Nickel-Rich Austenitic Stainless Steel. The “Achilles heel” of austenitic stainless steel is prone to stress corrosion cracking (SCC). But when the nickel content exceeds 20%, the stress corrosion resistance is greatly improved (Figure 1).
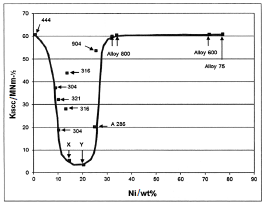
Nickel-rich austenitic stainless steel (NiASS) can be considered as a separate type of stainless steel. In fact, when the nickel content of austenitic stainless steel exceeds 30%, its stress corrosion resistance is comparable to that of duplex stainless steel and ferritic stainless steel.
Figure 1, the Copson curve shows the effect of nickel on the stress-corrosion threshold stress strength in iron-nickel-chromium alloys containing 16% to 21% chromium (105 ° C, 22% aqueous NaCl solution). X and Y are German superalloys, and 444 is an ultra-pure ferritic stainless steel. This figure is redrawn according to Speidel (1981).
Nickel is an expensive alloy element and is only used when necessary for performance. However, in some applications, when both stress corrosion resistance and austenitic structure are required, nickel is also essential.
For example, creep resistance is extremely important in high-temperature environments, where austenitic stainless steel is required. As with traditional austenitic stainless steels, because of its low stacking fault energy (see Figure 2), twin boundaries are a distinctive feature of nickel-rich austenitic stainless steels. Table 1 lists several limited nickel-rich austenitic stainless steel grades.
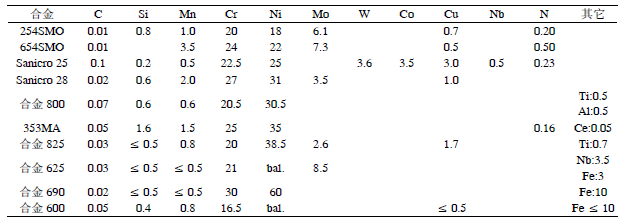
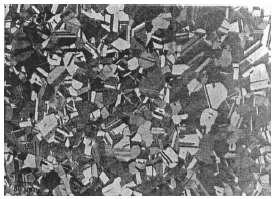
Super austenitic stainless steels 254SMO and 654SMO pipes are specifically designed for the oil and gas industry. Typical applications are equipment such as seawater cooling, pulp bleaching, and hydraulic and instrument piping.
Sanicro 25: A 22Cr-25Ni alloy designed for boilers at 700 ° C and above. Because of its good creep rupture strength and high temperature corrosion resistance, it is a material suitable for super heaters and reheaters.
In fact, Sanicro 25 has better creep rupture strength than most austenitic stainless steels in the range of 600 ~ 750 ℃. In highly corrosive and acidic environments, Sanicro 28 is usually the best choice.
It is used in high-strength drilling with pipelines, casings, and acid gas well linings. Other applications include heaters, pump systems, and pumps and vessels in wet and super phosphoric acid plants.
Multi-purpose alloy 800: commonly used in 550 ~ 1100 ℃ environment, such environments require materials with excellent creep resistance, good high temperature corrosion resistance and high temperature strength. This type of alloy is also used in the import and export of ammonia, methanol and civil gas, and alloy 800 is also a good choice for furnace tubes used in the production of vinyl chloride and ethylene.
Other applications include fluidized combustion bed heat exchange tubes, radiant tubes and heat treatment furnace components, such as muffler tubes and thermocouple protection sleeves.
The 25Cr-35Ni alloy 353MA is designed to be used in environments where there are potential problems with carburization and nitrogen absorption, and is suitable for cracking furnaces and reforming tubes that process synthesis gas. Although there are other alternative materials that contain more chromium, 353MA is optimal. One of the reasons is that it contains Ce element, which helps to form a very stable surface oxide layer.
Alloy 69: 60% nickel, mainly used in the piping of steam generators in nuclear power plants (Figure 3). The operating temperature is 365 ° C. At this temperature, stress corrosion cracking between grains is a potential problem. Under the given conditions, alloy 690 is hardly corroded, so it becomes the alloy of choice.
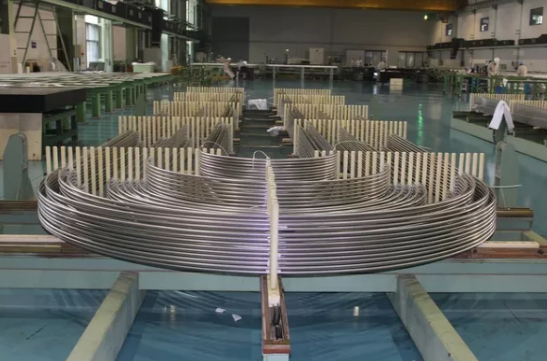
Interestingly, we have noticed that nickel-rich austenitic stainless steel 254SMO is also used in art production.
The “God, our Father, on the Rainbow” designed by Carl Milles was completed in 1995 on the south coast of Stockholm Strand (Figure 4). The sculpture is about 23m high. A large number of seamen pass by here every day. It is a famous attraction. The surrounding seawater contains salts and chlorides are likely to cause external corrosion. If low alloy steel is used to make rainbows, it will rust almost instantly.
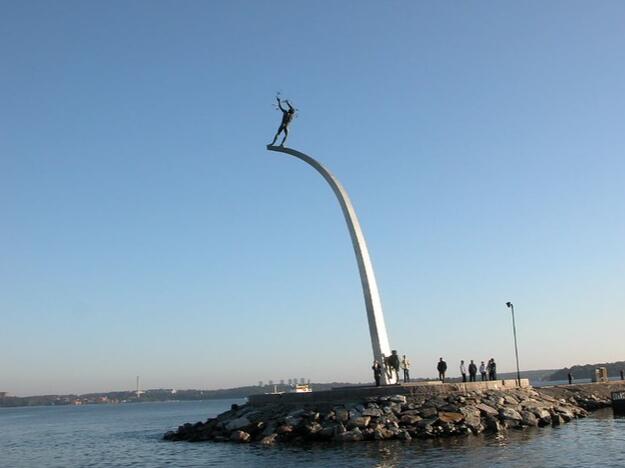