Continuous casting process, also known as billet casting, is the process of solidifying molten metal into “semi-finished” billets, blooms or slabs, and then rolling them in a finishing mill.
From wiki.
There are two methods for casting duplex stainless steel: die casting and continuous casting. Before the 1960s, most of the duplex steels were die cast. The large-scale popularization of continuous casting technology began after the 1960s, especially after the 1970s. By 1985, the global dual-phase steel continuous casting ratio had reached more than 70%.
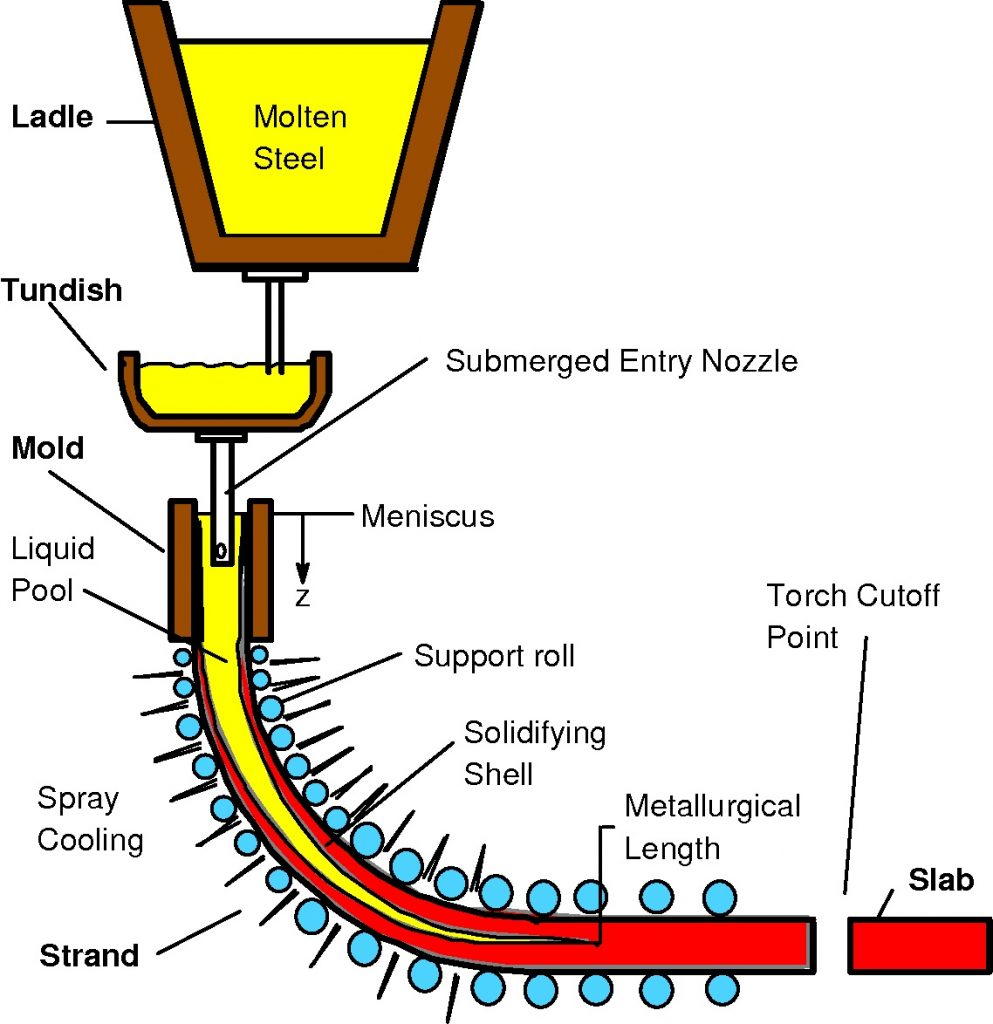
At present, the industrial developed countries basically replace die casting with continuous casting. The use of continuous casting not only improves the yield of molten steel, thereby increases the overall yield rate, and significantly improves production efficiency.
- Duplex stainless steel continuous casting is generally matched with a refining furnace, and the chemical composition and temperature of the molten steel are strictly required;
- In order to prevent secondary oxidation of molten steel, non-oxidation protective pouring is required in the continuous casting production process;
- Strict requirements for practical refractory materials such as ladle, tundish, sliding nozzle, immersion nozzle, etc.;In order to ensure the surface quality of the continuous casting slab, select suitable mold flux;
- During the continuous casting process, the vibration marks formed on the surface of the continuous casting billet due to the vibration of the mold should be controlled;
- Electromagnetic stirring is indispensable for continuous casting of super duplex steel.
Duplex stainless steel generally adopts the same vertical, vertical bending or arc continuous casting machine as carbon steel.
The refined molten steel is poured into the ladle, and the temperature of the molten steel is fine-tuned through the argon blowing station, and then hoisted to the ladle turret to wait for continuous casting.
After the last ladle of molten steel is cast, the ladle to be poured is turned over the injection port of the tundish, and then the molten steel is injected into the tundish through the shroud. The molten steel in the tundish enters the mold through the immersion nozzle for forming and condensation, and is continuously drawn down. The surface layer of the solidified cast slab continues to be rapidly cooled through the secondary cooling zone until the core becomes a solid, and then subjected to fixed-length flame cutting to complete the entire continuous casting process.
The super dual-phase molten steel is changed from ingot to slab process. Its role is not only to increase the yield rate of 10%, save energy and shorten the production cycle, but also because of the perfect quality control methods of continuous casting process, it has become a product quality improvement Necessary means.
Different steel grades can match the vibration process of the mold with the mold flux, so that the depth of the vibration marks on the surface of the cast slab can reach ≤200μm, thereby achieving the goal of basically not grinding and rolling the surface of the stainless steel cast slab.
Posted by KAYSUNS, stainless steel pipe and fittings supplier.