Experiments and results of duplex stainless steel pipe welding
Man has produced and used duplex stainless steel for almost 80 years. Early alloys, such as malleable alloy 329 and cast alloy CD4MCu, contained far more ferrite than austenite.
People do not pay attention to the importance of nitrogen. Many alloys contain very little nitrogen, so that when heat treatment is not performed after welding, the heat affected zone of these alloys usually becomes brittle and has poor corrosion resistance. Gas welding weld metal also has this defect.
In the 1980s, the importance of nitrogen to duplex stainless steel pipes was fully recognized, and the minimum nitrogen content requirements were usually specified. By adding an appropriate nitrogen content to the base metal and using a weld filler metal with an increased nickel content, the weldment can have approximately equal amounts of austenite and ferrite in the welded state, which significantly improves mechanical properties Improved corrosion resistance.
Mistakes
Unreasonable base metal specifications
Over the past 25 years, the most common duplex stainless steel is an alloy called 2205. Almost all of the literature uses UNSS31803’s composition range to describe this alloy. However, UNS S31803 has a minimum nitrogen content of 0.08%.
Practice has proved that this level of nitrogen content is too low, if the heat affected zone and the melting zone are to maintain good performance under post-weld conditions. After realizing this problem, ASTM has used UNSS32205 to define 2205 since 2000.
Table 1 shows the composition range of UNS S31803 and UNS S32205. It is worth noting that, compared with S31803, in addition to increasing the minimum nitrogen content, the minimum chromium and molybdenum content also increased.
Composition table of 2205 duplex stainless steel | |||||||||
UNS | Chemical composition range /% (maximum) | ||||||||
C | Mn | P | S | Si | Cr | Ni | Mo | N | |
S31803 | 0.030 | 2.000 | 0.030 | 0.020 | 1.000 | 21.0~23.0 | 4.5~6.5 | 2.5~3.5 | 0.08~0.20 |
S32205 | 0.030 | 2.000 | 0.030 | 0.020 | 1.000 | 22.0~23.0 | 4.5~6.5 | 3.0~3.5 | 0.14~0.20 |
Table 1
Figure 1 shows the microstructure of the forged steel that conforms to the composition of UNS S31803 but not the composition of UNS S32205, and the distribution of alloy elements between the ferrite phase and the austenite phase. For S32205, the nitrogen content of 0.12% is too low.
In Figure 1 (a), ferrite is darker gray, while austenite is almost white. It can be seen from the figure that the ferrite phase is rich in chromium and molybdenum and the austenite phase is rich in nickel and nitrogen.
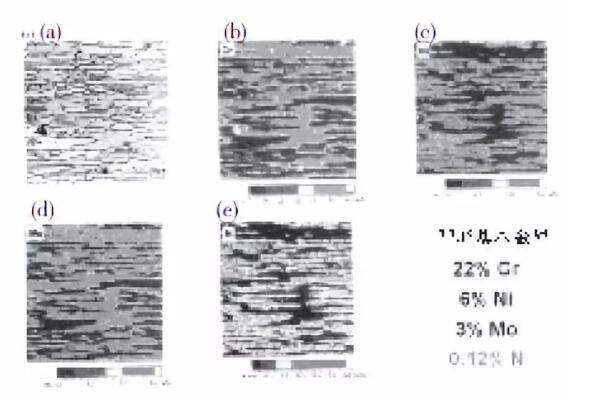
In particular, the content of chromium in the ferrite is about 25% and only 20% in the austenite, as shown in Figure 1 (b). The content of molybdenum in the ferrite is about 3.5%, in the austenite The content of molybdenum is only 2.5%, as shown in Figure 1 (d). The content of nickel in the austenite is 7.5%, and it is about 5% in the ferrite. See Figure 1 (c), the content of nitrogen in the austenite It is about 0.3%, and is zero in the ferrite, as shown in Figure 1 (e).
The distribution of phases is basically balanced. Because steel is a hot-rolled product, the structure is band-shaped.
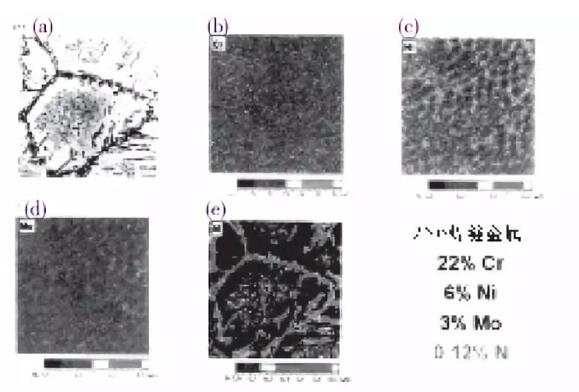
Compared with Figure 1, Figure 2 shows the microstructure and alloying element distribution of the melting zone of the self-fluxing GTA weld of UNSS31803, which is the same as the material in FIG. 1.
