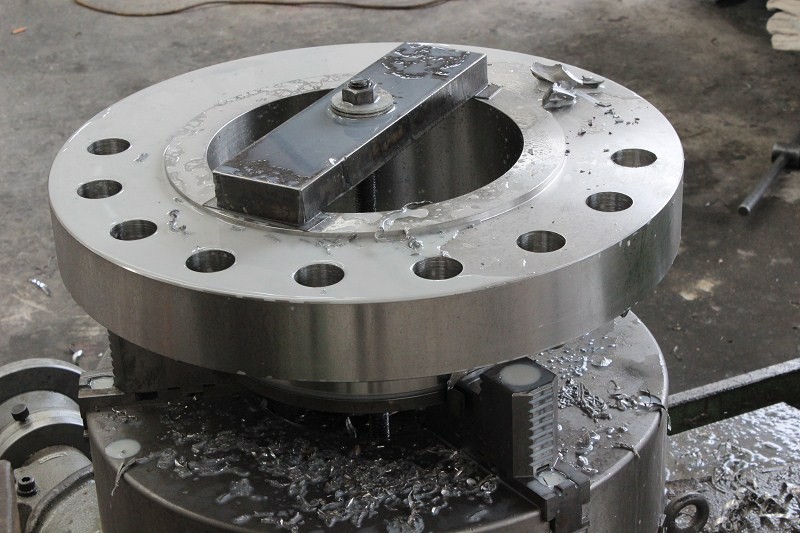
This kind of alloy is generally used in a high temperature environment above 540℃, and different alloys are selected according to the application. It is mostly used in special corrosion-resistant environments, high-temperature corrosion environments, and equipment requiring high-temperature mechanical strength.
It is often used in aerospace, energy, petrochemical industry or special electronics/optoelectronics fields.
Application fields | Requirements characteristics | Product Usage |
Aerospace | Maintain good mechanical strength at extremely high temperatures | Aircraft engines, gas turbines, engine valves |
Energy | Good resistance to high temperature vulcanization and high temperature oxidation | Furnace parts, insulation, heat treatment industry, oil and gas industry |
Petrochemical | Resistant to aqueous solution (acid, alkali, chloride ion) corrosion | Desalination plant, petrochemical pipeline |
Electronics | General environment with low corrosion resistance or high temperature resistance | Battery shell parts, lead frame, computer monitor net cover |
Origin and development
The nickel-based alloy was developed in the late 1930s. The nickel-based alloy Nimonic 75 (Ni-20Cr-0.4Ti) was first produced in the United Kingdom in 1941. In order to increase the creep strength, Al was added to develop Nimonic 80 (Ni-20Cr- 2.5 Ti-1.3Al); while the United States in the mid-1940s, Russia in the late 1940s, China in the mid-1950s also developed nickel-based alloys.
The development of nickel-based alloys includes two aspects, namely the improvement of alloy composition and the innovation of production technology.
For example, in the early 1950s, the development of vacuum melting technology created conditions for the refining of nickel-based alloys containing high Al and Ti, and drove a substantial increase in alloy strength and service temperature. In the late 1950s, due to the increase in the working temperature of turbine blades, alloys were required to have higher high-temperature strength. However, when the strength of the alloy was high, it was difficult or even impossible to deform. Therefore, precision casting technology was used to develop a series of high-temperature strengths. Of casting alloys. In the mid-1960s, better performance directional crystalline and single crystal superalloys and powder metallurgy superalloys were developed.
In order to meet the needs of ships and industrial gas turbines, a number of high-Cr nickel-based alloys with good thermal corrosion resistance and stable structure have been developed since the 1960s. In about 40 years from the early 1940s to the late 1970s, the working temperature of nickel-based alloys increased from 700 by 1,100°C, an average annual increase of about 10°C. Today, the service temperature of nickel-based alloys can exceed 1,100℃. From the aforementioned Nimonic75 alloy with a simple composition to the recently developed MA6000 alloy, the tensile strength at 1,100℃ can reach 2,220MPa and the yield strength is 192MPa; Its durability under 1,100℃/137MPa conditions is about 1,000 hours, and it can be used for aero engine blades.
