Common Problems Of Butt-welded Pipe Fittings
Butt-welded pipe fittings refer to the steel plates that are molded together and welded together to produce a variety of pipe fittings. Butt-welded pipe fittings mainly include butt-welded elbows, butt-welded tees, butt-welded reducers, etc..
The advantages of butt-welded pipe fittings are that they are cheap, the caliber can be made large, the thickness is thin, and the manufacturing process is simple. General pipe fitting manufacturers can produce them.
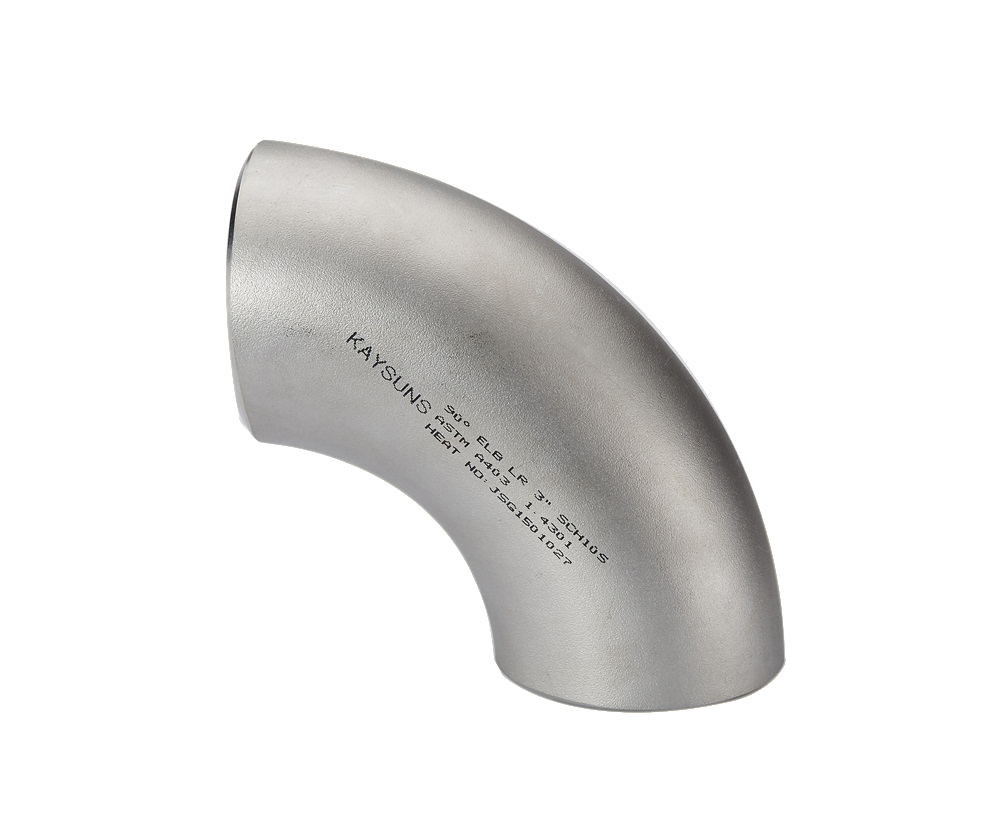
The shortcomings of butt-welded pipe fittings are also obvious. Because the welding process and the molding process are simple, air holes, welds, cracks, etc. are easy to occur, and the pressure is generally less.
Below we will focus on the common defects of welded pipe fittings and how to avoid those problems.
Common defects of butt-welded pipe fittings are prone to pores, cracks, and weak welds. The bubbles are because the burning gas exists in the form of bubbles between the welding gaps, which are generally inside. It is difficult to see. Only by inspection can you find out. The way to avoid is to use fuel with less impurities, and the other is to clean. Weld the appearance of steel plates to remove oil, gas, and moisture.
Crack refers to the crack caused by sulfide entering the weld metal during the manufacture of welded pipe. The reason is that the sulfur segregation zone contains low melting point iron sulfide and the presence of hydrogen in steel. The avoidance measure to be taken is to clean the weld surface. And flux cleaning and drying.
Weak seam refers to the possibility of a gap between the two steel plates of the welded pipe. This has a great impact on the welded pipe. The most direct detection method is to suppress the test water to see if there is any water leakage and avoid measures. It is a good mold, and the specifications and shapes must be made in accordance with the standards. The welded seam is smooth and smooth, and there must be no rust.