Dye Penetrant Test
What is PT Test
Liquid Penetrant Inspection is also named Dye Penetrant Test, a method of non-destructive testing (NDT). It is a surface inspection method, mainly used to detect surface damage such as cracks that cannot be identified by the naked eye, such as detection of near-surface defects (cracks), porosity, porosity, delamination, failure to weld through and failure to fuse defects in stainless steel materials (also known as “PT” inspection). Suitable for inspection of dense metal materials (welds), non-metallic materials (glass, ceramics, fluoroplastics) and products with open defects on the surface (cracks, porosity, etc.).
As the most commonly used NDT inspection method for stainless steel pipe fittings and stainless steel flange, liquid penetrant inspection is mainly used to detect surface defects of components to find product defects that cannot be seen by the naked eye. PT inspection mainly uses the strong penetration force of the penetrant to penetrate into the surface opening defects, wait for a certain period of time, after removing the excess developer on the surface, and finally spraying the developer to adsorb the penetrant inside the surface defects After waiting for a certain period of time and removing the excess developer from the surface, the final spraying of the developer adsorbs the penetrant from the surface defect and the defect can be observed by the naked eye.
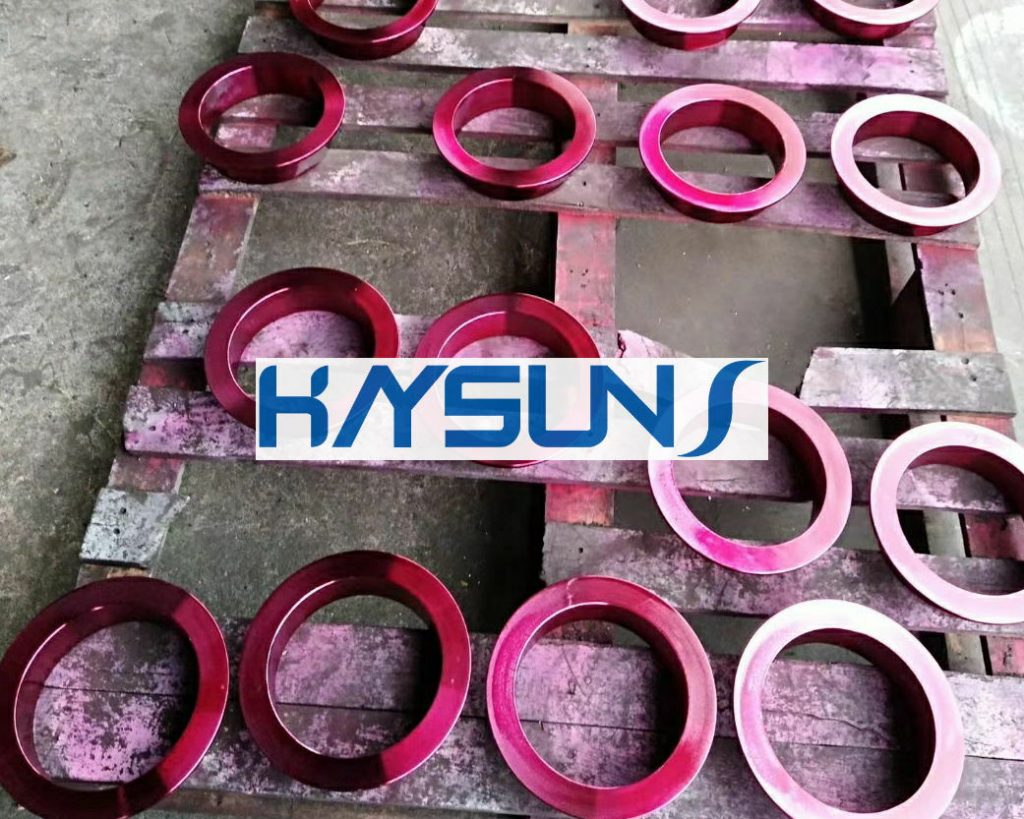
Inspection Process of PT Test
Workpiece surface pre-cleaning
Before applying penetrant on the inspected surface, the surface of the workpiece should be cleaned with a cleaning agent, so that the inspected surface is free of oil, rust, chips, paint and other dirt (such as inspection of the weld, there should be no oxide, slag, spatter and other dirt on the weld surface and the edge of the weld), and then, so that the surface of the inspected workpiece should be fully dry.
Color penetration
After uniformly spraying with penetrant on the surface of the workpiece that has been treated cleanly, penetrate for 5-15 minutes.
Cleaning and drying
After infiltration for 5-15 minutes, before applying the developing agent.
(1) To use a cleaning agent to clean the penetrant sprayed on the surface of the workpiece, making the examined surface to be clean.
(2) Dry with clean gauze or dry naturally at room temperature
Note: When removing excess penetrant, over-cleaning or under-cleaning should be prevented (to ensure that there is no penetrant on the surface of the workpiece).
