What is 904L Stainless Steel?
Alloy 904L is a super austenitic stainless steel designed for a variety of medium requiring high corrosion resistance. This alloy contains high content of chromium and nickel, and with molybdenum and copper as the additional components, its excellent corrosion resistance can be guaranteed.
With the content of 25% nickel and 4.5% molybdenum, alloy 904L is superior to 316L and 317L molybdenum stainless steels in the resistance to chloride stress corrosion cracking, pitting and corrosion.
Initially, alloy 904L is developed for the application of corrosion resistance in dilute sulfuric acid. It also performs well in the resistance to other inorganic acids (such as hot phosphoric acid) and most organic acids.
In practice, alloy 904L is easy to be welded and machined in the shop.
Standard of 904L Stainless Steel
EN Grade: 1.4539
ASTM/ASME Grade:
ASTM SA240 for SS plates
ASTM SB625 for SS plates and sheets
ASTM SB677/SB674 N08904 for pipe and tubes
ASTM SB366 WP904L for wrought fittings
ASTM SB459 N08904 for forged and flanges
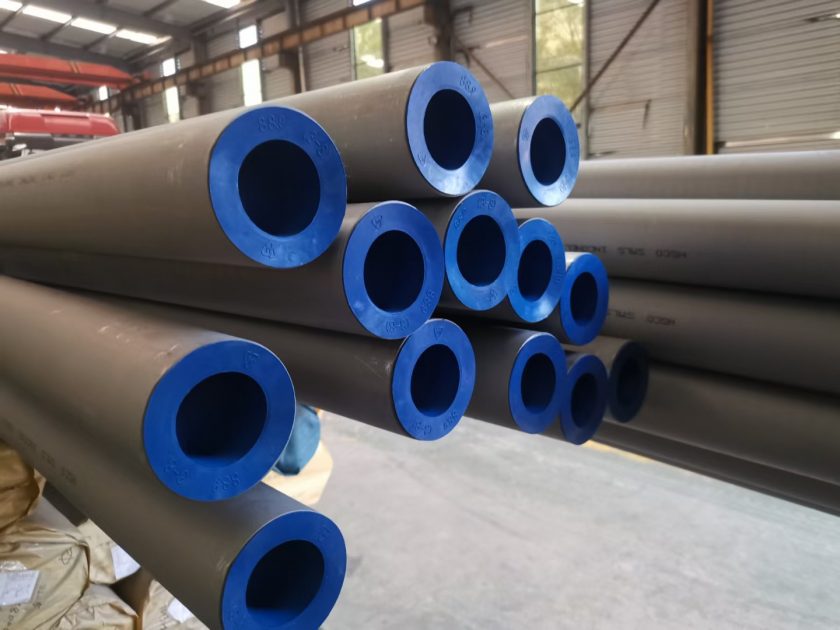
Corrosion Resistance of 904L Stainless Steel
With high content of alloy, 904L alloy performs excellently in uniform corrosion resistance.
Initially, alloy 904L is developed for the application of corrosion resistance in dilute sulfuric acid, and it is one of the few stainless steels that can maintain full corrosion resistance at temperatures up to 95°F (35°C) across the entire concentration range from 0 to 100%. Besides, 904L also has excellent corrosion resistance to many inorganic acids (e.g., phosphoric acid) and most organic acids. However, acid and acid solutions containing halogen ions are very corrosive, and the corrosion resistance of 317L, 317LMN, and 904L may not be able to defend.
Frictional distillate oils usually require the material superior to 316L, and 317Mn is often used. In these hot concentrated alkali solutions, the corrosion resistance of the material is mainly determined by its nickel content. With the nickel content reaching 25%, 904L now has proved to be an excellent alternative to most conventional stainless steels.
For traditional stainless steels such as 304L and 316L, they are susceptible to chloride stress corrosion cracking under certain conditions. The stress corrosion cracking tolerance of chloride will go up with the increase of nickel and molybdenum content. Therefore, for super austenitic stainless steels such as 904L, it has a higher resistance to chloride stress corrosion cracking.