It is difficult to see the pattern of alloy element distribution in Figs. 2 (b), 2 (c) or 2 (d) similar to the phase distribution of Fig. 2 (a). However, the nitrogen distribution indicates that the nitrogen concentration in the austenite flakes around the ferrite grain boundaries is higher than that in the ferrite grains. This may be due to the sufficient time for the nitrogen in these regions to diffuse into the austenite on the ferrite grain boundaries, resulting in the region next to the austenite plate containing virtually no nitrogen, as shown in Figure 2 (e).
Inside the ferrite grains, nitrogen is blocked, there is no chance to enter austenite, and it precipitates as chromium nitride, which is clearly visible, as shown in Figure 2 (a). For the melting zone, the combination of large ferrite grains and chromium nitride precipitates is very detrimental to the toughness and corrosion resistance of the melting zone.
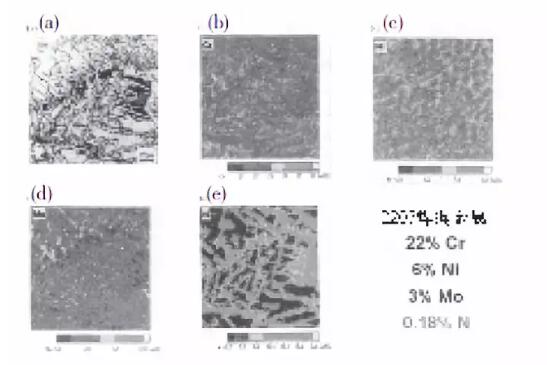
In fact, as mentioned earlier, 100% of the solidification in the melting zone is ferrite. Then, when the transformation to austenite starts, diffusion is required.
Since chromium, nickel, and molybdenum are replacement elements, they diffuse relatively slowly in the solid state, so they cannot achieve a balanced distribution between ferrite and austenite under normal welding cooling conditions. Nitrogen is an interstitial element, and its diffusion rate is about 100 times faster than that of the replacement element. As a result, it has more ability to enter austenite, although the composition is not completely entered as shown in FIG. 2.
In materials containing 0.12% nitrogen, the hottest part of the HAZ behaves similarly to the weld metal. In particular, it is composed of 100% ferrite and then partly transforms into austenite in the solid state. Therefore, it is more inclined to form large ferrite grains and austenite flakes formed along the original ferrite grain boundaries.
Figure 3 shows the microstructure and alloying element distribution in the GTA melting zone when the nitrogen content of 2205 alloy is higher than the nitrogen content shown in Figure 2 and meets the composition limits of UNS S31803 and S32205.
The nitrogen content of the weld metal in Fig. 3 is higher (the nitrogen content is 0.18%, compared with the nitrogen content of Fig. 2 being 0.12%), which significantly changes the microstructure after welding. In particular, it can be clearly seen in Fig. 3 (a) that more austenite is formed than austenite formed in Fig. 2 (a), and the austenite is dispersed through the entire ferrite grains instead of being mainly limited to iron. Element body grain boundary. Compared with FIG. 2 (a), precipitation of chromium nitride is not seen in FIG. 3 (a). Instead, all nitrogen enters the austenite, as shown in Figure 3 (e). Moreover, in Figure 3 (b) and (d), a small distribution of chromium and molybdenum can be clearly seen in this region. Primary ferrite grains.
Due to the higher nitrogen content of this sample, austenite formation may begin at higher temperatures than 0.12% N alloys, and as diffusion and transformation begin at higher temperatures, molybdenum and chromium may diffuse more Faster, the diffusion will take longer. It can also be seen in Fig. 3 (a) that the austenite flakes formed on the entire original ferrite grains shattered the original coarse ferrite grains. As the original ferrite grains are broken into small grains by the internal austenite strips, the toughness is improved. And because no chromium nitride is precipitated, the corrosion resistance is improved. The same is true in the high temperature part of the heat affected zone. In this way, it can be concluded that UNSS32205 with higher nitrogen content in Figure 3 is significantly better than UNS S31803 with lower nitrogen content in Figure 2.
The limit composition of 2550 alloy | ||||||||||
UNS | Chemical composition range /% (maximum) | |||||||||
C | Mn | P | S | Si | Cr | Ni | Mo | N | Cu | |
S32550 | 0.040 | 1.500 | 0.035 | 0.030 | 1.000 | 24.0~27.0 | 4.5~6.5 | 2.9~3.9 | 0.10~0.25 | 1.50~2.50 |
S32520 | 0.030 | 1.500 | 0.030 | 0.020 | 0.800 | 24.0~26.0 | 5.5~8.0 | 3.0~4.0 | 0.20~0.35 | 0.50~2.00 |
Table 2
It is clear that UNS S31803 is not suitable as a base metal for use in the post-weld state, and UNS S32205 should be used. Among duplex stainless steels, UNS S31803 is not the only base metal that is unsuitable for welding structures. The same is true for alloy 255, which is a component of UNS S32550. Table 2 compares the composition of UNSS32550 and UNSS32520 used for surfacing. The composition is generally the same. However, the minimum nitrogen content of UNS S32520 is higher than that of UNS S32550. Obviously, UNS S32520 is more suitable for post-weld applications. In addition, UNSS32550 can also be used, but the nitrogen content of the steel composition must be controlled to the upper limit.