Imaging
After shaking the image developer well, the surface of the inspected workpiece (cleaned and dried workpiece) should be evenly sprayed at a distance of 150mm-300mm, with a spraying angle of 30°-40°, and the image time should not be less than 7 minutes.
Observation
1、Observation of the traces should start from the application of the developer until the size of the traces does not change, about 7-15 minutes, observation of the image should be carried out within 7~60 minutes after the application of the developer.
2、Observation of the traces must be done under sufficient natural light or white light.
3、To observe the display traces, use the naked eye or 5 – 10 times magnification.
4、If you can’t distinguish between real and fake defective traces, you should retest the part.
Result judgment and record
1, According to the size and color intensity of the traces to determine the size and severity of the defects.
2、The ratio between the length and width of the defective traces is not less than 3 is called linear defective traces, long defects will show the linear traces.
3, the ratio of length to width of the defect traces is less than 3 is called circular defect traces. For example, air holes and other near-circular defects, will show a circular trace.
4, defects show traces, according to the need to record with photographic, schematic or peelable image agent, respectively.
5, in the inspected surface defects show traces of the part for marking.
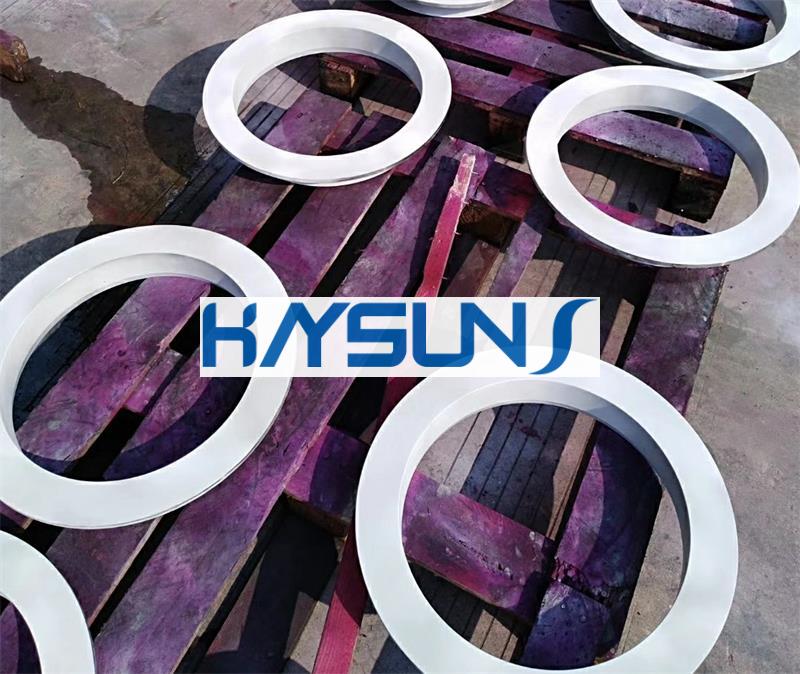
The NTD Report (PT report)
1, the code, name, material, surface state and quantity of the inspected workpiece.
2, the commissioning unit, based on technical documents and flaw detection requirements.
3, the type and type of coloring probe.
4, detection sensitivity (specify the type of contrast test block), flaw detection results.
5, flaw detection personnel, the auditor’s signature.
6, the date of application, the date of the report.
The advantages of PT Test
- simple operation.
- Fast detection speed.
- Low cost.
- Visual display of defects.
- With a fairly high sensitivity, can find defects below 1 micron in width.
It can check out cracks, cold compartments, inclusions, loosening, folding, porosity and other defects; but not for powder metallurgy parts with loose structure and other porous materials.
Frequently Questions of PT Test
Q: What defects can be found by penetrant flaw detection?
As long as the opening to the sample surface defects, can be found by penetrant inspection.
Q: What are the requirements of penetrant flaw detection on the surface of the test sample?
A: The sample surface should be free of rust, dirt, oil, grease or paint and other contaminants that cover the open defects.
Q: Can penetrant flaw detection detect open defects on the surface of stainless steel?
A: Yes, as long as the non-porous material, almost any known material surface open defects, penetrant inspection can be found.
Q: Can penetrant inspection detect surface open defects in forgings?
A: Yes, there is no restriction on the sample structure of the penetrant inspection, castings, forgings, welded parts, machined parts, rolled parts, extruded parts and other surface open defects, penetrant inspection can be found.
Q: Forging surface open defects, penetrant inspection can be found?
A: Yes, there is no restriction on the sample structure of the penetrant inspection, castings, forgings, welded parts, machined parts, rolled parts, extruded parts and other surface open defects, penetrant inspection can be found.
Q: Different defect shapes, sizes and directions will affect the detection effect of penetration?
A: No, except for wide and shallow surface open defects, penetrant inspection is not limited by defect shape (linear defects or volumetric defects), size, and direction, and only one penetrant inspection is required to check all defects open to the surface at the same time.