Purpose of heat treatment of titanium and titanium alloys
- Reduce residual stress of heat treatment of titanium generated during the manufacturing process (relieve stress)
- Produces the best combination of ductility, workability and dimensional and structural stability (annealing)
- Increas strength (solution treatment and aging)
- Optimize special properties such as fracture toughness, fatigue strength and high temperature creep strength
In order to obtain selected mechanical properties, various types of annealing treatments (for example, single annealing, double annealing and recrystallization annealing) as well as solution treatment and aging treatment must be carried out.
Stress relief and annealing can be used to prevent preferential chemical attack in certain corrosive environments, prevent deformation (stabilization treatment) and adjust the metal for subsequent forming and manufacturing operations.
Response to heat treatment & Alloy types
The response of titanium and titanium alloys to heat treatment depends on the composition of the metal and the influence of alloying elements on the α-β crystal transformation of titanium.
Keep in mind that not all heat treatment cycles are applicable to all titanium alloys, because the design goals of various alloys are different.
- Alloys Ti-5Al-2Sn-2Zr-4Mo-4Cr and Ti-6Al-2Sn-4Zr-6Mo are designed for strength in heavy sections.
- Alloys Ti- 6Al-2Sn-4Zr-2Mo and Ti-6Al-5Zr-0.5Mo-0.2Si for creep resistance.
- Alloys Ti-6Al-2Nb-1 Ta-1Mo and Ti-6Al-4V, for resistance to stress corrosion in aqueous salt solutions and for high fracture toughness.
- Alloys Ti-5Al-2.5Sn and Ti-2.5Cu for weldability; and
- Ti-6Al-6V-2Sn, Ti-6Al-4V and Ti-10V-2Fe-3Al for high strength at low-to-moderate temperatures.
The influence of alloying elements on the α-β transformation.
Unalloyed titanium is allotrope. Its close-packed hexagonal structure (α phase) becomes a body-centered cubic structure (β phase) at 885°C (1625°F), and the structure remains unchanged at temperatures up to the melting point.
Regarding their influence on the allotropic transformation, the alloying elements in titanium are classified as alpha stabilizers or beta stabilizers. Alpha stabilizers (such as oxygen and aluminum) increase the transition temperature from α to β. Nitrogen and carbon are also stabilizers, but these elements are usually not deliberately added in alloy formulations. Beta stabilizers (such as manganese, chromium, iron, molybdenum, vanadium, and niobium) can reduce the α to β transition temperature, and depending on the amount added, may cause some β phases to remain at room temperature.
Alloy type. According to the type and quantity of alloying elements contained in the titanium alloy, the titanium alloy is classified as α, near α, α-β or β alloy. The response of these alloy types to heat treatment is briefly described below.
Alpha and near-alpha titanium alloys can relieve stress and be annealed, but any type of heat treatment (such as solution beta treatment and aging treatment after quenching) cannot produce high strength in these alloys.
Commercially available beta alloys are actually metastable beta alloys. When these alloys are exposed to selected high temperatures, the remaining β phase will decompose and strengthen. For β alloys, stress relief and aging treatment can be used in combination, and annealing and solution treatment can be the same operation.
α-β alloy is a two-phase alloy, as the name suggests, contains both α and β phases at room temperature. They are the most common and most versatile of the three types of titanium alloys.
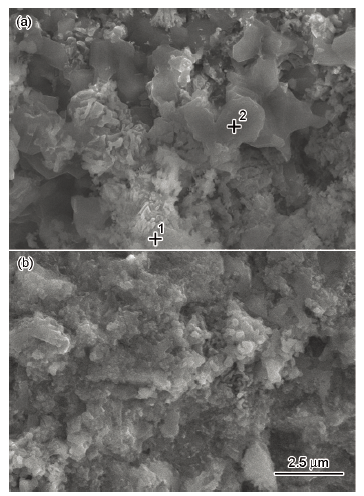
Oxygen and iron levels have significant effects on mechanical properties after heat treatment. It should be realized that:
- Oxygen and iron must be near specified maximums to meet strength levels in certain commercially pure grades
- Oxygen must be near a specified maximum to meet strength levels in solution treated and aged Ti-6Al-4 V
- Oxygen levels must be kept as low as possible to optimize fracture toughness. However, the oxygen level must be high enough to meet tensile strength requirements
- Iron content must be kept as low as possible to optimize creep and stress-rupture properties. Most creep-resistant alloys require iron levels at or below 0.05wt%.
Stress-relieving treatments
Titanium and titanium alloys can relieve stress.
The stress relieving treatment reduces undesirable residual stress:
First, the deformation caused by uneven hot forging or cold forming and straightening,
Second, asymmetric processing of steel plates or forgings, and third, welding and cooling of castings.
Relieving this stress helps maintain shape stability and eliminates disadvantages, such as the loss of compressive yield strength commonly known as the Bauschinger effect.
The annealing of titanium and titanium alloys
Annealing is mainly used to increase fracture toughness, ductility at room temperature, dimensional and thermal stability, and creep resistance.
