Surface roughness is very important for most surfaces involved in sliding contact. This is because factors such as the original rate of wear and sustained nature are highly dependent on this characteristic. These surfaces are generally load-bearing surfaces, and the roughness needs to be marked to ensure the suitability of the intended use.
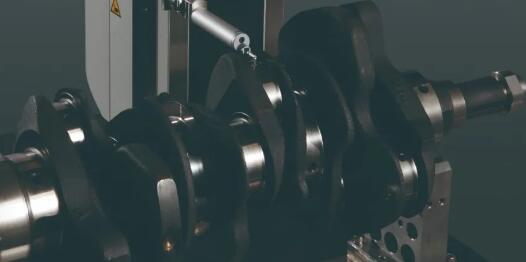
Definition of Surface Roughness
Surface Roughness (SR) is the roughness of surface in our daily measurement, which can be understood as the unevenness of fine pitch and tiny peaks and valleys in the process of processing products.
It is usually defined as the tiny distance (wave distance) between two peaks or two trough fingers. In general, the wave distance is within 1mm or less, and it can also be defined as the measurement of micro-profiles, commonly known as micro-error value .
We generally evaluate that there will be a baseline for roughness. The highest point above the baseline is called the peak point, and the lowest point below the baseline is called the valley point.
Then the height between the peak and the valley is expressed by Z; The distance between the microtextures of the processed product We use S to express.
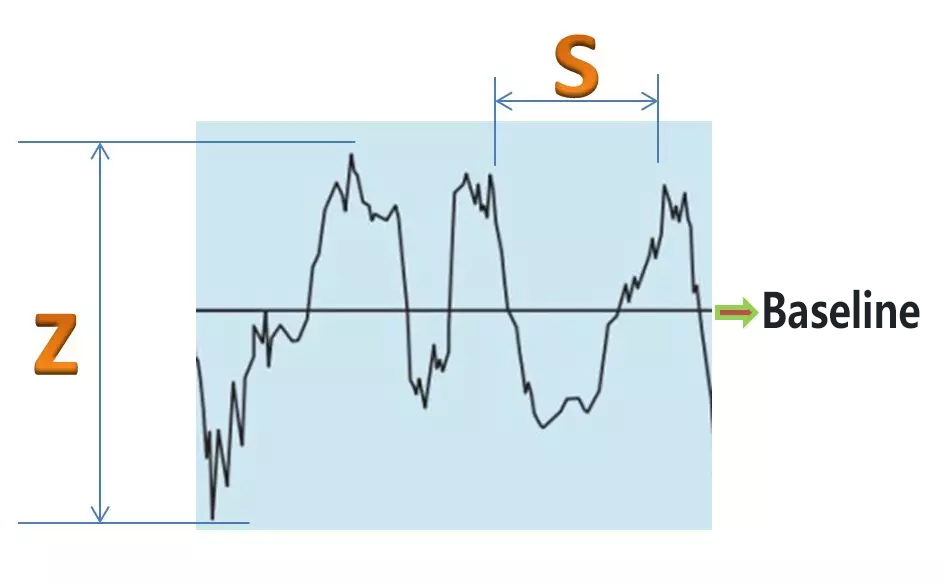
Under normal circumstances, the size of the S value is defined in the national verification standard:
S<1mm is defined as SR
1≤S≤10mm is defined as SR
China’s National Metrology Verification Standard stipulates: Normally, the three parameters of VDA3400, Ra, and Rmax are used to evaluate the verification surface roughness, and the unit of measurement is usually expressed in μm.
Evaluation Parameter Relationship
Ra is defined as the average arithmetic deviation (average roughness) of the curve, Rz is defined as the average height of the unevenness, and Ry is defined as the maximum height.
The maximum height difference Ry of the micro-profile is also expressed by Rmax in other standards.
Please refer to the following table for the specific relationship between Ra and Rmax:
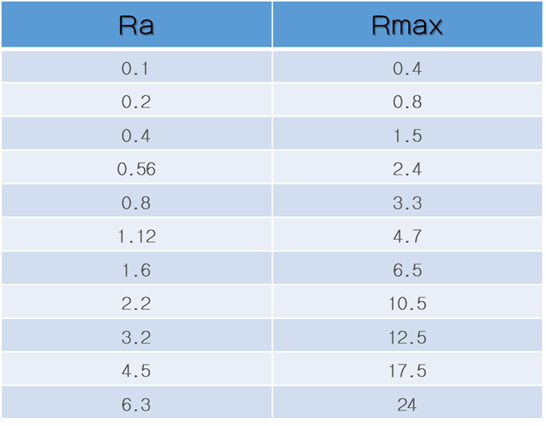
How Is It Formed?
The formation of surface roughness is caused by the machining process of the workpiece. The processing method, the material of the workpiece, and the process are all factors of the surface roughness of the image.
For example: During the electric discharge machining, the surface of the machined part has discharge irregularities.
The processing technology and the material of the parts are different, and there are various differences in the micro marks left on the surface of the processed parts, such as (density, depth, shape change, etc.).
