flanges, Introduction to Encyclopedia Francisca knowledge.
“Flange” is the abbreviation for “flange”, which is a transliteration of “flange”. It was first proposed by an Englishman named Elchat in 1809 and also proposed a casting method for flanges. However, it was not widely used for a considerable period of time until the early 20th century when flanges were widely used in various mechanical equipment and pipeline connections.
What is a flanges?
A flange, also known as a flange or flange. It usually refers to opening several fixed holes around a disc-shaped metal body to connect other components, and is widely used in various mechanical equipment and pipeline connections. A flange is a component that connects shafts and is used for connecting pipe ends; Also useful are flanges on the inlet and outlet of equipment, used for connecting two devices, such as gearbox flanges.
1. According to the chemical (HG) industry standards:
Integral flange (IF), threaded flange (Th), plate welding flange (PL), neck welding flange (WN), neck welding flange (SO), socket welding flange (SW), welding ring loose sleeve flange (PJ/SE), welding ring loose sleeve flange (PJ/RJ), lined flange cover (BL (S)), flange cover (BL).
2. According to the petrochemical (SH) industry standards:
Thread flange (PT), butt welding flange (WN), flat welding flange (SO), socket welding flange (SW), loose sleeve flange (LJ), flange cover (not specified).
3. According to the mechanical (JB) industry standard:
Integral flange, butt welding flange, plate type flat welding flange, butt welding ring plate loose sleeve flange, flat welding ring plate loose sleeve flange, flanged ring plate loose sleeve flange, flange cover.
4. According to national (GB) standards:
Integral flange, threaded flange, butt welding flange, neck flat welding flange, neck socket welding flange, butt welding ring with neck loose sleeve flange, plate flat welding flange, butt welding ring plate loose sleeve flange, flat welding ring plate loose sleeve flange, flanged ring plate loose sleeve flange, flange cover.
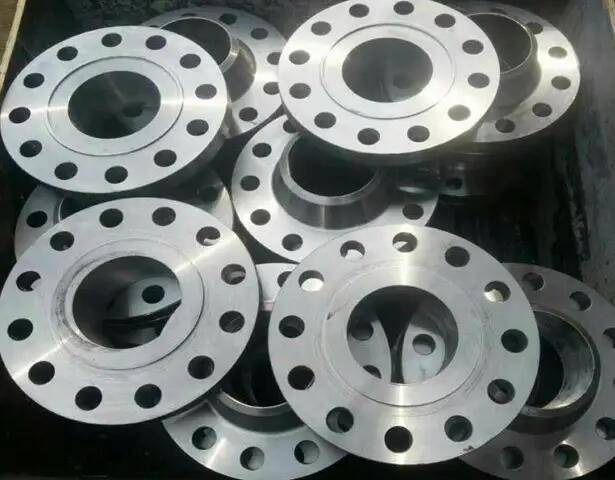
Standard for flanges
As a type of connector, flanges are widely used internationally, which requires a unified standard. For example, there are currently two main standard systems for pipeline flanges, namely the European pipe flange system represented by German DIN (including the former Soviet Union) (DIN, GB, JB, HG20592) and the American pipe flange system represented by American ANSI pipe flanges (including ANSI, GB, HG20615). In addition, there are also Japanese JIS pipe flanges, which are generally only used for public works in petrochemical plants and have a relatively small international impact. Here is a brief introduction to pipe flanges in various countries:
1. European flange system
European flange system: German DIN (including Soviet Union)
Nominal pressure: 0.1, 0.25, 0.6, 1.0, 1.6, 2.5, 4.0, 6.4, 10.0, 16.0, 25.0, 32.0, 40.0, Mpa;
Calculation diameter: 15-600mm;
The structural types of flanges include flat welding plate type, flat welding ring loose sleeve type, rolled edge loose sleeve type, butt welding rolled edge loose sleeve type, butt welding ring loose sleeve type, butt welding type, neck threaded connection type, integral type, and flange cover; The flange sealing surfaces include: flat, concave, convex, tenon and groove surfaces, rubber ring connection surfaces, lens surfaces, and membrane welding surfaces;
The OCT pipe flange registration standard released by the Soviet Union in 1980 is similar to the German DIN standard.
2. American flange system
American flange system: American ANSI B16.5 “Steel pipe flanges and flanged fittings”
Nominal pressure: 150psi (2.0Mpa), 300psi (5.0Mpa), 400psi (6.8Mpa), 600psi (10.0Mpa), 900psi (15.0Mpa), 1500psi (25.0Mpa), 2500psi (42.0Mpa);
Calculation diameter: 6-4000mm;
The structural types of flanges include strip welding, socket welding, threaded connection, loose sleeve, butt welding, and flange cover;
Flange sealing surface: concave convex surface, tenon groove surface, metal ring connection surface.
3. JIS (Japanese standard) pipe flange
JIS pipe flange: It is generally only used for public works in petrochemical plants and has a relatively small impact internationally, without forming an independent system internationally.
The national standard system GB for steel pipe flanges in China.