Many titanium alloys are put into use in an annealed state. Because one or more performance improvements are usually obtained at the expense of some other performance, the annealing cycle should be selected according to the purpose of the treatment.
Common annealing treatment methods are:
- Mill annealing
- Duplex annealing
- Recrystallization annealing
- Beta annealing
Solution Treating & Aging
Through solution and aging treatment, various strength levels can be obtained in α-β or β alloys. In addition to the unique Ti-2.5Cu alloy, the heat treatment response of titanium alloy originates from the instability of high temperature β phase at low temperature.
Heating the α-β alloy to the solution treatment temperature will produce a higher β phase ratio. The phase distribution is maintained by quenching; in the subsequent aging process, the unstable β phase will decompose to provide high strength. Commercially available beta alloys are usually provided under solution treatment conditions and only require aging treatment.
After cleaning, the titanium components should be installed in a fixture or a rack to allow free access to heating and quenching media. The thick and thin components of the same alloy can be solution treated together, but the time at temperature depends on the thickest part.
Table 1 shows the time/temperature combinations used for solution treatment.
Alloy |
Solution temperature [°C] |
Solution time [h] | Cooling rate |
Aging temperature [°C] |
Aging time [h] |
α or near-α alloys | |||||
Ti-8Al-1Mo-1V | 980-1010 | 1 | Oil or water | 565-595 | |
Ti-2.5Cu (IMI 230) | 795-815 | 0,5-1 | Air or water | 390-410 | 8-24 (step 1) |
465-485 | 8 (step2) | ||||
Ti-6Al-2Sn-4Zr-2Mo | 955-980 | 1 | Air | 595 | 8 |
Ti-6Al-5Zr-0.5Mo-0.2Si (IMI 685) | 1040-1060 | 0,5-1 | Oil | 540-560 | 24 |
Ti-5.5Al-3.5Sn-3Zr-1Nb-0.3Mo-0.3Si (IMI 829) | 1040-1060 | 0,5-1 | Air or oil | 615-635 | 2 |
Ti-5.8Al-4Sn-3.5Zr-0.7Nb-0.5Mo-0.3Si (IMI 834) | 1020 | 2 | Oil | 625 | 2 |
α-β alloys | |||||
Ti-6Al-4V | 955-970 | 1 | Water | 480-595 | 4-8 |
955-970 | 1 | Water | 705-760 | 2-4 | |
Ti-6al-6V-2Sn (Cu+Fe) | 885-910 | 1 | Water | 480-595 | 4-8 |
Ti-6Al-2Sn-4Zr-6Mo | 845-890 | 1 | Air | 580-605 | 4-8 |
Ti-4Al-4Mo-2Sn-0.5Si (IMI 550) | 890-910 | 0.5-1 | Air | 490-510 | 24 |
Ti-4Al-4Mo-4Sn-0.5Si (IMI 551) | 890-910 | 0.5-1 | Air | 490-510 | 24 |
Ti-5Al-2Sn-2Zr-4Mo-4Cr | 845-870 | 1 | Air | 580-605 | 4-8 |
Ti-6Al-2Sn-2Zr-2Mo-2Cr-0.25Si | 870-925 | 1 | Water | 480-595 | 4-8 |
β or near-β alloys | |||||
Ti-13V-11Cr-3Al | 775-800 | 1/4-1 | Air or water | 425-480 | 4-100 |
Ti-11.5Mo-6Zr-4.5Sn (Beta III) | 690-790 | 1/8-1 | Air or water | 480-595 | 8-32 |
Ti-3Al-8V-6Cr-4Mo-4Zr (Beta C) | 815-925 | 1 | Water | 455-540 | 8-24 |
Ti-10V-2Fe-3Al | 760-780 | 1 | Water | 495-525 | 8 |
Ti-15V-3Al-3Cr-3Sn | 790-815 | 1/4 | Air | 510-595 | 8-24 |
Recommended solution and aging treatments for titanium alloy
The load can be loaded directly into a furnace operating at the solution processing temperature. Although preheating is not necessary, it can be used to minimize deformation of complex parts.
Beta alloys are usually obtained from manufacturers under solid solution conditions. If reheating is required, the soaking time should only be the time required to obtain complete dissolution. The solution treatment temperature of β alloy is higher than β transformation temperature; because there is no second stage, grain growth can proceed quickly.
α-β alloy. The choice of α-β alloy solution treatment temperature is based on the combination of mechanical properties required after aging. The change of α-β alloy solution treatment temperature will change the content of β phase, thus changing the response to aging.
In order to obtain high strength with sufficient ductility, solution treatment must be performed at a higher temperature in the α-β field, usually 25-85°C (50-150°F) below the β transient line of the alloy. If higher fracture toughness or improved stress corrosion resistance is required, beta annealing or beta solution treatment may be required. However, heat treatment of α-β alloys in the β range will result in a significant decrease in ductility. These alloys are usually solution heat treated to a temperature below the β transformation temperature to obtain the best balance of ductility, fracture toughness, creep and stress fracture properties.
Posted by stainless steel pipe fittings supplier KAYSUNS