Chemical Analysis (%) of 904L Stainless Steel

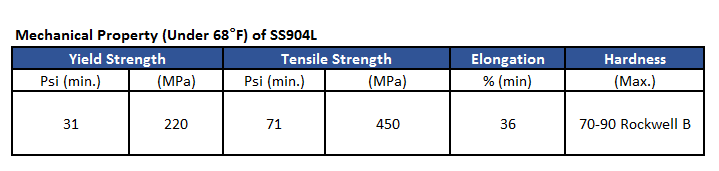
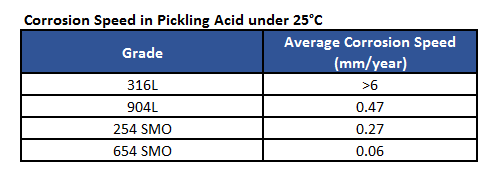
Processing of 904L
Cold Forming
904L is easy to be elongated and shaped. Compared with 304 or 304L, additional content of molybdenum and nitrogen means that it requires a more powerful processing equipment.
Hot forming
The temperature for hot forming is recommended to be between 1562 and 2102°F (850-1150°C). Normally, next steps of hot forming are annealing and hardening. However, for 904L, if it stops to form when the temperature goes beyond 2012°F (1100°C), the material shall be quenched directly so that the material can be used without subsequent heat treatment. More importantly, the entire workpiece can be quenched when temperature is higher than 2012°F (1100°C). When local heating or cooling is below 2012°F (1100°C), and the cooling goes too slow, hot forming shall follow the subsequent operations of annealing and quenching. 904L shall be annealed between 1940 and 2084°F (1060-1140°C).
Processing
The hardening rate of 904L in cold forming makes it less machinable than 410 and 304 stainless steels.
Welding of 904L Steel
can be welded with most standard workplaces. The austenite plate material has uniform austenite structure and uniform distribution of alloying elements, which may cause the redistribution of certain elements such as molybdenum, chromium and nickel after welding. And the separation of these elements retained in the welded casting tissue will influence the corrosion resistance in some environments. However, element separation is less evident in 904L, and this material is usually welded with filler metal of the same composition as the base metal, or even without filler metal.
Welding material for 904L is 20 25 CuL electrode and 20 25 CuL wire.
Is 904L Super Duplex Steel
As you can see from the chemical elements of 904L above, 904L has a very high nickel content of 23-28% and Cr content of 19-23%. This differs from super duplex steels such as SAF 2507, which have a low Nickel and high Chrome content. We believe that 904L is not a super duplex steel, but a super stainless steel. For 904L stainless steel tube, he namely belongs to This differs from super duplex steels such as SAF2507, which have a low nickel and high Cr content. We believe that 904L is not a super duplex steel, but a super stainless steel. For 904L stainless steel pipe, he namely belongs to ASTM SB677 standard.
904L Stainless Steel Price
We see that 904L has a high nickel content and is a super stainless steel, which is quite expensive. Compared to the common 304,316L stainless steel pipes and fittings, 904L is twice or more expensive than 316L. However, 904L has better corrosion resistance, so in some cases, the customers will still choose 904L rather than give up on it because of its price.
Application of 904L pipe and fittings
- Air Pollution Control: Used in the scrubbers in coal-fired power plants.
- Chemical Processing: Used in the equipment to produce sulfuric acid, phosphoric acid, inorganic and organic acids and phosphate fertilizers.
- Metallurgical Processing: Used in the pickling equipment for sulfuric acid.
- Oil and Gas production: Used in offshore processing equipment.
- Pharmaceutical Industry: Used in processing equipment.
- Pulp and Papermaking: Used in processing equipment.
- Seawater and Brackish Water: Used in condensers, heat exchangers and piping systems.