Unreasonable welding heat input
The traditional view of welding heat input is that when welding duplex stainless steel with 22% chromium content, the heat input should be limited to 0.5 ~ 2.5kJ / mm, and when welding super duplex stainless steel with 25% chromium content, the heat input should be limited to 0.5 ~ 1.5kJ / mm.
When a lower heat input is used, even for high-nitrogen-containing duplex steels, austenite is cooled at a very fast rate. Formation is also insufficient. When a higher heat input (> 1.5kJ) is used, under slow cooling conditions, there is a tendency for intermetallic compounds to precipitate in the ferrite. Compared with 22% Cr duplex stainless steel, the trend of 25% Cr super duplex stainless steel is more obvious.
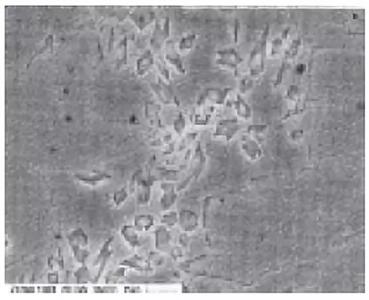
Figure 4 shows the microstructure of the weld metal near the middle thickness of the sample. There are a large number of angular precipitates in the ferrite alone. However, it was not exactly determined what the precipitate was. Our conclusion is that the precipitates were generated by repeated heating during twelve passes of the test specimen.
The normal operation when welding duplex stainless steels, especially super duplex stainless steel pipes, is that the heat input at the root bead is greater than the original fillet. The use of root bead with a thickness of about 6mm is quite good.
Unreasonable post-weld heat treatment
If welded castings or welded heads require post-weld heat treatment, then the use of commonly used nickel-rich filler metals, coupled with the use of unreasonable annealing temperatures that meet basic metal specifications, will cause duplex stainless steel processing manufacturers to commit Another mistake (for duplex stainless steel, nickel content is usually 9%, others are similar to filler metals).
The general requirement is to anneal at a minimum temperature of 1040 ° C and then water quench from the annealing temperature. Because people do not know that the σ phase is almost always formed in the duplex stainless steel during the heating to the annealing temperature, and the higher the nickel content will increase the solid solution phase temperature of the σ phase. In this case, nickel-rich weld metal is dangerous.
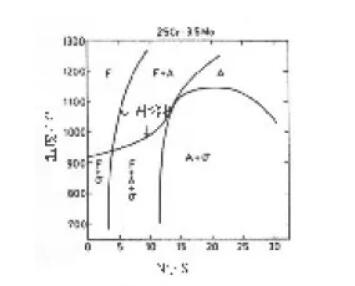
Figure 5 made by Grobner shows the effect of nickel on the solid solution phase temperature of the σ phase of 25% Cr-3.5% Mo alloy.
Although the alloy used to draw this diagram does not contain alloying elements such as manganese, silicon, and nitrogen, it is convenient for people to understand the effect of nickel in nature. It clearly shows that the solid solution phase temperature of the σ phase increases with increasing nickel content. In particular, the σ phase solid solution phase line temperature of the weld metal containing 9% Ni will be at least 50 ° C higher than the σ phase solid solution phase line temperature of the matched base metal containing 5% Ni.
Conclusion
Practice has proved that duplex stainless steel, including super duplex stainless steel, has good welding performance and is a very important engineering material.
However, due to carelessness and ignorance, some mistakes can be made. In order to make the heat affected zone and weld metal have good performance, it is appropriate to use a base metal with a high nitrogen content of at least 0.14% nitrogen. Otherwise, a large amount of ferrite and chromium nitride will be precipitated in the heat affected zone, which will damage the corrosion resistance and mechanical properties.
In order to avoid the precipitation of super duplex stainless steel in the repeated heating area, the use of a large amount of low heat input and small bead should be avoided. And when welding duplex stainless steel and super duplex stainless steel pipes, to prevent precipitation on the inner surface of the pipe, the root bead must use a higher heat input (greater than 1kJ / mm), which is greater than the heat input of the first few continuous welds .
The post-weld annealing of the welded duplex stainless steel needs to take into account the fact that the temperature of the σ phase of the weld metal that dissolves the nickel-rich weld metal is higher than that of the base metal.