In high-frequency welded pipes, the manifestations of cracks include long cracks, partial periodic cracks, and irregular intermittent cracks.
Some stainless steel welded pipes have no cracks on the surface after welding, but after flattening, straightening or water pressure tests, cracks appear.
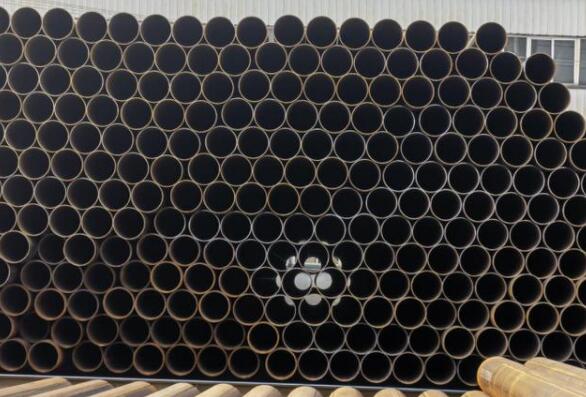
Factors affecting cracks
- Poor quality of raw materials
In the production of welded pipes, there are often problems of large edge burrs and excessive width of the raw material. If the burrs are outward during welding, it is easy to produce continuous and long intermittent cracks. The width of the raw material is too wide and the squeeze roll pass is too full to form a welded peach shape. , The outer welding scar is large, the inner welding rib is small or even not, and it will crack after straightening.
- Edge corner joint state
The fillet joint of the pipe blank edge is a common phenomenon in the production of welded pipe. Improper forming adjustment is a prerequisite for corner joints. Improper pass design of the squeeze roller, large outer round angle of the pass, and elevation angle of the squeeze roll adjustment are the key factors that affect the corner joint.
- Unreasonable selection of process parameters
The process parameters of high-frequency welded pipe production include welding speed, welding temperature, welding current, extrusion force, opening angle, size and placement position of inductors and resistors, etc.
The selection of high frequency power, welding speed, welding extrusion force and the size of the opening angle are more important process parameters, which need to be matched reasonably, otherwise it will affect the welding quality.
In the production of high-frequency welded pipes, there are many factors that cause weld cracking, and the prevention methods are different. There are too many variables in the high-frequency welding process. The defects in any link will affect the quality of the weld.
The above are some common factors given from stainless steel pipe and fittings supplier, KAYSUNS.