Features of nickel-based alloys
Nickel-based alloys are the most widely used and strongest materials in superalloys. The name of the super alloy is derived from the material characteristics.
- (1) Excellent performance: It can maintain high strength at high temperature, and has excellent creep resistance, fatigue resistance and other mechanical properties, as well as oxidation and corrosion resistance, and good plasticity and weldability.
- (2) Alloy addition is super complicated: Ni-based alloys often add more than ten alloying elements to improve the corrosion resistance of different environments; and solid solution strengthening or precipitation strengthening.
- (3) The working environment is extremely harsh: Nickel-based alloys are widely used in various harsh operating conditions, such as high temperature and high pressure parts of aerospace flight engine gas chambers, structural parts for nuclear energy, petroleum, marine industries, and corrosion-resistant pipelines.
The effect of various elements on
Metallic nickel retains austenite and a face-centered cubic structure until it reaches its melting point. This provides a degree of freedom for the ductile-brittle transition, and also greatly reduces the manufacturing problems caused by the coexistence of other metals. In the electrochemical sequence, nickel is inert than iron and more active than copper. Therefore, in a reducing environment, nickel is more resistant to corrosion than iron, but not copper. On the basis of nickel and chromium, the alloy has oxidation resistance, which can produce many kinds of alloys with a very wide range of applications, so that they can have the best resistance to reducing and oxidizing environments .
Compared with stainless steel and other iron-based alloys, nickel-based alloys can hold more alloying elements in a solid solution state, and can maintain good metallurgical stability. These factors allow the addition of a variety of alloying elements, so that a large number of nickel-based alloys can be used in various corrosive environments.
The common elements in nickel-based alloys mainly include:
Nickel:
Provide metallurgical stability, improve thermal stability and weldability, improve corrosion resistance to reducing acids and caustic soda, and improve stress corrosion cracking resistance, especially in chloride and caustic soda environments.
Chromium:
Improve anti-oxidation and high-temperature anti-oxidation, anti-sulfur properties, and improve anti-pitting and crevice corrosion properties.
Molybdenum:
Improve the corrosion resistance to reducing acids, improve the resistance to pitting and crevice corrosion in the chloride-containing aqueous solution environment, and improve the high temperature strength.
Iron:
Improve resistance to high temperature carburizing environment, reduce alloy cost, and control thermal expansion.
Copper:
Improve the corrosion resistance to reducing acids (especially those sulfuric acid and hydrofluoric acid used in places where the air is not circulating) and salts. The addition of copper to the nickel-chromium-molybdenum-iron alloy helps to improve the resistance to hydrofluoric acid, Corrosion resistance of phosphoric acid and sulfuric acid.
Aluminum:
Improve high temperature oxidation resistance and age hardening.
Titanium:
Combined with carbon, it reduces intergranular corrosion caused by chromium carbide precipitation during heat treatment and improves aging strengthening.
Niobium:
Combined with carbon, it reduces intergranular corrosion caused by chromium carbide precipitation during heat treatment, improves pitting and crevice corrosion resistance, and improves high-temperature strength.
Tungsten:
Improve the resistance to reducing acid and local corrosion, improve strength and weldability.
Nitrogen:
Improve metallurgical stability, improve pitting and crevice corrosion resistance, and increase strength.
Cobalt:
Provides enhanced high temperature strength, improved resistance to carbonation and vulcanization.
Many of these alloying elements can combine with nickel in a wide range of compositions to form a single-phase solid solution, ensuring that the alloy has good corrosion resistance under many corrosive conditions. The alloy also has good mechanical properties in a fully annealed state, without worrying about harmful metallurgical changes caused by manufacturing or thermal processing. Many high nickel alloys can increase their strength through solid solution hardening, carbide precipitation, precipitation (ageing) hardening, and dispersion strengthening.
Posted by stainless steel pipe fittings kaysuns