1. Nominal pressure: 0.25Mpa~42.0Mpa
Series 1: PN1.0, PN1.6, PN2.0, PN5.0, PN10.0, PN15.0, PN25.0, PN42(Main series)
Series 2:PN0.25, PN0.6, PN2.5, PN4.0
The flange sizes of PN0.25, PN0.6, PN1.0, PN1.6, PN2.5, and PN4.0 belong to the European flange system represented by German flanges, while the rest are American flange systems represented by American flanges.
In the GB standard, the maximum nominal pressure level belonging to the European flange system is 4Mpa, and the maximum nominal pressure level belonging to the American flange system is 42Mpa.
2. Nominal diameter: 10mm~4000mm
3. The structural form of the flanges:
Integral flange unit flange
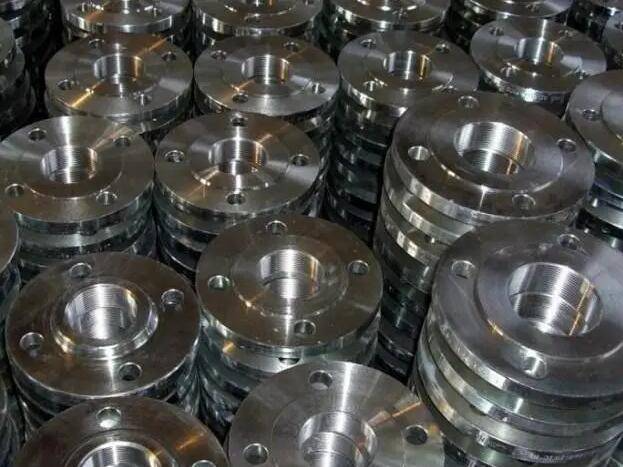
Threaded flange;
Welding flange, butt welding flange;
Neck welding flange, neck socket welding flange, plate welding flange: loose sleeve flange, butt welding ring loose sleeve with neck flange, butt welding ring loose sleeve plate flange, flat welding ring loose sleeve plate flange, plate flipping loose sleeve flange
Blind flange cover (blind hole flange).
4. Sealing surfaces of flanges: flat, concave, convex, tenon and groove surfaces, ring connection surfaces
Flanges assembly
1.Before assembling the flange, it is necessary to clean the flange surface, especially the sealing surface.
2.When assembling flat welding flanges, the pipe end should be inserted into the flange with an inner diameter thickness of 2 ≤ 3, and then the flange should be spot welded to the pipeline. If it is a horizontal pipe, the flange should be spot welded from above, and then the flange position should be checked and corrected from different directions using a 90 ° angle ruler, so that its sealing surface is perpendicular to the centerline of the pipeline. The second point under the spot welding is correct.
3. Use a 90 ° angle ruler to check and correct the position of the flange from the left and right directions. After passing through the third and fourth points, spot weld and fix the flange.
4. For the assembly of flange pairs, the bolt holes for installing the flange should be aligned with the corresponding bolt holes of the fixed flange and parallel to the fixed flange, with a deviation not less than 1.5% of the outer diameter of each thousand flanges, And not greater than 2mm.
When selecting the matching flange for equipment or valve components, attention should be paid to whether the flange of the original equipment or valve component is consistent with the flange connection size used in the pipeline.
Common Soft Cushion Materials
Rubber board and rubber cotton board are the most commonly used flange soft pad materials.
1. Industrial rubber sheet
Rubber sheet, commonly known as industrial rubber sheet, is also known as industrial vulcanized rubber sheet or rubber sheet.
2. Rubber cotton board
Rubber cotton board, also known as asbestos rubber board, is generally used as a gasket for sealing equipment and pipeline flanges. The medium can be water, steam, air, various gases, ammonia, alkali, and oil.
Flanges connection
1. The flange connection should be kept on the same axis, and the center deviation of the bolt hole should not exceed 5% of the hole diameter. The bolt should be freely perforated. The connecting bolts of the flange should have the same specifications, installation direction should be the same, and the bolts should be tightened symmetrically and evenly.
2. Beveled washers of different thicknesses should not be used to compensate for the non parallelism of the flange. Do not use double washers. When large diameter gaskets need to be spliced, they should not be docked with flat ports, but should be in the form of diagonal lap rings or mazes.
3. For the convenience of flange installation and disassembly, the fastening bolts and flange surface shall not be less than 200mm.
4.When tightening the bolts, they should be symmetrical and intersecting to ensure uniform force on the washers.
5. Bolts and nuts should be coated with molybdenum disulfide, graphite oil or graphite powder for subsequent removal: stainless steel, alloy steel bolts and nuts; The design temperature of the pipeline is below 100 ℃ or 0 ℃; Outdoor facilities; Atmospheric corrosion or corrosive media.
6. Before installation, metal washers such as copper, aluminum, and soft steel should be annealed.
7. It is not allowed to directly bury flange connections. The flange connection of buried pipelines should have inspection wells. If it is necessary to bury it, anti-corrosion measures should be taken.