Effect Of Surface Roughness On Workpiece
Workpiece wear resistance
Fit stability
Fatigue strength
Corrosion resistance
Tightness
Contact stiffness
measurement accuracy
…
The coating, thermal conductivity and contact resistance, reflection ability and radiation performance, resistance to the flow of liquids and gases, and the circulation of current on the surface of the conductor will all have varying degrees of influence.
Evaluation Basis
①Sampling length
The unit length of each parameter, the sampling length is the length of a reference line for evaluating the surface roughness. Under the ISO1997 standard, 0.08mm, 0.25mm, 0.8mm, 2.5mm, and 8mm are generally used as the reference length.
②Evaluation length
Consists of N reference lengths. The surface roughness of each part of the surface of the component can not truly reflect the real parameter of roughness on a reference length, but it needs to take N sampling lengths to evaluate the surface roughness. The assessment length under the ISO1997 standard is generally N = 5.
③Baseline
The reference line is the contour center line for evaluating the roughness parameter. Generally, there is a least squares midline and a contour arithmetic mean midline.
[Least Squares Midline] is the least squares calculation of the points collected during the measurement process.
[Arithmetic mean centerline of contour] Within the sampling length, make the area of the two parts of the contour on the midline equal
In theory, the least square midline is an ideal baseline, but it is difficult to obtain in practical applications, so it is generally replaced by the arithmetic mean midline of the contour, and a straight line with an approximate position can be used instead.
How To Obtain The Surface Roughness Value?
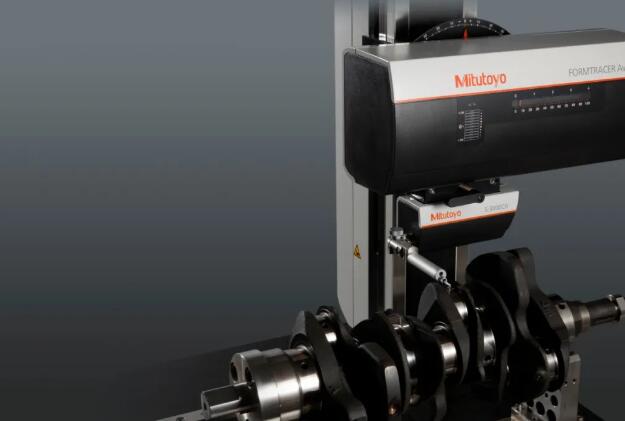
The evaluation of surface roughness is increasingly valued in the manufacturing industry. To study the surface roughness, you need to use a special machine, named: surface roughness measuring instrument.
Most of the correct and complete surface roughness measurement methods, although they use a dedicated measuring machine, but in some cases, for quick and low-cost operation, you can also use hand-held kit tools to measure, as shown below:
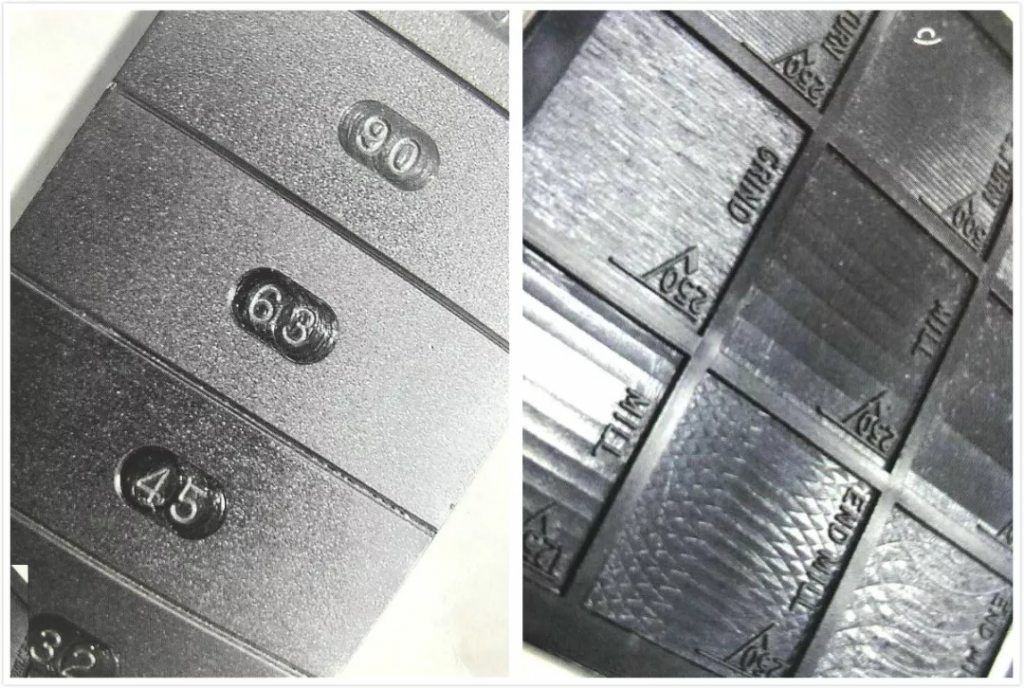
The roughness comparison sheet is a nickel-based sample made by electroforming. It is ideal for metal processing and is a very effective auxiliary tool.
The functions that can be achieved by the roughness measuring machine are different, the evaluation method is different, and the cost is also different. Choose the most suitable model according to needs of stainless steel pipe fittings supplier.