Due to its higher corrosion resistance, duplex stainless steel pipes are widely used in petrochemical industries and other industries with harsh media environments. Although duplex steel has good corrosion resistance, leakage in petrochemical industry often occurs due to the corrosion of duplex pipes or other reasons.
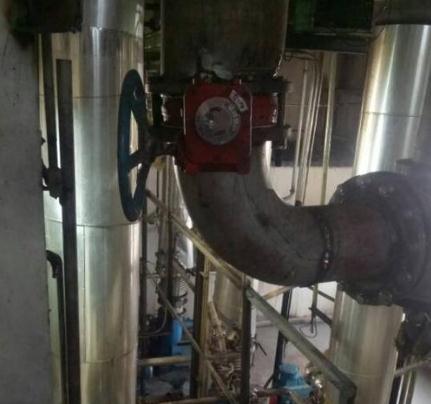
After a short-term operation of the duplex stainless steel gas heat exchanger, leakage in petrochemical industry appeared. We can comprehensively analyze the reasons for the short-term leakage and failure of the heat exchange tube through the detection methods of corrosion morphology, metallography, hardness, etc., combined with the corrosion environment of the heat exchange tube, and provide technical support for subsequent corrosion protection.
Process analysis
The tested heat exchanger tube material is 2205 duplex stainless steel (0Cr22Ni5Mo3N), the medium is oil and gas, and the temperature is 80°C.
Oil and gas contain a large amount of hydrogen sulfide, chloride ion and hydrogen dioxide, which belong to the low-temperature corrosion of hydrogen chloride + hydrogen sulfide + hydrogen dioxide in a complex medium environment. When pH>7, the dominant damage mechanism is acidic water corrosion; when pH<7 The dominant damage mechanism is hydrochloric acid corrosion. In addition, the presence of hydrogen sulfide will cause stress corrosion cracking of carbon steel and low-alloy steel in a wet hydrogen sulfide environment, and the presence of chloride ions will cause chloride stress corrosion cracking of austenitic stainless steel. Due to the process problem of processing oil and gas, the injection of ammonia may also produce ammonium chloride corrosion.
Analysis of the appearance and material performance of the leaked pipe
2.1 Macro morphology
The heat exchanger is a U-shaped tube heat exchanger, the elbow is a smooth tube, which has undergone a solution treatment according to the design requirements, and the straight tube is a spiral tube processed by rolling. The macroscopic characteristics of the tube sheet of the leaking heat exchanger and the intercepted heat exchange tube are as follows:
(1) The number and distribution characteristics of leakage tubes of heat exchanger tubes. The number of leaking tubes on the tube sheet exceeds 30; the locations of leaking tubes are irregularly distributed.
(2) Sampling inspection of the characteristics of the outer surface of the heat exchange tube. The outer surface of the spinning groove of the leaked heat exchange tube has a large number of rolling defects. Although the number of such defects is large but the depth is relatively shallow, it is obviously not the reason for the short-term operation of the heat exchange tube to crack and leak, but It is not ruled out that it will continue to expand during long-term operation of the device.
(3) The corrosion damage characteristics of the inner surface of the heat exchange tube sampled. The inner surface of the tube near the tube sheet has the most pitting corrosion pits. As the distance from the tube sheet increases, the corresponding pitting corrosion is gradually reduced. The shallow depth of the pitting pits on the inner surface of the heat exchange tube should not be the cause of the short-term operation of the heat exchange tube cracking and leaking.
2.2 Metallographic analysis
Observe the local structure of the transverse and longitudinal sections of the pipe section through a metallographic microscope. The matrix structure is composed of ferrite + banded austenite precipitates. The two phases are roughly equivalent in number. The austenite precipitates are striped along the rolling direction of the steel pipe. Distribution between phases.
There is an obvious deformation zone near the spiral groove on the outer surface of the pipe section, and the deformation zone completely surrounds the spiral groove by rolling. In addition, it is found that the bottom of part of the spiral groove has a rolling crack with a length of about 100μm on its side surface, which indicates that the pressure of the spinning process is very large; the existence of the deformation zone of the spinning process indicates that the spiral heat exchange tube has not been processed after the spinning process. Carry out solution stress relief annealing treatment.
2.3 Chemical composition analysis
According to the analysis results, except for the slight difference in nitrogen data, other components meet the 2205 material standard.
2.4 Hardness testing
The hardness detection positions are respectively selected on the inner surface of the bottom of the spiral groove of the spiral heat exchange tube and the inner surface of the tube without processing the spiral groove.
Analysis of inspection results
Based on the above inspection results, it is concluded that the chemical composition and matrix structure (ferrite + banded austenite) of the selected pipe basically meet the requirements of the 2205 duplex steel standard. The main problems are as follows.
(1) There are a lot of micro-crack defects on the inner wall
Through metallographic analysis, it is found that there are a large number of micro-cracks in the parts near the tube head expansion or the parts far away from the tube head. This phenomenon shows that these cracks have formed during the tube rolling process.
(2) There are a lot of processing defects
There is an obvious deformation zone near the spiral groove on the outer surface of the heat exchange tube, and the deformation zone completely surrounds the spiral groove processed by rolling. In addition, there are rolling cracks at the bottom of the spiral grooves of some heat exchange tubes. The existence of cracks in the rolling process indicates that the processing stress is very large; the existence of the rolling process deformation zone indicates that the spiral heat exchange tube has not undergone solution stress relief annealing or insufficient stress relief annealing after processing.
(3) Local pitting damage
After a short period of operation, many but not very deep pits (about 100μm) have been produced on the inner wall of the heat exchange tube. The occurrence of these corrosion pits indicates that the heat exchange tubes of this batch have insufficient pitting resistance to the working medium, which will obviously affect the service life of the heat exchange tubes.
(4) Hardness
The test results show that the hardness of the processed spiral groove is obviously higher than that of the unprocessed area, and the hardness of the heat exchange tube is higher, which will increase the brittleness of the tube and decrease the plastic toughness. It shows that the deformation of the heat exchange tube is too large when the spiral groove is processed, and the stress relief treatment is not performed or the stress relief treatment is insufficient after processing.
Based on the above analysis, the failure of the heat exchange tube head leakage is due to the heat exchanger tube being in a wet hydrogen sulfide corrosive environment, and the martensite phase precipitation, high hardness and stress concentration caused by the expansion and spinning processing will cause Sulfide stress corrosion cracking sensitivity is greatly increased. At the same time, the raw materials of the heat exchange tube do not meet the quality standards, and there are a large number of longitudinal micro-cracks on the inner wall. Although these micro-cracks are short in length, these micro-cracks will rapidly expand and form penetration under the promotion of sulfide stress corrosion during operation. crack.
It is recommended that surface damage should be avoided during rolling processing, and solution treatment of the entire tube should be carried out after processing in avoid the leakage in petrochemical industry.
Posted by stainless steel pipe fittings supplier, KAYSUNS.